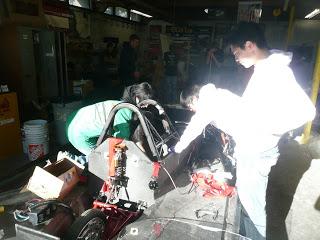
Above: some mechies working on the seat bolting (left to right: Yanyi, Jerry, Stanley, Chris). Below: The team playing hockey at the end of the day.
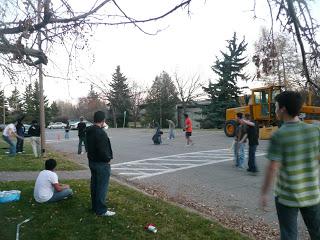
I also made a cut-out of our team logo and glued it onto our seat this past week. The logo was cut from kevlar and a small piece of innegra (which incidentally is a very interesting type of fiber...)
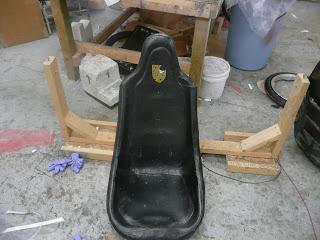
Our previous mechanical manager, Scott Nesbitt, is on his internship in Switzerland, but we try to keep in touch with him since he's still a big part of the team. Usually we talk through back and forth emails, but we gave Skype a shot the other day, and it seems like it might be more useful as we can talk directly, and is also easier in terms of file transfers etc. You can see Scott's epic new apartment below haha.
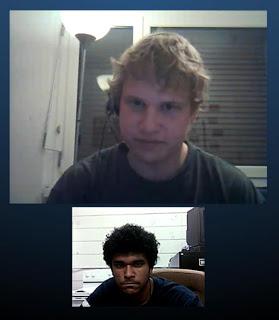
Tim has also been busy working on his MPPT's this week, as well as a prototype steering wheel (which looks really good). He can probably get into more specific detail about revision two of the MPPT's, but below are a couple pictures of both the latest MPPT in progress, and steering wheel.
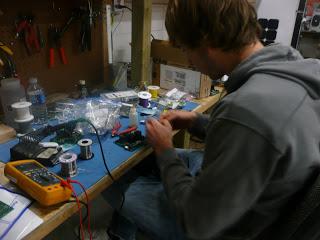
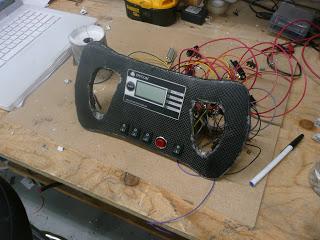
This week, we also did some testing related to certain aspects of our array stand. The design itself is a bit too complex to go into too much detail, but the basic idea is that it consists of two tripods, each with two concentric collars that will slide inside one another, regulating the angle of a bracket that attaches to the top shell. One idea was to have a clamp that could be tightened in the location we wanted, which would have a rubber interface to facilitate the restriction of movement (kind of like the mechanism to tighten the table on some drill presses). We thought about drilling holes through both and using a pin or bolt to secure the collars where we wanted, but this way we can achieve continuous rather than discrete angles. Using the bolt hole idea also created other issues which don't really need to be mentioned. Anyways, we mounted a test sample consisting of some aluminum samples (which were up against different types of rubber) to a tensile machine (with a clevis on the top, and incline wedge grip on the bottom), to see the maximum force each material could take before slippage occurred. Both types of rubber that we tested began to slip at unacceptable levels, so we will be using a different method to hold the collars together.
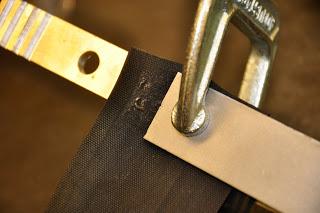
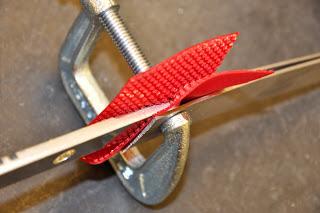
We are also planning on performing some more tests on the carbon fiber tubing samples that we ordered a few weeks ago, and I will keep you guys updated on the results of those tests as well.
That's it for now... talk to you soon!
John Fernando
Mechanical Engineering Manager