Jamie is a sailmaker; he periodically shares his knowledge on the blog, and those posts are under the Sailmaker tag. This is the second post in a two-part series to demystify some of the woo around sailcloth material; you can read the first post here. Anyone with questions about sails is invited to get in touch; Jamie enjoys sharing from his depth of experience as a sailmaker and a cruiser.
Sailcloth comes in so many forms, each exhibiting unique characteristics. It’s easy to see, and understand differences between a Carbon fiber “string” sail and one made from Dacron with crosscut construction. Subtler differences such as fiber quality, weave or lamination methods, and yarn distribution result in specific cloth properties. The real trick to great sails is correctly matching sailcloth with its intended purpose.
In getting back to woven and laminate differences, first consider sail panel geometry. Crosscut sails are simple enough: parallel panels running perpendicular to an imaginary straight line between head and clew. This orients the strong “fill” yarns (running across the panel) to the highest load from head to clew. “Warp” yarns (running the length of the panel) are generally weaker and with more over-under crimp than fill yarns. No fill or warp yarns run parallel to the luff or foot. These constructional strengths and weaknesses result in a strong leech and much bias loading elsewhere. For bias stability (stretch control), woven cloth relies on keeping yarns well locked together by weave tightness and plastic coatings that stiffen the yarns. They do really improve stretch characteristics, but weaving yarns tighter costs more, and plastic coatings make stiff sails that are harder to handle.
Enter the radial sail
Radial and molded sails solve the bias loading problems of crosscut sails. Radial sails use many triangular and trapezoidal panels to maintain load and yarn alignments. This results in panels that can be very long, so the strongest yarns in the cloth are in the warp direction. Molded sails use yarns laid onto a substrate layer representing large sections of a sail (or even the entire sail) by computer controlled machinery according to predetermined load paths. There is hardly a force within the sail that doesn’t have a yarn to prevent stretch; and where there is no yarn there can be layers of film, taffetas, and scrims.
Does this clear benefit of non-woven, radial laminate sails with no bias load and crimp stretch mean they are better than woven crosscut or radial sails? Yes, if you want lighter, stronger, and better shape. You get the feather and the steel, but toughness is more quarterback than linebacker; and costs range from moderately more to untouchable for many a modest sailor. The cost issue is in part because fiber and yarns tend to be exotic: Kevlar, Technora, Twaron, Vectran, and carbon. It’s also because the panel geometry of radial sails wastes much cloth and molded sails require expensive machinery; some even use autoclaves to bond composite layers together.
Cloth integrity
As for toughness, the chemical bonds that bind yarns and films together continue to improve. Chemically bonded sails can include outer layers of polyester taffeta, a layer of very small yarns, loosely woven together that help protect the inner layers from impact and UV damage. Still, woven cloth is yarn mechanically bound together and it’s tougher than chemical bonds that can degrade from flexing, impact damage, and even higher tropical temperature. Also, moisture wicked up by yarns into the lamination can cause mildew to grow. Biocides in the cloth prevent mildew growth for some years, but eventually will fail. Cruising laminate cloths are composites of polyester yarns, film and taffeta, are particularly susceptible to this in the tropics.
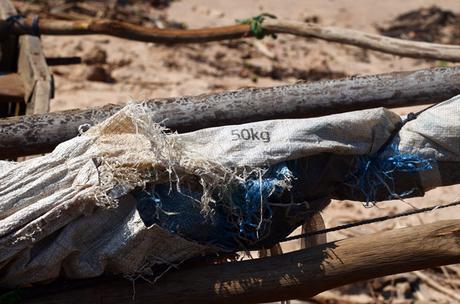
furled sail on an outrigger in Madagascar – a 50 kg sack.
Everything is a compromise
For every great benefit of super fibers or robotic construction method there is a compromise. Some cloth is all compromise – doing nothing very well. If you’re lucky enough to be buying new sails, there is much to balance between cost, longevity, and performance driven by the materials and construction methods. It’s certainly more than techno-speak and pretty pictures. Looking around at the old 50 kg sacks turned into sails power for a dugout canoe, well, it truly is a gift to live where you have options.
Answer to the trivia question in the prior post: the measure refers to the weight for one sailmaker’s yard of the cloth; a sailmaker’s yard is 36” by 28-1/2”.
Any questions from the fleet for our sailmaker?
This post is syndicated on Sailfeed.