Diesel-powered trucks are the engines that keep the wheels of modern business turning, delivering most of the goods used throughout North America. However, for years, those same engines of economic prosperity have been responsible for emitting billows of black smoke full of greenhouse gases and pollutants from their tailpipes.
In fact, according to an MIT study[1], the transportation industry is the single largest contributor to global environmental change. And according to the EPA, on-road vehicles contribute more than 23 percent of total U.S. greenhouse gas emissions. The two major culprits contributing to pollution are particulate matter (PM) and nitrogen oxide (NOx).
New Legislation. Cleaner Vehicles. Fewer Greenhouse Gases.
The good news? Thanks to emissions legislation passed over the past eight years, the emissions equation is steadily re-balancing. The EPA passed legislation in 2007 mandating that commercial vehicles reduce particulate matter from .10 to .01 g-bhp[2] per hour and nitrogen from 2.5 to 1.10 g-bhp.
Then, in 2010, the EPA passed stringent new emissions regulations that further challenged the heavy-duty truck industry to develop cleaner diesel engine solutions. The new emissions limitations directed engine makers to reduce nitrogen-oxide (NOx) from 1.10 to .20 g-bhp per hour.
Further tightening of standards is expected within the next five years. On February 18th of this year, President Obama directed the EPA and NHTSA to work together to develop another round of GHG and fuel efficiency standards for medium- and heavy-duty trucks. The standards, which will impact trucks starting with the 2019 model year, will be proposed by March 2015 and finalized a year later.[3]
The Engine Technologies Driving Change
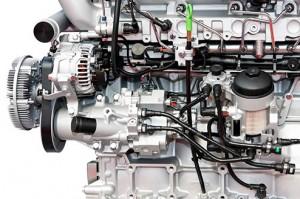
In any case, when the government legislated the latest round of standards for vehicles in 2010, engine makers and vehicle manufacturers got to work developing ways to eliminate nitrogen oxides from diesel exhaust. Essentially, there are two ways to do this: either get rid of NOx after it’s produced or keep it from being produced in the first place. The result of their work – two new technologies based on these approaches:
- Selective Catalytic Reduction (SCR): an after-treatment approach that injects a urea-based fluid, Diesel Exhaust Fluid or DEF, into the exhaust stream to convert unwanted nitrogen oxide (NOx) into nitrogen and water. DEF is consumed at a ratio of roughly two percent compared to diesel, and yields up to five percent fuel economy improvement, making it ideal for long distances.In addition to improvements in fuel economy, SCR technology requires less active regeneration of diesel particulate filters (DPFs). However, it does require a second tank to hold the DEF, which must be refilled regularly.
- Enhanced Exhaust Gas recirculation (EGR): suppresses the creation of NOx during combustion and cleans up the resulting particulate matter in the DPF. EGR does this by lowering the peak combustion temperature by injecting cooled exhaust gas into the intake system. Fuel economy is not as efficient as SCR and produces more particulate matter, but is less complex because it doesn’t require the addition of an on-board fluid (DEF).
The Cost of Clean: New Challenges for Fleet Owners
Thanks to the new engine technologies developed in response to the EPA mandates, diesel trucks run cleaner and quieter today than ever – while preserving the efficiencies and advantages of a diesel engine.
That clean performance comes at a price, though. The cost of the new technologies bumped up acquisition cost of Class 8 vehicles. Second, the complex new engine technologies introduce costly engine problems, downtime and business disruptions for fleet owners. According to Brent Gruber, Director of the Commercial Vehicle Practice at J.D. Power and Associates, owners are impacted financially “because they’re not making money when their trucks are down for service.”
The higher equipment and maintenance costs of the new technologies have an impact on the bottom line. Maintaining the vehicles costs more too, requiring extra steps to keep them operating smoothly. Diesel particulate filters (DPFs must be cleaned out when trucks reach a certain mileage. The cost of cleaning varies, but certainly adds expense.
For fleet managers, DPFs present another potential downside. If particulate matter reaches a certain threshold, the filters clog. When they do, they can interfere with engine operation. To prevent costly engine damage or even shutdown, drivers must regenerate the engines. So that’s something drivers must know how to do – and do.
The Key to Striking the Right Balance
Whether your EPA-compliant vehicles use SCR or EGR technology, keeping them and your business rolling means understanding what DPF and DEF technologies require. So how do you educate your drivers to do what it takes to keep your vehicles on the road? Stay tuned for my next post, where we’ll explore DPF and how to regenerate diesel engines. In a third post, we’ll explore DEF.
Written by. Mr. Mike Dennis, Group Director Maintenance Operations at Ryder. He is an operations professional with over 20 logistics, transportation and maintenance. Throughout his career, Mr. Dennis has played an active role in developing maintenance solutions.
[1] Source: Transportation in a Climate-Constrained World, Andreas Schafer, John B Heywood, Henry D Jacoby and Ian A. Waitz, June 2009
[2] g-bhp = Grams per brake horsepower hour
[3] Source: Cars, Trucks, and Climate: EPA Regulation of Greenhouse Gases from Mobile Sources, The Congressional Research Service, March 2014