Let me just start by saying, natural dye is a process. A process. The turnaround time when it comes to coloring your own fabric is not quick and even Rachael Ray couldn’t make a 30-minute meal out of indigo or pomegranate.
For the past year and a half, my affinity has been in bra and dress making and can you blame me? Who doesn’t love a good dress and a pair of underthings to go underneath? But this project called to me. It was in the middle of summer and during our weekly coffee date when Bekuh said to me, “Hey, you should check out a new blog I found. It’s called Blooming Leopold and it’s right up you’re alley.” Marce once said that finding a new blog was like finding a prize inside a cereal box and she was right. That toy becomes the highlight of the week. Living in my old stomping grounds, Savannah, Georgia, Lauren naturally dyes and sews simple, ethereal dresses. And she provides tutorials on many of her makings too! A month after I introduced myself to her, I sparked up another conversation. “Would you be up for a collaboration? I’ll make it super easy for you. You tell me what to do, I’ll do it, and we’ll both post about it on our blogs.” She agreed and since September, when she sent me her dyeing steps and tips, this project has slowly come together. The long process wasn’t a hindrance to my other projects either, as I sat in front of my sewing machine, this project was either cooking, cooling, or drying.
Later this week and in a super cool layout, I will visually show you each step of my natural dye process (plus tips!), but below is the story and the construction of the dress.
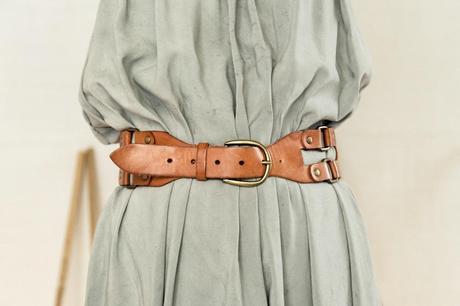
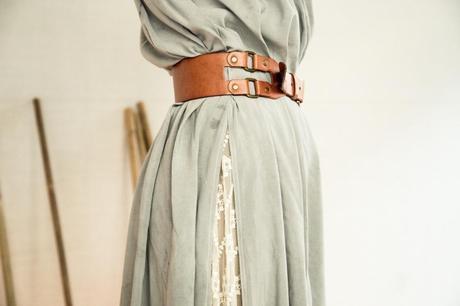

Because this was my first dye natural dye project ever, Lauren and I kept things simple and chose solid color design. Also, even though I admire the beauty of a shibori-like motif, it’s not my style. Before choosing the pattern, I bought the dye and the fabric – alkanet and bamboo rayon. I love purples and magentas, especially with my hair and skin tone, and bamboo rayon is just heavenly. Have you ever had your hands on the fabric? It’s light and airy and smooth as butt-ah. While my supplies shipped from Dharma Trading Company, I began looking for the pattern. I wanted the standout feature of the dress to be the fabric, so I chose a pattern that had lots of it - McCall’s 3912 (I omitted the sleeves).
The interesting thing about alkanet, which is the name of several plants in the borage family that give a red / purple color, is that it’s not water soluble. Under most circumstances, natural dyes are simmered anywhere between 1 to 3 hours prior to dyeing the fabric and the mixture is then left to cool, strained (to remove roots and powder), and then used as the dye bath. When I left alkanet over a stove for 3 hours, the mixture was light grey, not purple, and a test swatch barely picked up color. I emailed Lauren in a panic, but she calmed my nerves and wrote that most reviews said alkanet produced more of a greyish than purple tone and that I should double the amount of dye I used. I agreed and we decided to do another batch, this time increasing alkanet to 1 pound, the following weekend. On a whim, I called Dharma to see what they had to say about my first test. The packaging of the alkanet said to soak the roots in a bath of isopropyl alcohol for up to two days, but because Lauren’s directions didn’t include this step, I left it out. Turns out, alkanet roots don’t release their color in heated water like other natural dyes. The only way to get it to dye is by leaving it in rubbing alcohol. So, that what I did and for two days and boy, did my apartment wreak! Sorry neighbors.
The coloring of the fabric didn’t come out as I intended, I was going for a charcoal grey, but I love it. It’s not purple, but it’s not gray. It’s somewhere in between and both colors shine through just slightly. Because I dyed so much yardage at one time, the coloring was mottled and uneven, but the imperfections were consistent so it looks like it was the intention.
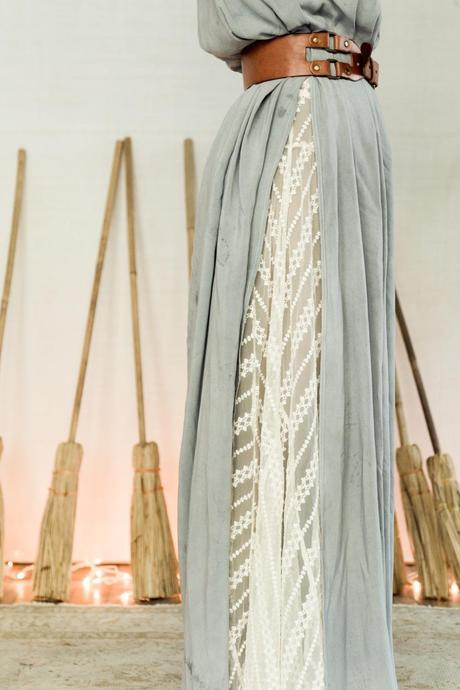
The construction of the dress was simple. Inspired by kimonos, I left the side seams open at 5″ below the armhole and wore this slip underneath. Both the side seams and bottom hem have a 1/4″ double turnback and the armhole was finished with self bias binding. To make sewing the side seams easier, I switched the order of operations. First, I finished the edges, and then I sewed the seam. For me, it was easier to make a tiny hem such as a ¼” double turnback when the side seams are open. The neckband was clean finished to the body and the top ply (layer) was fused with my newest obsession, Pro Sheer Elegance Light. People, I don’t think I’ll ever go back to Joann’s-bought interfacing again. This interfacing doesn’t shrink or bubble, and comes with clear instructions and maintenance guidelines. Interfacing for dummies.
Summer, fall, winter, or spring, this dress works. The design doesn’t fit in with my usual style, I’m drawn to structured fabrics and silhouettes, but this project taught me that I can look and feel good in garments outside my comfort zone.
Thank you Lauren for being patient with me for the past couple of months! Our hard work definitely paid off.
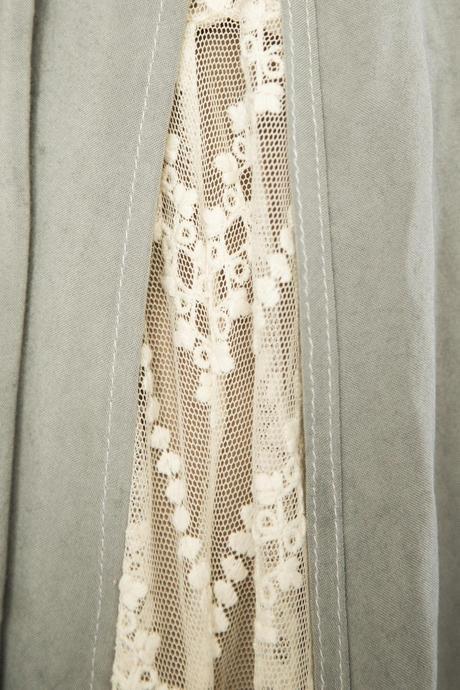
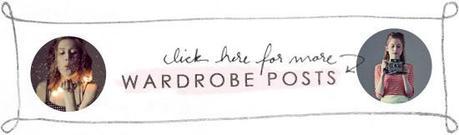