The techniques and strategies used by gas production companies and suppliers for cylinder management were not always as systematic and efficient as they are today. During the early years of the 90s, they were struggling to uphold their reputation and maintain their status due to the emergence of several new gas firms previously considered as underdogs. Growing competition led to a steady decline in prices, which was regarded as a necessary evil for satisfying increasing gas cylinder demands. It was becoming extremely difficult for the existing big companies to invest large sums for cylinder tracking. The problems were magnified even more by demands from customers for reliable records. For overcoming the intense pressure, the companies adopted barcode technology for the time being.
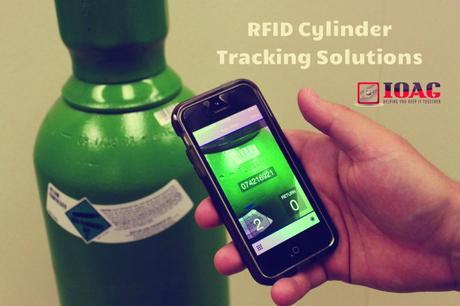
Barcodes remained popular due to their affordability for several decades. However, they had some major drawbacks that came into attention of the owners not until a long time had passed. The disadvantages included low storage capacity, high sensitivity to moisture and dirt, non-rewriteability, expensive and complicated printers, and necessity of manual labor to read tags. Factors such as rising competition, fluctuating economy and pressure for meeting increased demands forced companies to hunt for alternative cylinder tracking methods. Some companies took a step forward and switched to a new technology known as Radio Frequency Identification (RFID).
The new RFID technology turned out to be more cost-effective and reliable than barcodes. There was no need for human capital, but only three components – tags, scanning antenna and transceiver. RFID solutions for cylinder tracking automated the entire process. Each unit now had a unique tag that was read automatically by on-site readers. The readers had connection with a computer responsible for operating the system software. Whenever a cylinder was moved from one place to another, this software automatically updated the inventory.
Soon after, RFID service providing companies were established, and the technology completely revolutionised the pre-existing systems of cylinder management. No more hassles were faced in maintaining delivery records, which resulted in almost zero loss of cylinders annually.
Nowadays, the cylinders arrive at the site of users with RFID tags containing all sorts of essential information like fill date, serial number, cylinder contents and expiration date. Information about the liquid level and operating pressure of the cylinders can also be extracted from the tags. As such, it has become much easier to operate and maintain an accurate manual inventory. Many improvements are being introduced from time to time for increasing the efficiency of the RFID system.

