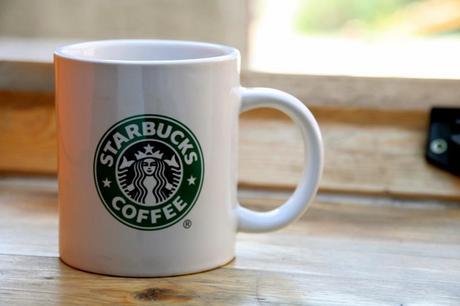
More than just a neat idea, there are (at least) two practical reasons for this type of assembly. The first is that it will almost certainly reduce the cost of store construction. Peter DeMaria, owner of an architectural firm that has experience building with shipping containers, stated that construction in residential applications (like this home in Redondo Beach, California) usually cut costs by 20 percent, and the amount of construction time by up to 40 percent in certain applications. The other reason is that since shipping containers are very portable, they may open up new business opportunities. A Starbucks spokesman gave the example that a store could be assembled in temporarily available locations, and later be transported and reassembled elsewhere. It seems this might also be a good way to test new locations before investing larger sums of money on permanent structures.
There is also a case to be made for this type of construction as it pertains to the environment. According to SG Blocks, a company that retrofits shipping containers, it takes nearly 8,000 kWh to recycle a four-ton shipping container, but only 400 to 800 kWh to convert the same container into an SG Blocks unit. Due to the amount of energy needed to melt the containers, the company says the reclamation process is uneconomical. By reusing the containers, the demand for new steel and lumber that would have been used in traditional construction is also reduced.
Image by rudolf_shuba