The holiday season has passed, but now there is a different kind of hustle and bustle taking place in the retail world – the return of merchandise. January and February mark the busiest months of the year for holiday returns, with returns adding up to about 10 percent of overall sales.
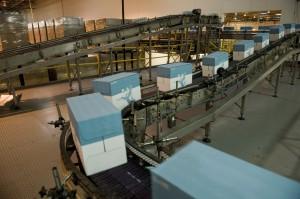
As online shopping becomes more prevalent, the rates of product return post-holidays have significantly increased. Returned goods from online sales make up 20 to 30 percent of all merchandise returned to retailers. This means that retailers need to find a quick, cost-effective and sustainable way of disposing, recycling, or reselling products that have re-entered their supply chains. That’s where reverse logistics comes in.
Reverse logistics, also known as returns management, is the process of managing the movement of goods from the point of consumption back to the point of origin. For nearly all manufacturers and retailers, returned products equal a lost sale. In order for this not to hit a retailers bottom line, they must maximize the value of that returned asset as fast as possible. For example, more than 70 percent of the merchandise returned in the consumer electronics and hi-tech industry has nothing wrong with it. The faster those products can be repackaged and made available for re-sale, the faster a company can recover their value.
As more and more companies are starting to focus on their reverse logistics operations, they are finding that running their operation efficiently can be challenging. A well-run reverse logistics operation can be complex and labor intensive for a few reasons.
1) The returns process generally includes logistics, transportation, triage and testing, depot repair, sales and marketing of refurbished products, finance (validating warranty repairs), customer service and channel management.
2) There is a great deal of physical handling of the returned products to determine the right disposition (should it be repaired, refurbished, scrapped, recycled, repackaged).
3) Employees need specialized training depending on the types of goods they are handling (consumer electronics, appliances, apparel).
4) Technology solutions have to be customized to track the products through every step and manage credit reconciliations and compliance related issues.
To overcome some of the complexities companies face with their reverse operations, they are looking into how they can use a co-location strategy to integrate their reverse logistics operation with their regular distribution network. Because they often lack the visibility needed to do something of this nature, more companies are turning to 3PLs for help.
Because of greater competitive and economic pressures, companies are viewing their reverse logistics operations as a competitive advantage, a new revenue stream versus just a cost a center. Businesses want more control of their supply chain operations and with reverse logistics, this means increased efficiency in recovering, inspecting, testing, disposing and re-selling of returned products. As product life cycles shorten, particularly in the consumer electronics industry, the speed of the reverse supply chain is paramount.
Effective handling of returned goods is not just good for businesses, but also good for the planet. Reverse logistics is also aligned with environmental sustainability. When companies maximize tons per mile, consolidate shipments, reduce returns and optimize the disposition and asset recovery process, they are simultaneously reducing harmful emissions and energy use. An effective reverse logistics strategy is actually the ultimate recycling process. So reverse logistics can also help meet corporate sustainability goals, as well as reduce a company’s carbon footprint.
By unlocking the hidden value of reverse logistics, companies can manage their bottom lines, improve competitiveness and operate more sustainably. It’s truly the gift that keeps on giving.
To learn more about Reverse Logistics, download our white paper here.
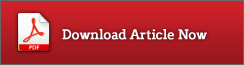
Written by Steve Sensing, Vice President & General Manager, Hi-Tech/Electronics