The skies were leaden gray our first morning in the town of Waterford, and the shimmer on the street below our hotel window betrayed a light drizzle that had dampened the area. The House of Waterford Crystal was a short walk from the Granville Hotel so we were not deterred by the weather but set out on foot to check out the world-famous crystal manufacturer.
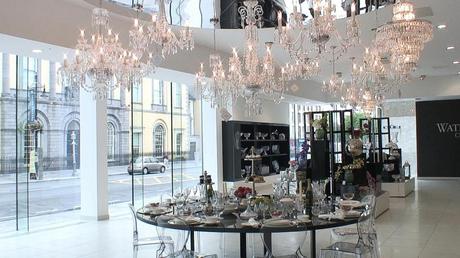
Immediately that we entered the front end of the business, we were bedazzled by the shimmering surfaces of so much crystal. The ceiling of the showroom, alone, was hung with dozens of elaborate chandeliers.
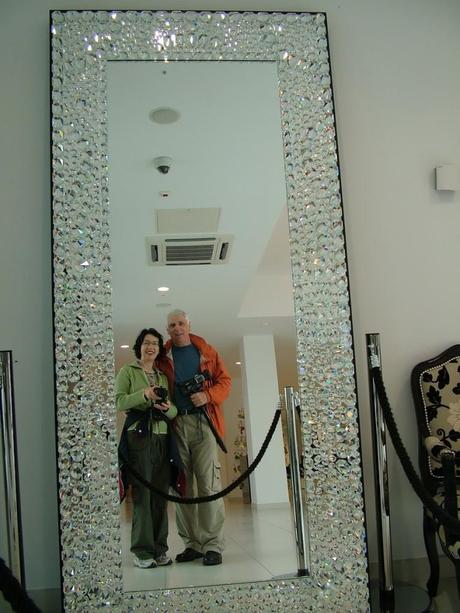
While waiting for our guided tour of the workings of the factory, Bob and I passed the time perusing hundreds of pieces of crystal for sale in the retail store and on display in the showroom. The workmanship was outstanding, and the price tags sky high. Here, you see us reflected in a massive mirror that is edged with hundreds of individually cut crystal pieces.
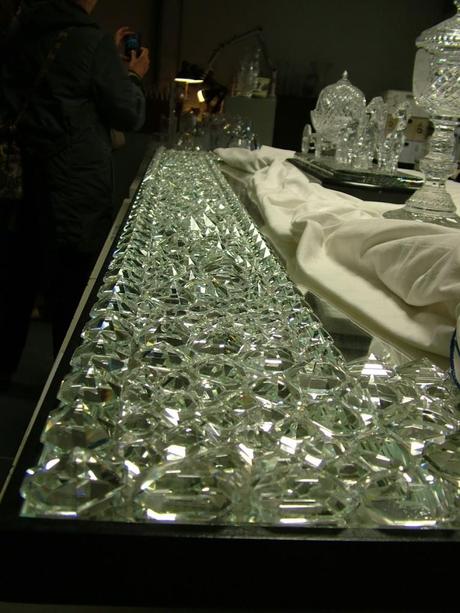
Later, on the tour, we came across the frame of another similar mirror as it was being assembled.
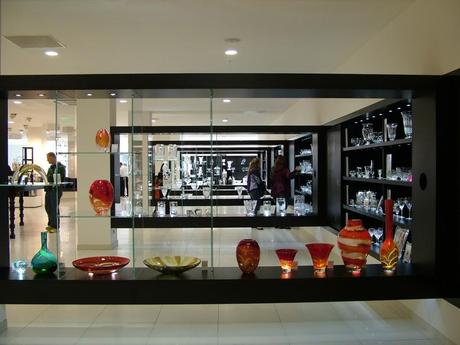
The House of Waterford Crystal features the largest collection of the world’s most coveted crystal right there in the opulent retail store. I love coloured glass so was immediately drawn to the vibrant vases and bowls that so sharply contrasted the clear crystal of most of the other pieces.
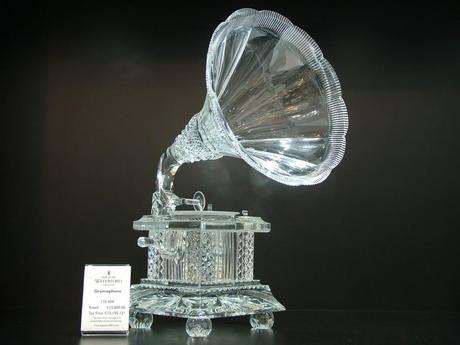
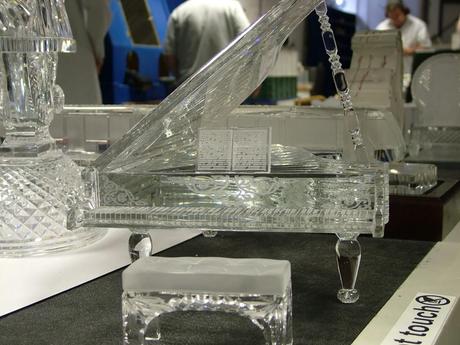
The artistry of the pieces ranged from delicate and diminutive…
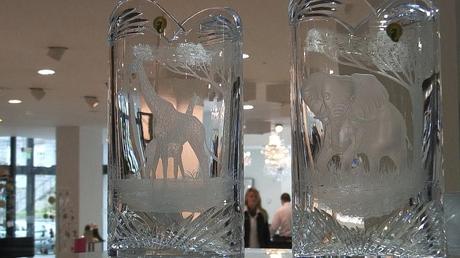
to sturdy and tall, and each was created to exacting standards.
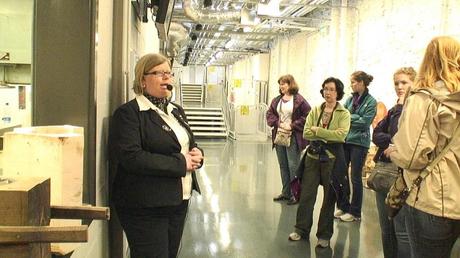
Finally, we were ready to start the tour of the Waterford Crystal plant, joined by a dozen or so other guests.
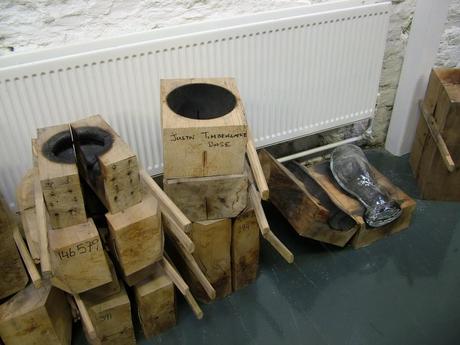
The first area we visited was the Molding Department. Wooden molds are constructed out of beech and pear wood because they have a high tolerance to heat. Molten glass is poured into the molds to form the crystal shapes. Some previously-used molds were on exhibit including one for a product that had been commissioned to do with Justin Timberlake.
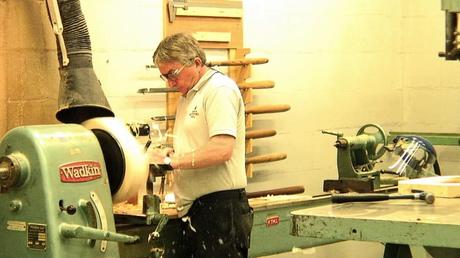
The wooden molds are made by hand as they have been for hundreds of years. Here, we see a wood carver in action. For Bob, this was particularly interesting since he, himself, carves wood as a hobby.
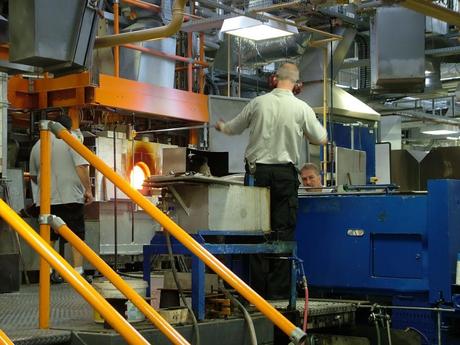
Next up on our walking tour was the Blowing Room where our senses were affronted by a heady mix of heat, cacophonous noise and bustling activity.
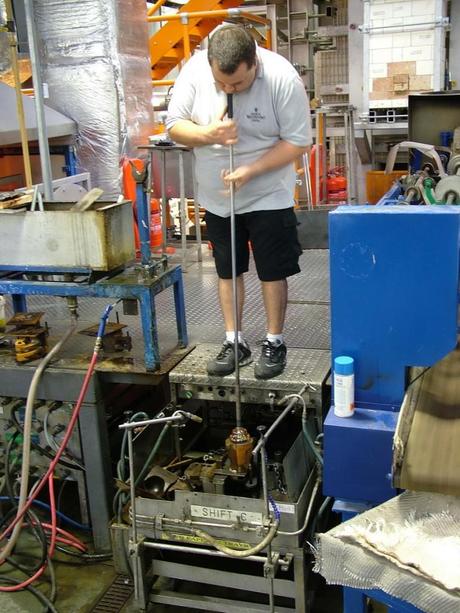
It was very exciting as we edged ever closer to the 1300-degree furnace.
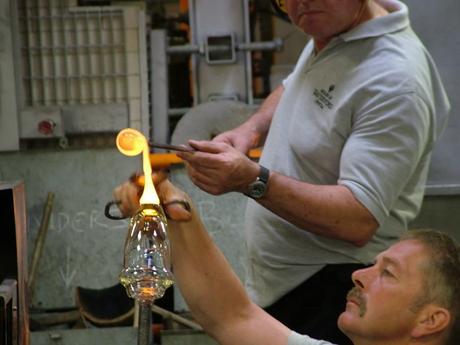
Before our eyes, we saw glowing balls of red-hot molten crystal transformed into wondrous elegant shapes.
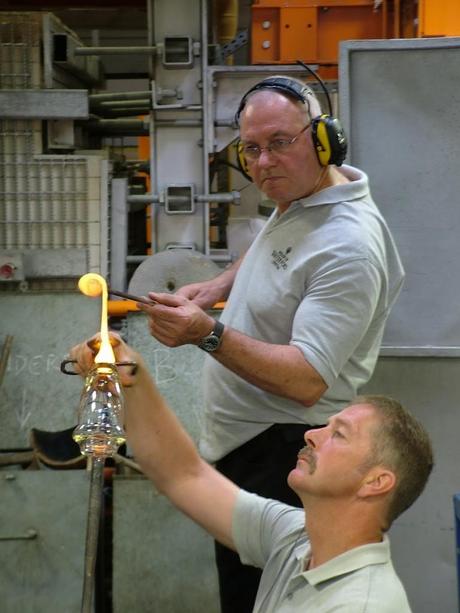
The miracle of this transformation is owing to the meticulous skilled craftsmen who have two hundred years of accumulated knowledge behind them.
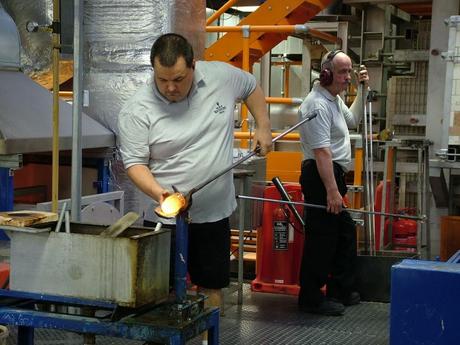
Over and over again, the craftsmen repeated the process with each piece essentially identical to the last.
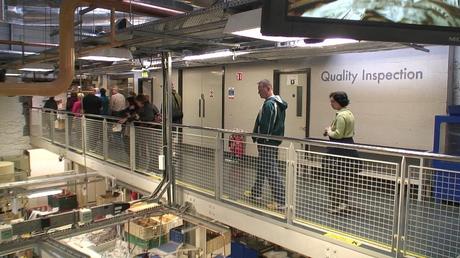
Once each piece of crystal is fashioned into its final shape, it is sent to the Quality Inspection Room where it must pass a stringent examination for faults. Even if a piece is rejected, it will be smashed and remelted to use again.
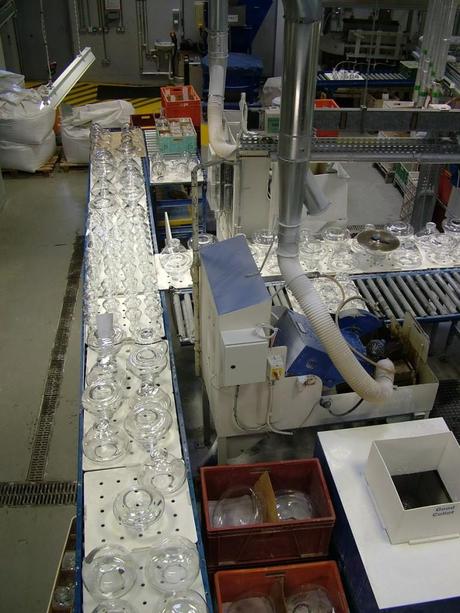
Those pieces accepted as meeting Waterford’s high quality standards wait to be sent to the next stage of production.
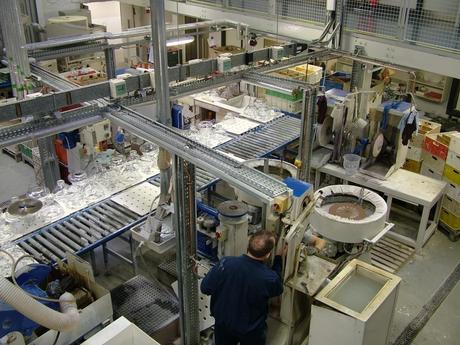
It was mind boggling how so many pieces could look exactly alike when being individually handmade.
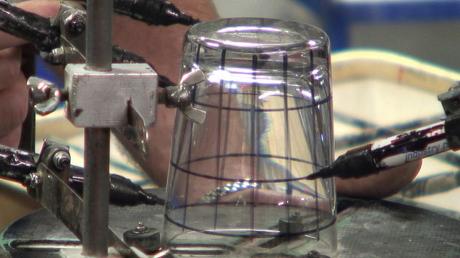
At the next stage of production, the uniform crystal figures are each marked in preparation for cutting the patterns into the glass.
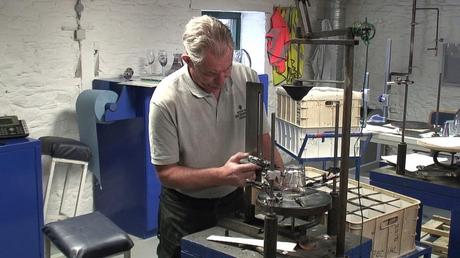
This next stage of production takes place in the Marking Room where finely calibrated tools aid the craftsmen in hand-marking each piece of the crystal in precisely the same pattern, for those that are duplicates of one another. There is no room for shaky lines at this task.
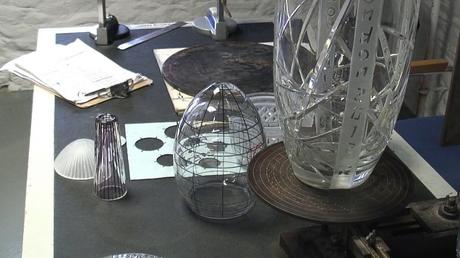
The variety of geometric patterns, including horizontal and vertical lines, are drawn on with a marker, but no trace of the lines will remain after the final cleaning process.
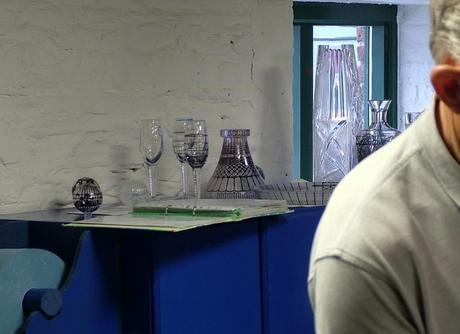
Examples of some of the detailed marking could be seen on pieces set to one side. Some of the line patterns are extremely detailed representing very fine work.
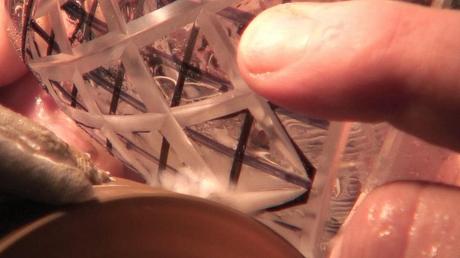
Once the pieces of crystal move on to the Cutting Room, the geometric patterns are assessed before cutting begins.
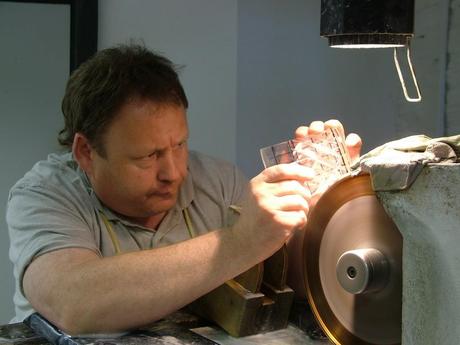
During his training years, each Master Cutter will have learned and memorized each pattern used by Waterford Crystal. The temporary geometric grid only serves to assist the Master Cutter.
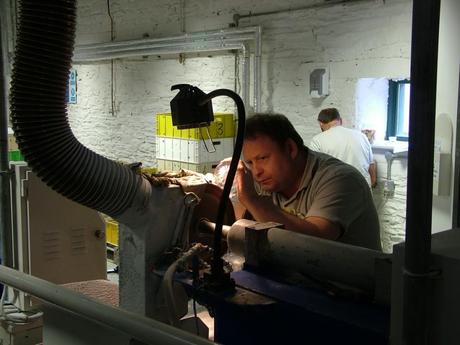
Great focus and attention to detail is required by each Master Cutter when cutting the pattern into the crystal.
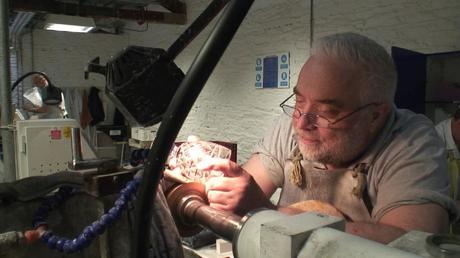
Despite the demands of their jobs…
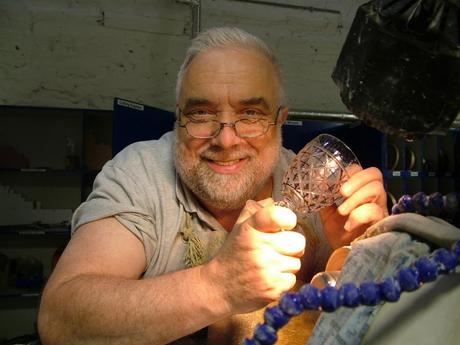
each craftsman in the factory was affable and keenly willing to share their knowledge with us.
As you see in our video, we learned a lot from speaking firsthand with the craftsmen during the hour and a half tour.
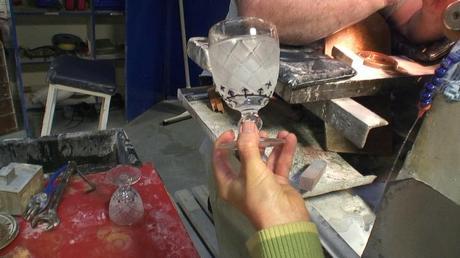
Our close proximity to each workstation allowed a very close look at the ongoing work. Here, I am scrutinizing one of the Waterford crystal goblets from the set the cutter was working on.
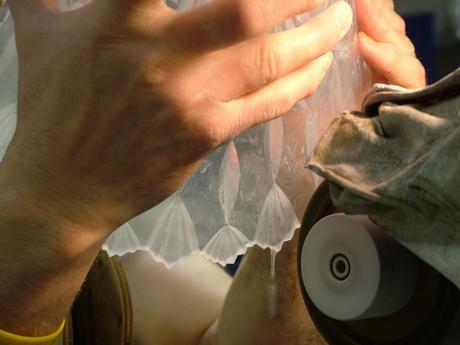
Each Master Cutter that we observed was specializing in one type of product. It was interesting to watch them manipulate some of the larger pieces such as this vase against the diamond-tipped wheels. They must exercise their own judgment when applying pressure for too much will have the wheel cutting right through the crystal.
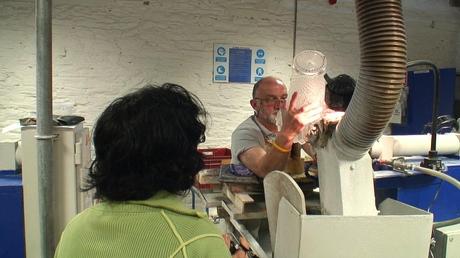
Each Master Cutter trained for 8 years or more to master their craft, and each is responsible for giving every piece of crystal the clear and sparkling cut that is the distinctive hallmark of Waterford products.
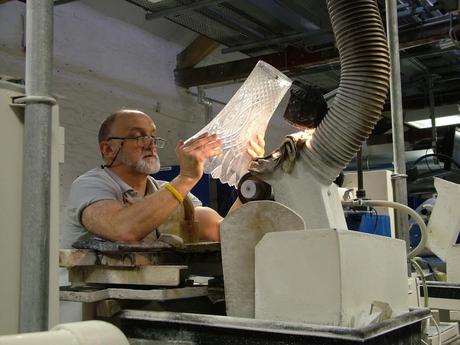
It was easy to see why Waterford Crystal demands such a high price when you consider the hours of work that go into each and every piece of crystal.
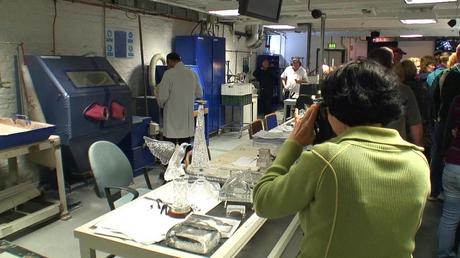
Towards the end of the tour, a series of tables was loaded with items on display that featured examples of sculpted and/or engraved crystal.
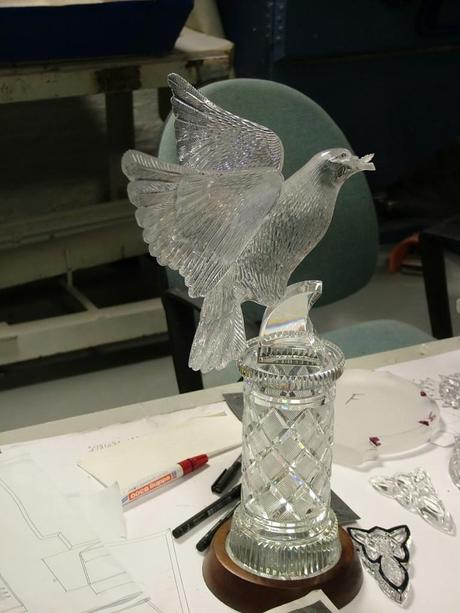
A Master Sculptor uses wheels to sculpt the crystal unlike the mallets and chisels that are employed when carving wood or stone. Because a sculpture is sculpted from a solid block of crystal, it may take days, weeks or even months to complete one piece.

When we entered the Engraving Room, it was a shock to see one engraver working on the skyline of our hometown, Toronto, Ontario. Nicely filling one side of a massive bowl, the skyline featured, among other things, the CN Tower and the Air Canada Centre.
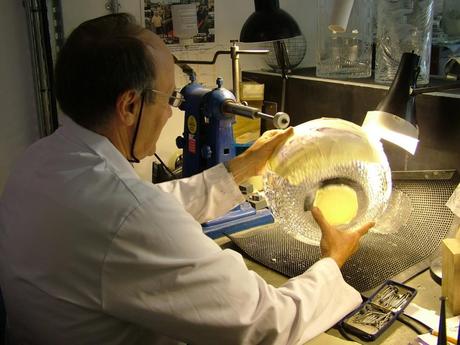
The bowl was commissioned as the trophy for the Honda Indy car race held in Toronto.
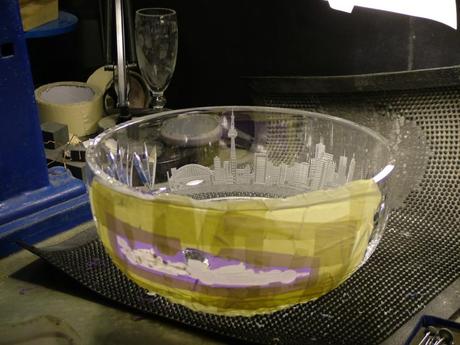
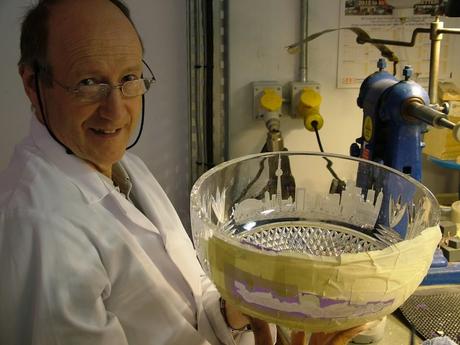
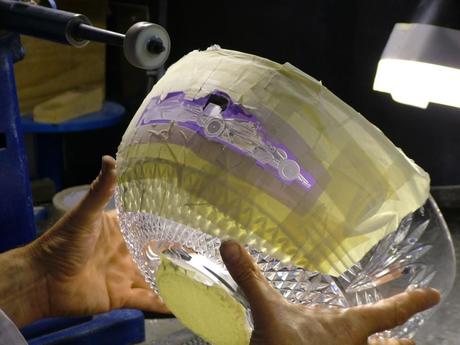
On the opposite side of the massive international trophy, the engraver had fashioned a number of Indy race cars.
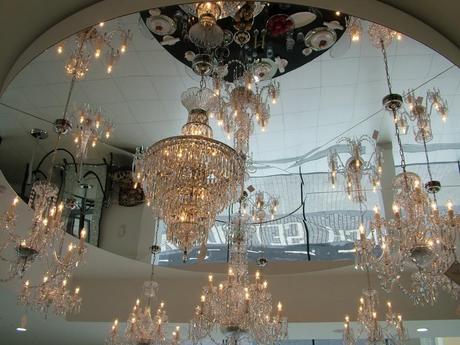
And so, with the tour completed, Bob and I retired to the showroom once again to revel in the stunning display of crystal wares.
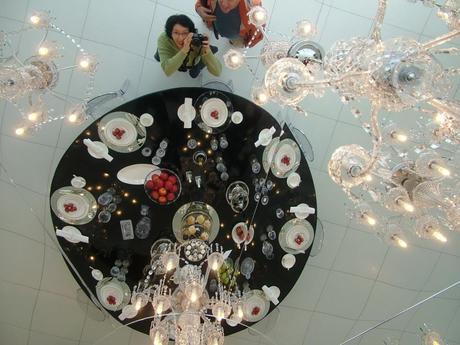
We had fun taking pictures of the mirrored ceiling that so beautifully reflected the glistening and glimmering crystal chandeliers as well as the elegantly appointed dinner table that showcased lots of sparkling stemware.
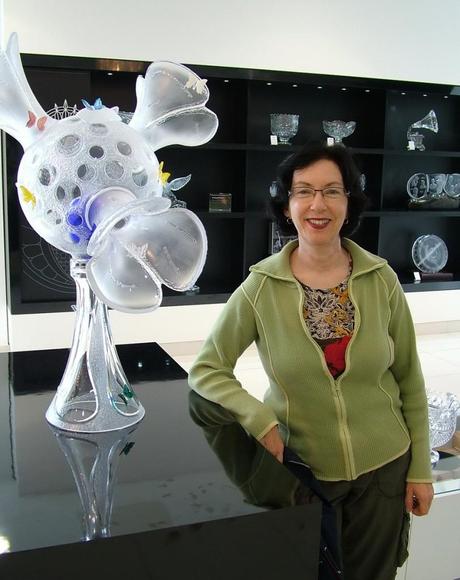
Other crystal pieces made us laugh for their modern take on sculpture. Whimsy is always in fashion.
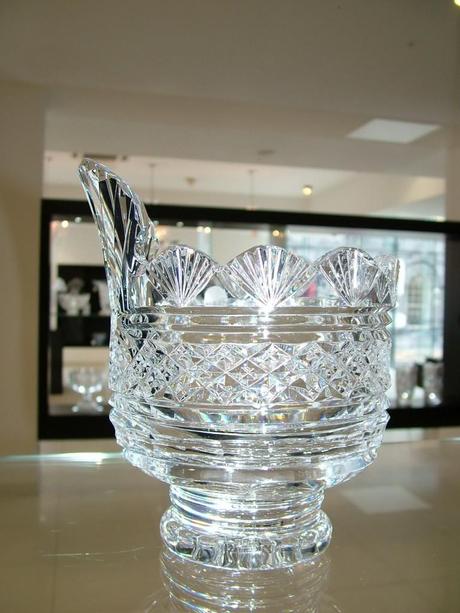
It is the deep cutting of the crystal that radiates such brilliance and sparkle,
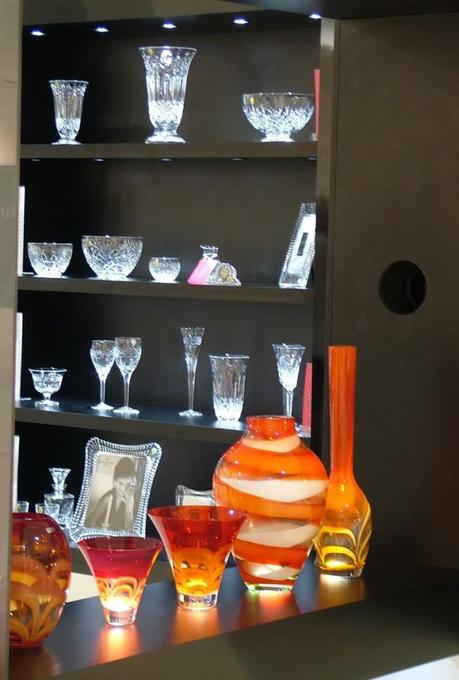
but my preference is still for the bold and vibrantly coloured crystal.
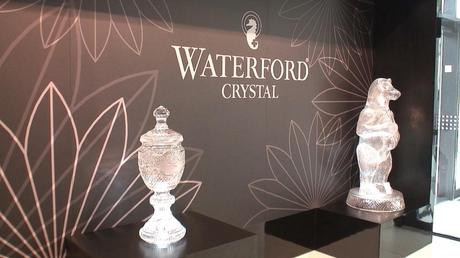
Bob and I enjoyed our educational tour of the House of Waterford Crystal, and it certainly gave us an appreciation for the world-famous glassware.
Checkout some of our other Ireland adventures
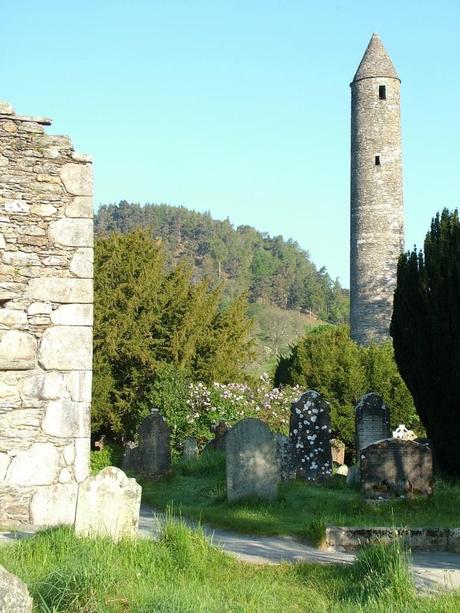
Glendalough, one of the most beautiful places in Ireland
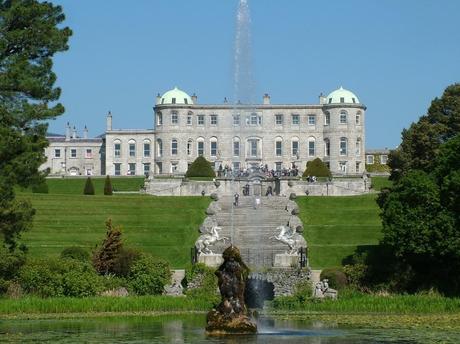
Powerscourt House and Gardens, A World Of Floral Glory – Ireland
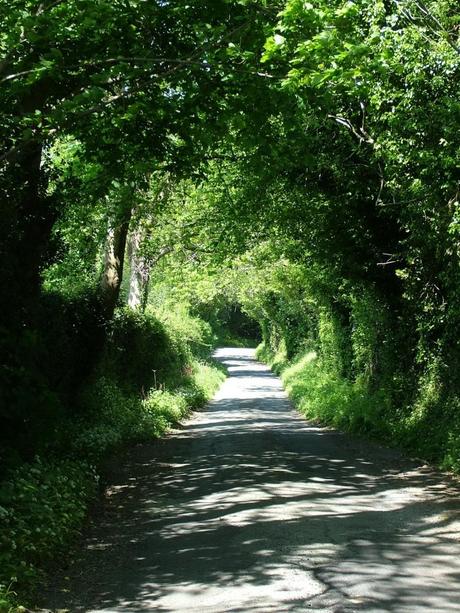
Driving the Intriguing Backroads of Wicklow County – Ireland
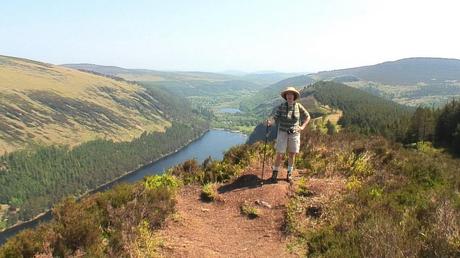
Hiking In Wicklow Mountains National Park – Ireland
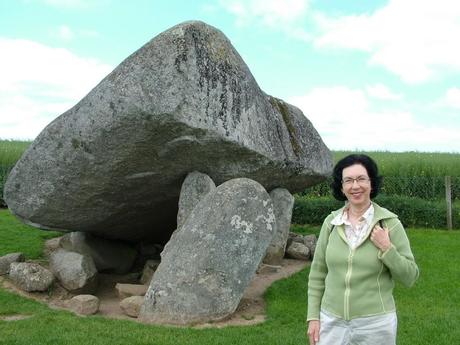
Our visit to the Neolithic Brownshill Portal Tomb in Ireland
Frame To Frame – Bob & Jean