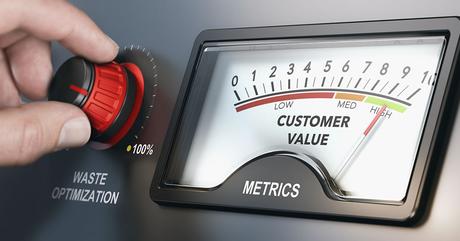
At Softstar Shoes, we pride ourselves on integrating sustainability into the fabric of our culture by responsibly sourcing materials, repurposing scrap, and reducing our carbon footprint. One important way we continuously work towards these goals is by incorporating lean manufacturing methodologies.
Lean principals are best described as the continual, passionate elimination of waste. We know being lean requires patience and nurturing. Being "lean" is what enables Softstar to make shoes in the USA and compete with brands that import their footwear from other countries.
Eliminating the 8 Forms of Waste
1. MOTION
How much walking, moving, and searching do we do when crafting shoes? Are tools in the right place? Does work flow easily from one Elf to another?
2. WAITING
How much time do we spend waiting for other team members? For equipment to be fixed? For material to arrive? How much time do shoes wait between steps?
3. TRANSPORTATION
How much distance does a shoe travel through our workshop from the beginning of its construction to the end? Can that distance be shorter?
7. EXTRA PROCESSING
Do we really need to inspect the shoes eight separate times? How do we identify where we can eliminate non-value-added (NVA) steps?
8. UNDERUTILIZED TALENT
Who has skills that would be better suited for different tasks? What innovative ideas do our team members have, and how do we encourage contributions?
Lean Manufacturing Team Training
After two years of social distancing, masks, and plastic sheeting, we realized COVID had put a serious dent in our teamwork and communication skills. We took this opportunity to tackle lean training head on.
In July and August 2022, Shingo prize winning author Gary Connor visited the Softstar workshop weekly. He helped reinvigorate our team's ability to literally and figuratively start working together again. He coached the Elves about teamwork, efficiency, and lean principles. Not only was Gary a fun and engaging teacher, but his lifetime of experience in lean manufacturing gave us valuable insights as to how we can improve our processes.
Developing lean and sustainable excellence requires a strong commitment to teamwork and open communication-a work culture of transparency where team members can take ownership. Yet becoming "lean" is a never-ending journey. It's a way of working, not a destination.
Gary's workshops focused on a variety of classic lean manufacturing topics such as 5S, flow, takt time, line balancing, and value stream mapping. Most importantly, he helped us develop our team communication skills. Continuous improvement necessitates everyone's engagement and creative problem-solving. Only then does it become possible to take action and implement changes.
Teamwork 101
- Observe! Ask "why" five times to get to the root of the issue. Communication is a nuanced skill we can always improve.
- Instead of reacting, pause and ask questions before responding.
- Understand and be aware of other people's communication styles, skills, and generational biases.
- Build an emotional bank account! Remember, it takes 17 positives to counteract 1 negative.
- A team mobilizes the intellectual resources of everyone in the group.
- Take action. Little steps build on each other and lead to big changes over time.
5S Principals
Gary taught the Elves about 5S, a five step methodology for creating a more organized and productive workspace.
After auditing three work spaces, the Elves made several observations and improvements. The sheep fluff bin was shined and cleaned up by adding a simple lid for protection. An outdated manual from 2018 was by removing it from a work space. And the Elves standardized a new procedure after realizing there's no reason to keep saving lace scraps that are too small to use for anything.
The fifth principal, "Sustain," is the hardest one. There's no point to the first four if you don't sustain the organized process you created! It's also important to understand there's no reason to feel bad about organizing. It may feel unproductive in the moment, but afterwards the improved efficiency speaks for itself.
How can made-in-USA manufacturing compete with importing?
Making shoes is labor-intensive endeavor. That's why most footwear in the USA (98%) is imported from global economies with lower labor costs. In the 1960s, the USA manufactured almost 100% of its footwear purchased domestically. But by the 1980s, the footwear industry had all but left US shores to capitalize on cheaper labor.
Softstar is able to stay competitive despite US labor costs being 3-10x higher than in other countries largely because our "lean" practices allow us to deliver optimal value to customers. We differentiate our products by not compromising on the quality of our materials or our ecological impact. All of this works in concert to deliver beautiful, high quality footwear with customizable colors to your doorstep.
Patient Journey: The Story of Bamboo
Lean manufacturing is a patient journey, not something that happens overnight. It takes years to cultivate and refine, yet can be devastated by neglect, short term thinking, or environmental ravages like COVID. Gary shared with us a parable about Bamboo to help internalize the time and dedication needed to cultivate a strong foundation:
"Like any plant, Bamboo requires care-water, good soil and sunshine. A farmer will plant a seed with care and hope. In year one, there is no visible signs of activity or development, and yet the farmer keeps watering and tending. In the second year, again, no growth above the soil. And after the third and fourth, still no signs of growth... yet the farmer persistently keeps making little contributions to sustain the seed. Suddenly, in the fifth year the little tree starts to grow, and how quickly it does! The bamboo tree grows nearly 80 feet in just 6 weeks!" - Parable of the Chinese Bamboo Tree as retold by Gary Conner
There you have it. Elves must be patient creatures! When it comes to lean culture, we know we need to keep honing our skills and make small incremental improvements in order to be successful well into the future. Lean culture helps Softstar build a strong foundation strong from the ground up. Apart from shoes, this is also our way of being.