Every once in a while, we get a builder contact us with a project that truly blows us away. We get to see so many custom built skateboards, that you may even say we've become desensitized to them (not really though, we love them all! Haha). Recently we were contacted by a new customer of ours who is using his 36” x 52” TAP bag to laminate specialty woods onto the bodies of his handmade guitars.
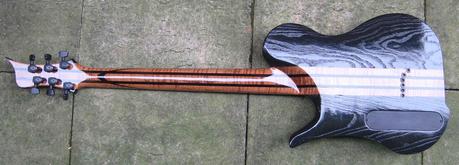
Dave Morgan wrote, "The Thin Air Press worked amazingly well. Very simple to use and I had zero problems with it. The bag lost no air even when left for 12 hours. Thanks for making such an affordable press that allows people like me to make a radius-top guitar!"
Well, with a quote like that we just had to ask him to go into more detail about his build! This is what he sent us:
"My current guitar design is based around the Fibonacci spiral (a.k.a. golden spiral). A key element of that design is for not only the shape to follow the proportions of the spiral, but the profile as well. This introduces an interesting challenge into the building process. In order to use various woods on the top of the guitar I need a mechanism to evenly bend it over a curved surface. That is where the Roarockit Thin Air Press (TAP) comes in.
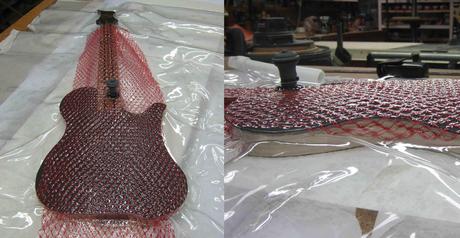
Other vacuum laminating systems are available on the market but I found them to cost $500 and up! When discussing the problem with my brother he mentioned that he read an article on the TAP in a woodworking magazine and recommended I take a look. I knew immediately that this would fulfill my need. The small size (26"x28") would fit a guitar body by itself, but the large size (36"x52") would fit the entire guitar, necessary for my neck-thru design.
Prior to building the guitar I watched the videos on the Roarockit site to get an idea of how difficult the process would be. There were two specific suggestions from those videos that I found very useful. First is to have one or two people help during the vacuum process to ensure the bag is flat and the pressure is applied evenly. The second was to use a glue with a longer set time (I used TiteBond II). Once I was ready, I put the guitar in the bag and spread the mesh evenly over the surface to allow for air flow.
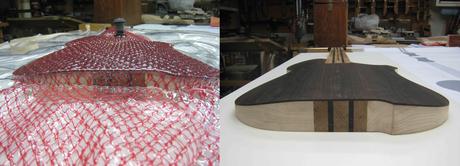
Before applying glue I used a shop vacuum to evacuate the air to see how quickly I could pump all the air out and check for adequate pressure to bend the wood. After a couple test runs I enlisted the help of a couple family members, applied the glue and placed the guitar and mesh in the bag. As recommended, I used the shop vacuum to get as much air out as possible first followed by using the included hand pump. This proved much easier than expected and within two minutes everything fully pressed. I checked the bag a couple times over the next few hours and found that the bag had not lost seal at all.
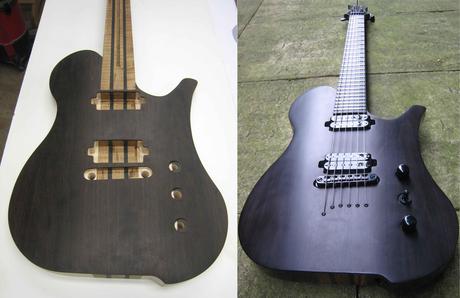
I left everything to set over night and in the morning the bag was still sealed as ever. I couldn't be happier with the results after removing the guitar from the bag. Roarockit have been great to work with and I highly recommend the TAP for wood working of all kinds."
Thank you so much for the kind words Dave! This guitar project really IS amazing.
While he is currently not taking orders for custom guitars, Dave left us his contact infromation for anyone interested in giving their feedback on the project.
You can contact Dave @ dave@phiguitars.com