Optimizing productivity by setting up systems and processes to promote higher yields is an efficient method to get ahead of the competition.
Enhance Quality-Control Policies
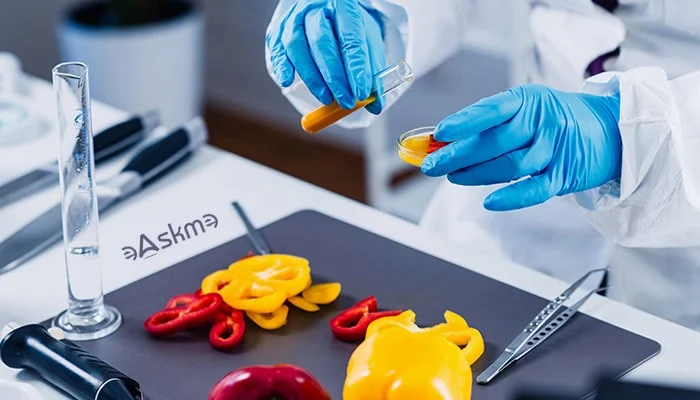
To ensure this, you must implement the necessary systems, tools, and policies that require a thorough vetting of all goods before leaving the plant.
One way to do this is to install metal detectors that can aid in detecting foreign objects in food items.
Create a Strategy for Preventative Maintenance
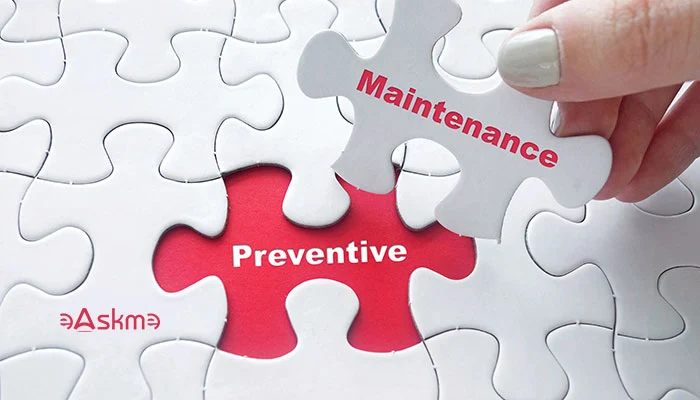
When it malfunctions or breaks down, it reduces output and lowers the quality of foods or goods.
To safeguard equipment from failure and prepare for inevitable downtime, the company should adopt a preventative maintenance policy.Indeed, with proper planning, you can better deal with unplanned downtime and get operations back up and running sooner.
Conduct Inventory Management
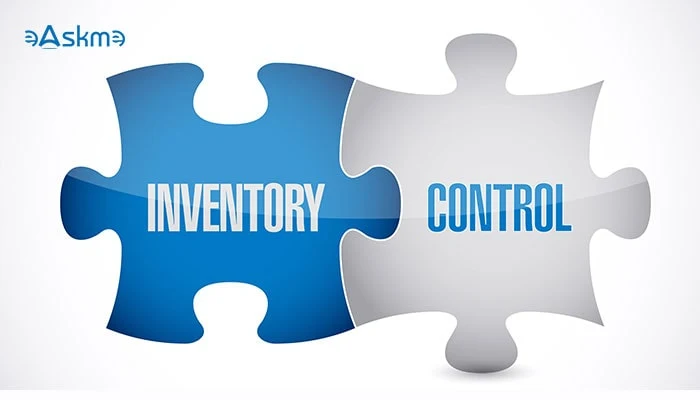
Establishing a robust inventory tracking system that can identify shortages and assist with acquiring fresh supplies is the best method to ensure this.
In this case, systems that can automatically monitor and acquire new commodities would be quite useful.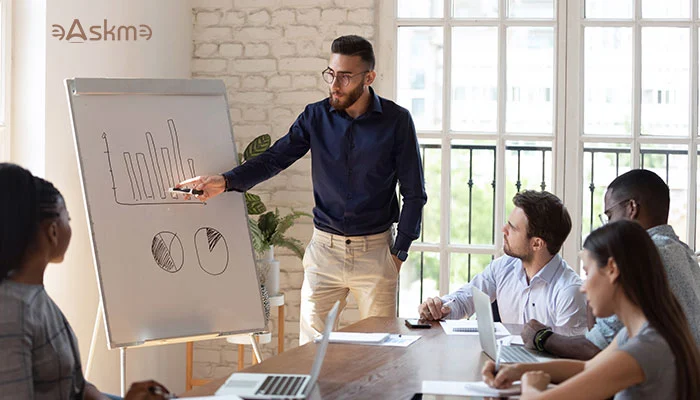
Put in Place Employee Training Programs
Ensure new employees and personnel are trained in a highly tailored environment using interactive and virtual training experiences that are very similar to the real thing. As a result, food safety training and good handling practices are critical for developing high-quality meals and products.
This not only improves product quality and minimizes contamination, but it's also a terrific method to increase productivity by implementing more precise and responsible handling procedures.
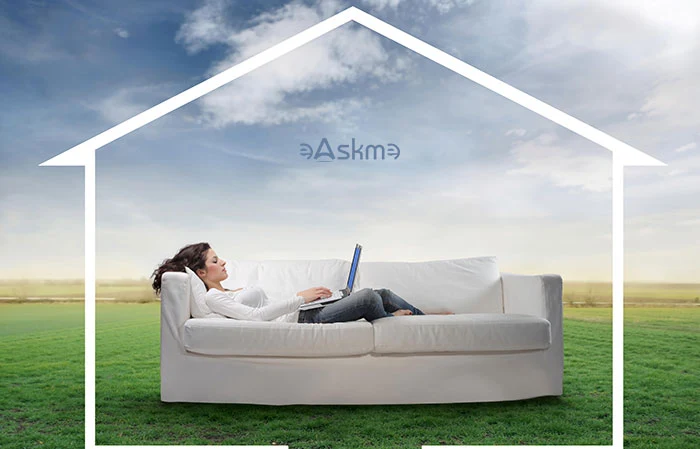
Maintain a Clean Work Environment
Make sure your employees are wearing the appropriate protective gear, such as safety goggles.
It's critical to keep factory settings clean and tidy and remove any physical barriers that may be in the way of workers.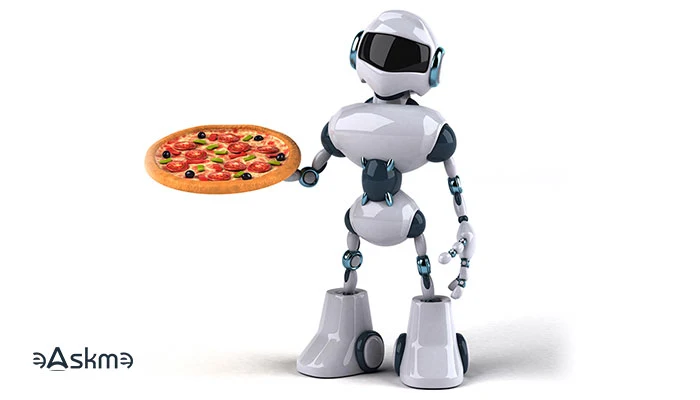
Clutter, on the other hand, can stifle productivity and restrict movement and operations.
On the other hand, automation can aid by replacing inefficient manual procedures with an efficient, self-contained manufacturing process.Use Automation or AI software
When you add in overseas competition, tariff uncertainties, and labor skill deficits, the FMCG industry is in a precarious position.
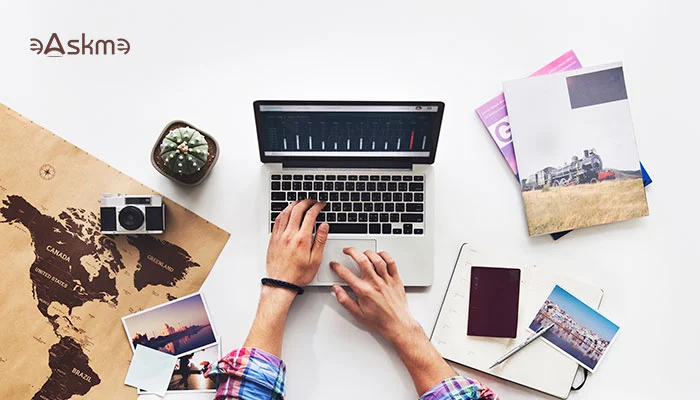
For instance, pick and place robots and powder filling machines can help you decrease production bottlenecks and delays caused by human error; it also helps you overcome worker shortages by allowing talented personnel to focus on value-added, strenuous activities rather than repetitive tasks.
Organize Your Work Station
Excessive mobility indicates a lack of structure and can waste a lot of time in the production process. Wherever possible, cut travel time and distance. Is there a way to decrease the distance, orient the product, or move the product more quickly and safely to the next phase in the process if it must be moved from one machine to another?
Is there any software that can help with scheduling?
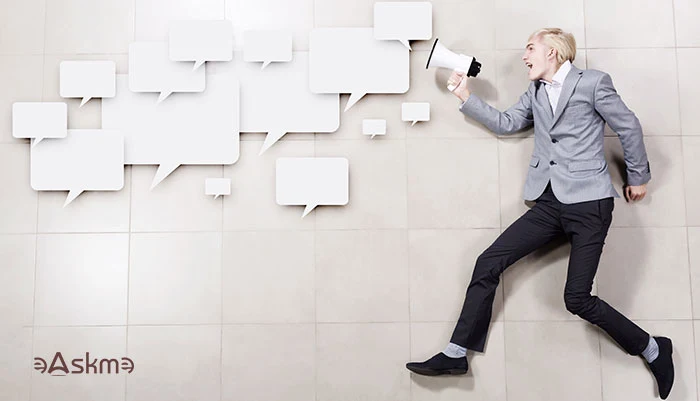
Consider using Kanban (just-in-time production) techniques to cut down on delays and boost efficiency.
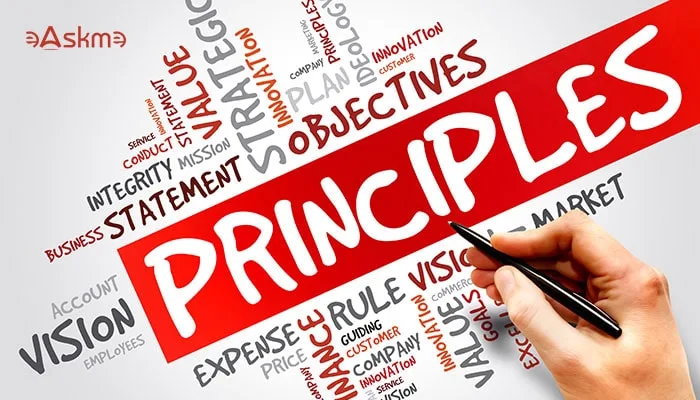
Encourage People to Communicate
The Toyota Production System, which incorporated many manufacturing practices from Henry Ford's assembly-line model, is where lean manufacturing got its start. Providing open channels for your employees to express their opinions will boost manufacturing productivity because you'll be informed of concerns you wouldn't otherwise be aware of.
- Seiri - classify tools, parts, and instructions according to their importance (needed or unneeded)
- Seiton - group tools and parts together, so they're easier to find and use.
- Seiso - keep the work area tidy.
- Seiketsu- create a daily timetable for Seiri, Seiton, and Seiso
- Shitsuke: Make the first four S's a strict order that must be followed at all times.
Apply Lean Manufacturing Principles
Having streamlined and effective processes is critical to your productivity, revenue, and client happiness when you own a manufacturing company.Less process waste, decreased lead time, less rework, lower inventories, enhanced process understanding, and improved knowledge are all business benefits of "lean."
In addition to these tips, it's important to put shipping logistics capable of managing your supply needs in place.To summarize lean manufacturing concepts, refer to the Lean Manufacturing 5 S's:
Conclusion
You now have a solid platform to begin improving your manufacturing productivity, thanks to the advice and hints provided here.
Partner with a reliable and affordable shipping company that offers Amazon shipping from China.
By delegating your preparation and logistics, you free up time to focus on your business.
Taking advantage of China's cheap labor expenses will result in lower preparation costs than in your market.
If you find this article interesting, don't forget to share it with your friends and family.
Don't forget to like us FB and Follow on Twitter to stay tuned with us.
You May Also Like These;