For years, China has been the go-to destination for offshore industrial manufacturing. Abundant and low-cost labor and manufacturing costs, cheap oil, and reliable trade routes convinced many manufacturers to relocate industrial operations overseas.
Then, market conditions changed. Wages and real estate costs rose. U.S. seaports faced shutdowns and logjams, forcing backlogs across the supply chain. Manufacturers found themselves looking for a manufacturing destination closer to home. For those in the automotive, industrial and electronics sectors, Mexico answers the call.
In its latest Executive Viewpoint, “Mexico: The New Industrial ‘Nearshore’ Destination – Manufacturing Sector Finds Cross-Border Home,” executives from Ryder explore how economic and logistics changes encouraged manufacturers to look south – instead of east – for their manufacturing solutions.
The paper reveals that tidings are rising for America’s third-largest U.S trade partner, one with thousands of cross-border transits and trade that tops a billion dollars every day. Already, studies show that some 49% of manufacturers would consider reshoring at least part of their operations to Mexico by 2020.
Why nearshore to Mexico? Among the benefits are:
- Proximity. A shipper can move freight from Mexico to the U.S. by ocean in 48 hours; by truck, it can take 24 hours or less, compared to weeks from Asia via ocean container. This means faster customer service cycle times, especially for custom products. Working in the same or proximate time zones, companies can dispatch personnel or product to factories or facilities often a few hours away by plane or truck.
- Growing truck and rail traffic. More than 1.37 million trucks crossed the U.S.-Mexico border in the first quarter 2015, up 2.9% from the same period the year before. And the value of goods rose by 9% over the same time last year.
- Lower labor and production costs and the strengthening dollar. China’s higher labor costs compared to those in Mexico, along with productivity gains and a depreciation of the peso against the dollar, keep wage growth in check. Meanwhile, falling U.S. natural-gas prices for industrial users has resulted in energy-cost advantages.
Nearshoring to Mexico also has its challenges. From economic uncertainties surrounding the currency exchange, to the importance of training a young workforce in key labor skills, to the need for more Mexican investment in roads, telecommunications and other infrastructure, any shift to Mexico requires on-the-ground analysis before a move is made.
Border crossings historically have been fraught with delays and stiff customs requirements, and crime and security remain concerns for shippers and manufacturers. It’s critical to partner with 3PLs that participate in the Customs-Trade Partnership Against Terrorism (C-TPAT) and Mexico’s Nuevo Esquema de Empresas Certificadas (NEEC), initiatives that seek to reduce risks by promoting global supply chain security.
In fact, organizations unfamiliar with nearshoring of manufacturing or logistics operations, or exploring how Mexico may meet their needs, should consult with a 3PL whose extensive experience in Mexico can help lay the groundwork for a successful nearshoring opportunity.
As China fades as the industrial manufacturing market’s outsourcing destination of choice, Mexico seems primed to meet U.S. manufacturers’ needs. With an abundant labor pool, lower wages and energy costs, and improving truck and rail transport, Mexico has emerged as the nearshore alternative to outsourced manufacturing.
To learn more, download “Mexico: The New Industrial ‘Nearshore’ Destination – Manufacturing Sector Finds Cross-Border Home,” the latest Executive Viewpoint from Ryder System Inc.
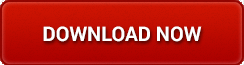