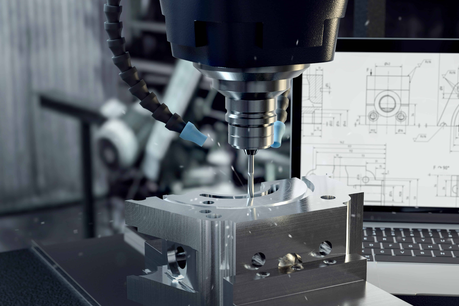
Rapid prototyping involves creating a quick physical product model to test its design, functionality, and fit. Engineers and designers use this method to speed up the development cycle and bring ideas to life faster. By producing prototypes quickly, teams can make adjustments early, which reduces production costs and time.
Various manufacturing techniques are used for rapid prototyping, each suited to different needs and materials. This article explores these techniques and their roles in the rapid prototyping process.
What Is Rapid Prototyping?
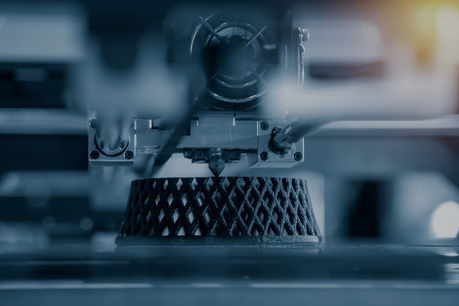
Rapid prototyping is a process used in product development to create quick, tangible models of designs. These models help engineers, designers, and stakeholders visualize, test, and refine products before they go into full production. By producing prototypes rapidly, teams can identify potential issues, test functionality, and adjust early in the development cycle.
The core purpose of rapid prototyping is to accelerate the design process, allowing multiple iterations in a short time frame. This approach saves time and cost by catching design flaws and functional issues early, which would otherwise be more expensive to fix in later stages. Techniques such as 3D printing, CNC machining, and casting are commonly used, each offering unique advantages depending on the project's specific needs.
Rapid prototyping isn't limited to a single field; it's applied across industries, from consumer electronics to aerospace. By bringing designs to life quickly, companies can innovate faster, reduce development risks, and ultimately deliver higher-quality products to market more efficiently.
What Kinds of Manufacturing Techniques Can Be Used for Rapid Prototyping?
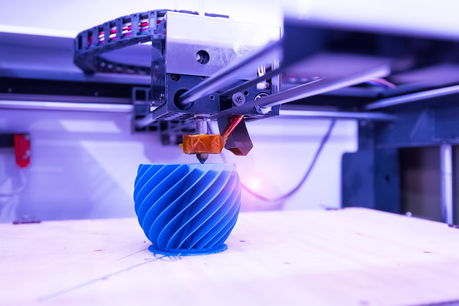
Here are the different kinds of manufacturing techniques that can be used for rapid prototyping:
CNC Machining
Computer Numerical Control (CNC) machining is a subtractive manufacturing technique that includes cutting and shaping a solid block of material with computer-controlled machinery. CNC machines can create CNC prototypes with great precision and accuracy, making them ideal for functional testing and validation. CNC machining is widely used for prototyping metal and plastic components and supports various materials and surface treatments.
Vacuum Casting
Vacuum casting, also known as silicone casting or polyurethane casting, is a technique for producing small batches of prototypes or low-volume manufacturing components. It entails designing a master pattern and using it to create a silicone mould. The mould is vacuumed, and liquid polyurethane resin is injected to recreate the master design. Vacuum casting is ideal for creating prototypes in various materials, colours, and surface treatments.
3D Printing/Additive Manufacturing
3D printing, commonly known as additive manufacturing, is a popular rapid prototyping process. It entails building physical objects layer by layer based on a computer model. There are several types of 3D printing methods available, including fused deposition modelling (FDM), stereolithography (SLA), selective laser sintering (SLS), and digital light processing. 3D printing lets designers iterate and validate their designs quickly by producing complex and customised prototypes from various materials.
Rapid Injection Molding
Rapid injection moulding is a process for producing small to medium quantities of prototypes or low-volume manufacturing parts. The process entails making a mould from a master pattern and injecting molten material (usually plastic) into the mould cavity. Rapid injection moulding has faster turnaround times than standard injection moulding methods, making it excellent for iterative prototyping and small-batch production.
Rapid Electronics Prototyping
Rapid electronics prototyping uses off-the-shelf electronic components, development boards, and breadboards to create and test electronic circuits and systems quickly. This method allows designers to assess electrical device functionality and integrate hardware and software components. Rapid electronics prototyping is widely employed in IoT projects because it enables quick iterations and changes.
Sheet Metal Prototyping
Sheet metal prototyping creates prototype sheet metal components such as enclosures, brackets, and panels. Thin metal sheets are cut, bent, and assembled to get the desired shape. Laser cutting, waterjet cutting, bending, and welding are techniques used to create sheet metal prototypes. This method is commonly used for functional testing and determining component fit.
Key Considerations When Choosing Rapid Prototyping Method
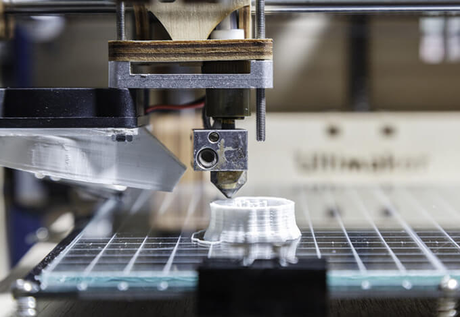
Selecting the proper prototyping technique requires understanding the project's specific needs. Here are a few crucial factors to consider:
Material Compatibility
Material compatibility is essential because each CNC rapid prototyping method supports different materials. For example, Fused Deposition Modeling (FDM) 3D printing works well with thermoplastics like ABS and PLA, which are suitable for lightweight, less rigid prototypes. On the other hand, techniques like CNC machining can work with a wide variety of materials, including metals and composites, making them ideal for durable parts. Understanding the material properties needed, such as flexibility, durability, or temperature resistance, helps select a compatible method that delivers the best results.
Accuracy and Detail
The level of detail and accuracy required affects the choice of method. Techniques like Stereolithography (SLA) or Selective Laser Sintering (SLS) produce high-resolution parts with fine details, which is ideal for complex designs or parts requiring precision. CNC machining may be preferred for applications that need tight tolerances or intricate geometries because it can deliver parts with very low dimensional variation. On the other hand, FDM 3D printing may not offer the same level of detail but can be ideal for rapid, low-cost prototyping of simpler designs.
Production Speed
The timeline for producing prototypes is often critical, particularly in iterative design cycles. Additive manufacturing methods like SLA and FDM can produce parts within hours, which is ideal for rapid design changes and testing. However, if a prototype requires more durable materials or larger, intricate parts, processes like CNC machining or metal casting may take longer but offer better material strength. Balancing the need for speed with the required durability and complexity helps ensure the project remains on schedule without sacrificing quality.
Cost Constraints
Budga significantnificantr role in choosing a rapid prototyping technique. 3D printing, particularly FDM, is often more affordable for simple prototypes, making it a preferred choice for initial concept models. In contrast, CNC machining or SLS can be more costly due to the complexity of the setup and material expenses but may be justified for parts that require specific mechanical properties or tight tolerances. By assessing both the project's budget and prototyping goals, teams can select a method that delivers value without exceeding financial limits.
End-Use Requirements
The intended use of the prototype will influence the choice of method. A low-cost option like FDM printing can suffice if the prototype is only for visual purposes, such as a concept model for design review. However, methods like CNC machining or metal sintering are often necessary if the prototype requires full functionality, durability, and strength. Functional prototypes can undergo testing for fit, form, and mechanical properties, making them suitable for advanced stages in product development.
Conclusion
Rapid prototyping has become essential for modern product development, enabling teams to test designs and make informed improvements early in the process. By understanding and selecting the proper manufacturing techniques, companies can develop prototypes that meet specific material, accuracy, speed, cost, and functional requirements. This approach saves time and resources and enhances product quality, helping bring ideas to market faster and with greater confidence. It offers even more possibilities for innovation and precision across various industries.