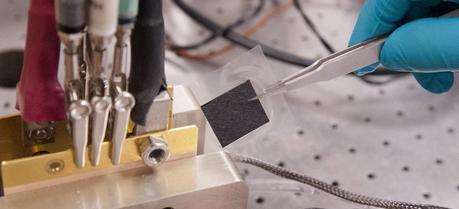
A new relatively inexpensive polymer membrane can decrease the cost of alkaline fuel cells and batteries by allowing the replacement of pricey platinum catalysts while keeping the important aspects of performance intact, according to Penn State researchers.
“We have tried to break this paradigm of tradeoffs in materials (by improving) both the stability and the conductivity of this membrane at the same time, and that is what we were able to do with this unique polymeric materials design,” said Michael Hickner, associate professor of materials science and engineering.
In solid-state alkaline fuel cells, anion exchange membranes conduct negative charges between the device’s cathode and anode — the negative and positive connections of the cell — to create useable electric power. Most fuel cells currently use membranes that require platinum-based catalysts that are effective but expensive.
Hickner’s new polymer is a unique anion exchange membrane — a new type of fuel cell and battery membrane — that allows the use of much more cost-efficient non-precious metal catalysts and does not compromise either durability or efficiency like previous anion exchange membranes.
“What we’re really doing here is providing alternatives, possible choices, new technology so that people who want to commercialize fuel cells can now choose between the old paradigm and new possibilities with anion exchange membranes,” Hickner said.
Creating this alternative took some intuition and good fortune. In work spearheaded by Nanwen Li, a postdoctoral researcher in materials science and engineering, Hickner’s team created several variations of the membrane, each with slightly different chemical compositions. They then ran each variation under simulated conditions to predict which would be optimal in an actual fuel cell.
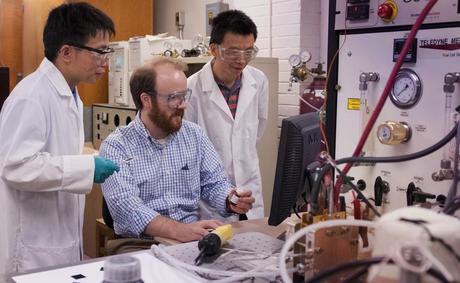
Michael Hickner, seated, along with research associates Yongjun Leng, left, and Nanwen Li review the data received from a specific polymer membrane that has been inserted into the fuel cell test stand. (Credit: Patrick Mansell / Pennsylvania State University)
Based on these initial tests, the group predicted that the membranes with long 16-carbon structures in their chemical makeup would provide the best efficiency and durability, as measured respectively by conductivity and long-term stability.
Chao-Yang Wang, William E. Diefenderfer Chair of Mechanical Engineering, and his team then tested each possibility in an operating fuel cell device. Yongjun Leng, a research associate in mechanical and nuclear engineering, measured the fuel cell’s output and lifetime for each material variation.
Despite predictions, the membranes containing shorter 6-carbon structures proved to be much more durable and efficient after 60 hours of continuous operation.
“We were somewhat surprised…that what we thought was the best material in our lab testing wasn’t necessarily the best material in the cell when it was evaluated over time,” said Hickner, who added that researchers are still trying to understand why the 6-carbon variation has better long-term durability than the 16-carbon sample in the fuel cell by studying the operating conditions of the cell in detail.
Because the successful membrane was so much more effective than the initial lab studies predicted, researchers are now interested in accounting for the interactions that the membranes experienced while inside the cell.
“We have the fuel cell output — so we have the fuel cell efficiency, the fuel cell life time — but we don’t have the molecular scale information in the fuel cell,” Hickner said. “That’s the next step, trying to figure out how these polymers are working in the fuel cell on a detailed level.
Li N, Leng Y, Hickner MA, & Wang CY (2013). Highly Stable, Anion Conductive, Comb-Shaped Copolymers for Alkaline Fuel Cells. Journal of the American Chemical Society PMID: 23721192