The aluminium alloy wheels tend to crack once they are hit hard, and the hardness depends on various factors like the brittleness of the alloy, the wheel's design, and the aspect ratio of the tyre.
Normally, the causes of the cracks are the deep potholes and the raised manhole cover. Cracks are too dangerous and even let the tyre loose out its air. The air leaves without any warning and at a great speed.
Small cracks in the wheels might be covered and sealed, using the tyre's bead to stop the tyre from leaking. But the cracks will grow and widen, thus impact the originally caused crack. If the cracks go to turn on one side or it gets split to a "Y" shape then in all possibilities, the entire chunk of the wheel could catastrophically be lost.
A few issues to consider to make a decision for welding cracked wheels.
* The crack's location: The marginally safe cracks for welding are the ones at the back or on the wheels' inboard side. If a crack is on the wheel's front face, then the cracks contain the structural integrity of the wheel similar to the cracks on the spokes. If the crack is inside the barrel, then welding is not possible.
* The crack's direction: If the crack is on the wheels' backside, it will cross the bead area and the flange at right angles to the wheel spins. These cracks can be welded as these are opened up for accepting the weld. The cracks going parallel to the direction of the spin are not welded since it causes the wheels to widen at the weld area, preventing the wheels from running straight again.
* The welder's skills: Aluminium alloy are welded through the process known as Tungsten Inert Gas welding or TIG welding. Many aluminium wheels had been Metal Inert Gas welding which had been a disaster. The bead becomes much thinner and weaker, and the process makes the surrounding alloy burn. Thus, the entire area around tyre becomes weak around the weld. Hence, the wheels are welded only when the experienced welder carries out TIG welding and deals specifically with each wheel.
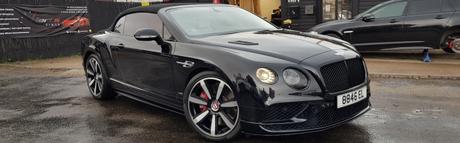
Before the is done, the wheels are straightened. The impacts cracking the wheels will be equally bent, and the welders substantially straighten the wheels. Often, electrical current is beneficial for welding to slightly warp the wheels, which requires there is some requirement of minimal truing later, that is done easily when the wheels are straight before the welding.
Once the wheels are welded, the welders deal with a large bead of solder, and the bead must be completely smoothened where the tyre is contacting the wheel, or the tyre will make imperfect contact and leak. After grinding down the bead and smoothening it out on both sides, the welders even smoothen the entire area using a computer numeric control lathe, while preparing to repaint or re-machine the wheel. Often the welders smoothen the barrel's outside and the beads are left on the inside for making sure the welds are strong.
Overall, when the wheels are to be welded, then the professionals are must to hire. Through welding, the wheels are saved from the disaster of becoming useless. Rather, the welders know the right place to start from, and they are sure to perform the process rightly.