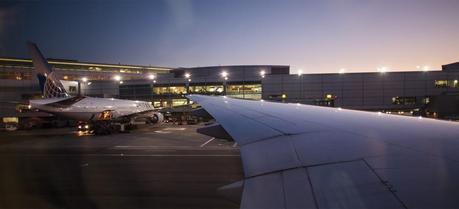
The EU project SARISTU (Smart Intelligent Aircraft Structures) aims to reduce kerosene consumption by 6%, and integrating flexible landing devices into aircraft wings is one step towards that target.
While birds are able to position their feathers to suit the airflow, aircraft wing components have so far only been rigid. As the name suggests, landing flaps at the trailing edge of the wing are extended for landing. This flap, too, is rigid, its movement being limited to rotation around an axis. This is set to change in the SARISTU project.

Shape-changing aircraft wings to cut kerosene consumption by 6%. Simulation of a flex module. (Credit: Fraunhofer IFAM)
“Landing flaps should one day be able to adjust to the air flow and so enhance the aerodynamics of the aircraft,” explains Martin Schüller, researcher at the Fraunhofer Institute for Electronic Nano Systems ENAS in Chemnitz, Germany. A mechanism that alters the landing flap’s shape to dynamically accommodate the airflow has already been developed by the consortium partners. Algorithms to control the required shape modifications in flight were programmed by ENAS, in collaboration with colleagues from the Italian Aerospace Research Center (CIRA) and the University of Naples.
The mechanism that allows the landing flap to change shape can only function if the skin of the landing flap can be stretched as it moves, a problem tackled by researchers from the Fraunhofer Institute for Manufacturing Technology and Advanced Materials IFAM in Bremen. “We’ve come up with a silicon skin with alternate rigid and soft zones,” reveals Andreas Lühring from Fraunhofer IFAM. “There are five hard and three soft zones, enclosed within a silicon skin cover extending over the top.”
The mechanism sits underneath the soft zones, the areas that are most distended. While the novel design is noteworthy, it is the material itself that stands out, since the flexible parts are made of elastomeric foam that retain their elasticity even at temperatures ranging from -55 to 80 °C (-67 to 176 °F).
Four 90-centimeter-long prototypes—two of which feature skin segments—are already undergoing testing.
A single improvement won’t be enough to cut kerosene consumption by 6% Since a variety of measures are needed, scientists from Fraunhofer IFAM are participating in a second subproject focusing on the wingtip. Here the SARISTU consortium has developed a tab that forms part of the wing tip and changes shape during flight to keep air resistance as low as possible. Any gap between the flap and the fixed aircraft wing would cancel out any positive effect. “This led us to develop an elastic connecting element, and this work already covers everything from the chemical makeup to the process technology and manufacture of the component,” says Lühring. Like the landing tab, this component retains its elasticity at temperatures ranging from -55 to 80 °C, and it easily copes with the high wind speeds involved.