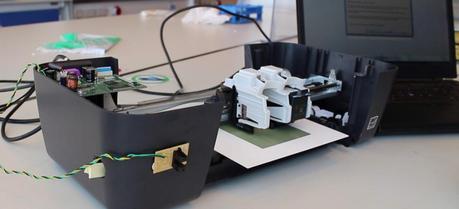
Researchers at DTU Energy Conversion has transformed an ordinary HP 1000 ink jet printer into a printer able to print efficient energy conversion devices such as solid oxide fuel cells (SOFC).
SOFCs have attracted increasing attention over the last two decades due to high energy conversion efficiency, efficiency, fuel flexibility and low environmental impact, but the technology still has some challenges related to cost and durability before gaining entry at commercial markets. Some of those challenges might be solved using inkjet printers, both as a development tool to reduce the design-prototype-test cycle time for the development of new cell types, and as a manufacturing tool where entire SOFC stacks are printed using significantly smaller amounts of materials than traditional manufacturing processes.
SEE ALSO: Solar-Induced Fuel Cell Converts Biomass to Electricity
Research on 3D-printing has been going on for some time, but recently a research team at DTU Energy Conversion, consisting of Christophe Gadea, Vincenzo Esposito, Johan Hjelm, Karsten Agersted, Qiang Hu, Søren Højgaard Jensen and Severine Ramousse, succeeded in modifying an ordinary HP 1000 ink jet printer, costing approx. 400 DKK (≈$73), enabling it to print inexpensive fuel cells showing superior performances compared to fuel cells fabricated by traditional tape casting.
“We have developed a cheap and innovative technology that allows the printing of ceramic thin films (≈1µm), using an inkjet printer. A continuous and dense 1.2 micrometer yttria stabilized zirconia layer has been fabricated with this process and it improved the fuel cell performance. This process is flexible enough to be applicable for numerous materials for other applications involving thin layers as well,” explains Christophe Gadea, development engineer at DTU Energy Conversion.
Several technologies have been studied for the elaboration of thin-film electrolytes for SOFCs, including chemical vapor deposition (CVD), pulsed laser deposition (PLD), spray coating, screen printing, electrophoretic deposition (EPD), tape casting and dip coating. However, CVD and PLD are expensive and difficult to scale up. Although spray coating, tape casting and screen printing processes are inexpensive and can be easily scaled up, deposition of thin films using one of these processes with thicknesses less than 10 µm is a technical challenge.
Inkjet printing has a tendency to miss a pixel once in a while, resulting in leaks in the electrolyte and a decreased performance, but this problem was solved by printing several layers on top of each other, greatly improving the cell efficiency and still keeping the overall thickness below 10 µm.
“In the nearby future, activities will be focused on improving inks, printing more complex patterns and optimizing the final process to enhance the printed layers characteristics such as substrate covering and surface profile”, explains Christophe Gadea.