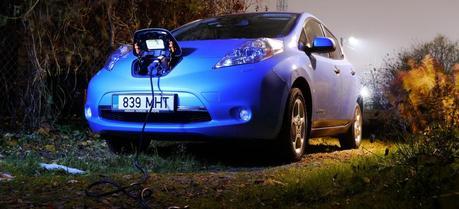
Chemists at the NIM Cluster at the Ludwig Maximilian University of Munich and at the University of Waterloo, Canada, have created a novel type of porous nanofiber that can help make lithium-sulfur batteries more efficient.
Lithium-sulfur batteries’ cathodes are made mainly of sulfur, a cheap waste product of petroleum processing. Sulfur cathodes offer high energy density, but they have two major weaknesses. Sulfur easily combines with lithium to form compounds that crystallize and gum up the battery’s insides, and it tends to crack under the stress of repeated cycling. As a result, a typical lithium-sulfur battery becomes useless within a few dozen cycles—far too few for a laptop or car battery that may get cycled once a day for years.SEE ALSO: High-Capacity Molten Air Battery Developed
The chemists Professor Thomas Bein (LMU), Coordinator of the Energy Conversion Division of the Nanosystems Initiative Munich, Professor Linda Nazar (University of Waterloo, Waterloo Institute of Nanotechology) and their colleagues have now succeeded in producing a novel type of porous nanofiber with a highly ordered structure that gives it an extraordinarily high surface-to-volume ratio. Thus, a sample of the new material the size of a sugar cube presents a surface area equivalent to that of more than seven tennis courts.
“The high surface-to-volume ratio, and high pore volume is important because it allows sulfur to bind to the electrode in a finely divided manner, with relatively high loading. Together with its easy accessibility, this enhances the efficiency of the electrochemical processes that occur in the course of charge-discharge cycles. And the rates of the key reactions at the sulfur electrode-electrolyte interface, which involve both electrons and ions, are highly dependent on the total surface area available,” as Benjamin Mandlmeier, a postdoc in Bein’s Institute and a first co-author on the new study, explains.
A novel recipe and a cleverly designed mode of synthesis are the key factors that determine the properties of the new materials. To synthesize the carbon fibers, the chemists first prepare a porous, tubular silica template, starting from commercially available, but non-porous fibers. This template is then filled with a special mixture of carbon, silicon dioxide and surfactants, which is then heated at 900°C. Finally the template and the SiO2 are removed by an etching process. During the procedure, the carbon nanotubes—and thus the pore size—shrink to a lesser extent than they would in the absence of the confining template, and the fibers themselves are correspondingly more stable.
“Nanostructured materials have great potential for the efficient conversion and storage of electrical energy,” says Thomas Bein. “We in the NIM Cluster will continue to collaborate closely with our colleagues in the Bavarian SolTech Network in order to explore and exploit the properties of such structures and their practical applications.”
He, G., Mandlmeier, B., Schuster, J., Nazar, L., & Bein, T. (2014). Bimodal Mesoporous Carbon Nanofibers with High Porosity: Freestanding and Embedded in Membranes for Lithium–Sulfur Batteries Chemistry of Materials DOI: 10.1021/cm403740r