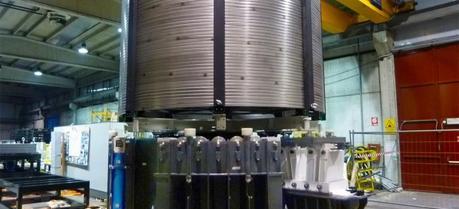
To initiate and maintain plasma current, the international ITER fusion reactor requires a giant solenoid—which will be the largest pulsed electromagnet ever built. The 1,000 metric ton solenoid located in the center of the ITER tokamak will have 5.5 gigajoules of stored energy and be about 18 meters, or 60 feet, tall.
The Oak Ridge National Laboratory (ORNL) US ITER team leading the central solenoid development and fabrication has developed a firm basis for the design and achieved a number of key milestones in the last six months, including a final pulsed electromagnet design review in December 2013. Authorization to proceed to manufacturing is expected in May 2014 from the project’s coordinating body, the ITER Organization.
“The central solenoid development has followed a unique process,” said David Everitt, the CS system manager. “We brought the fabricator, General Atomics in San Diego, on board early to help with manufacturing review and development. As the CS design progressed, the fabricator has been taking our design, prototyping it and providing feedback.”

The 1,000 metric ton solenoid located in the center of the ITER tokamak will have 5.5 gigajoules of stored energy and be about 18 meters, or 60 feet, tall. (Credit: ITER)
That approach has helped US ITER resolve a number of engineering challenges. Not only is the central pulsed electromagnet unusually large and powerful, but it also is tightly integrated into the ITER magnet system. ITER uses a magnetic confinement approach to contain 100 million degrees Celsius plasmas within carefully defined magnetic fields. In some locations, there will be only 10 mm of space—the width of a thick pencil—between the massive central solenoid and a 13 meter, or 45 foot, tall “D”-shaped toroidal field magnet.
Wayne Reiersen, the US ITER magnet systems team leader, noted, “The actions proposed in the final design review report are thoughtful and provide us with excellent feedback on the central solenoid design and path forward. We will really benefit from this review.”
Overall, the final design review confirmed that the central solenoid design is well supported by analysis and by research and development.
The pulsed electromagnet will be composed of six stacked modules, each made of conductor wound into pancake-like layers. An individual module weighs more than 110 metric tons. The manufacturing process for the modules of the central solenoid will take 16—24 months per module. Each module, plus a spare, must be fabricated and tested at full current, 45 kA, and 4 degrees Kelvin, or about -450 degrees F, to ensure that the magnets are ready to perform in the superconducting environment of the ITER machine.
The modules will be fabricated with a just-in-time process. As each shipment of conductor is received, it will immediately enter the winding station to be formed into pancakes. The module fabrication process culminates approximately two years later when the module passes final testing and is shipped to France. Everitt added, “Building the central solenoid is all about timing. At any one time, we can have four or five modules moving through the production process.”
A central solenoid mock-up module, which will verify the production process, is planned for completion in summer 2015, with sample conductor winding activities beginning in summer 2014.
Twelve tooling stations for the central solenoid modules will be installed in a General Atomics fabrication building in Poway, Calif. Most of the workstations have progressed beyond final design and are in the fabrication stage. Some of the more complex stations include conductor winding, turn insulation, vacuum pressure impregnation of insulation material and final testing.
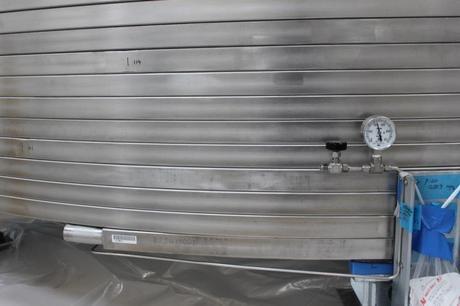
Sample conductor, which is not superconducting, has been delivered to General Atomics in preparation for fabrication of the mock-up module. (Credit: US ITER)
The winding station, which requires precise radius and turn transitions, is now in fabrication near Torino, Italy, by Tauring, under contract to General Atomics. Tauring has developed a control system based on the total length of the conductor to accommodate ITER requirements.
“Turn insulation is a complex manufacturing process,” Everitt explained. “Multiple layers of insulating materials are required and must be wrapped around the conductor after the winding and heat treatment processes are completed. Because there is a strain limit on the conductor after heat treatment, the conductor must be carefully un-sprung—not unlike a Slinky—to apply the insulation and then reassembled in the correct coil configuration.”
Reierson added, “There is great confidence in and a firm basis for the design. And there is also confidence that assembly tooling production is possible on time.” Assembly tooling refers to any specialized tools needed to pick up, move and install the components of the central solenoid.
Mike Cole, a US ITER engineer leading the tooling effort, explained assembly tooling actually lags the modules and structures in the design and fabrication schedule. But the tooling needs to be ready at the right time for the assembly of the central solenoid.
“Anything related to the central solenoid has to be addressed: How do you pick it up and install it? Humans can be expected to lift only items of around 25 pounds or less,” Cole said. “We also need to make sure that we meet French industry standards.”
The most significant challenges for tooling are the assembly platform and the module lifting structure. Both items need to be delivered early to the ITER site.
US participation in ITER is sponsored by the Department of Energy Office of Science and managed by Oak Ridge National Laboratory in Tennessee, with contributions by partner labs Princeton Plasma Physics Laboratory and Savannah River National Laboratory.