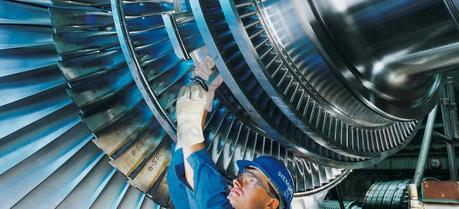
About 90% of all electricity is generated using steam as the working fluid, nearly all by steam turbines. In electric generation, steam is typically condensed at the end of its expansion cycle, and returned to the boiler for re-use. A technology that improves steam condenser efficiency could have a large impact on global electricity generation. Now a team of scientists from MIT has found a way to do this.
A surface steam condenser is a commonly used term for a water-cooled shell and tube heat exchanger installed on the exhaust steam from a steam turbine in thermal power stations. These condensers are heat exchangers which convert steam from its gaseous to its liquid state at a pressure below atmospheric pressure. Surface condensers are also used in applications and industries other than the condensing of steam turbine exhaust in power plants.
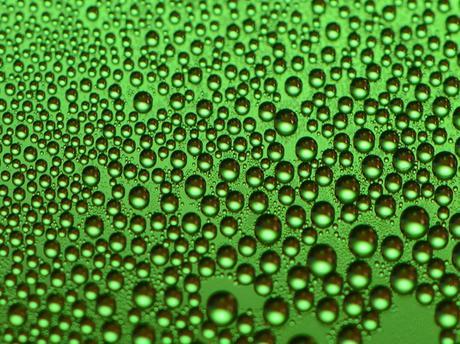
On typical hydrophobic coatings, droplets forming from high-temperature steam soon spread out to coat the surface, quickly degrading their performance. The new coating, seen here, maintains its ability to foster droplet formation over long periods. (Credit: See citation at the end of this article)
In thermal power plants, the primary purpose of a steam condenser is to condense the exhaust steam from a steam turbine to obtain maximum efficiency, and also to convert the turbine exhaust steam into pure water (referred to as steam condensate) so that it may be reused in the steam generator or boiler as boiler feed water.
It has been known for years that hydrophobic steam-condenser surfaces (ones that repel water) could improve the efficiency of condensation by causing the water to quickly form droplets. But most hydrophobic materials have limited durability, especially in steamy industrial settings. The new approach to coating condenser surfaces should overcome that problem, the MIT researchers say.
The findings are reported in the journal Advanced Materials by MIT professors Karen Gleason and Kripa Varanasi, graduate student Adam Paxson and postdoc Jose Yagüe.
The covalent-bonding process the team developed is significantly more stable than previous coatings, he says, even under harsh conditions.
Tests of metal surfaces coated using the team’s process show “a stark difference,” Paxson says. In the tests, the material stood up well even when exposed to steam at 100 degrees Celsius in an accelerated endurance test. Typically, the steam in power-plant condensers would only be about 40 degrees Celsius, Varanasi says. According to degradation models, the material might be durable for much longer than these initial tests: “We’re thinking tens of years,” Gleason says.
The new coating can easily be applied to conventional condenser materials—typically titanium, steel, copper or aluminum—in existing facilities, using a process called initiated chemical vapor deposition (iCVD).
Another advantage of the new coating is that it can be extremely thin—just one-thousandth of the thickness of conventional hydrophobic coatings. That means that while steam condenser efficiency is improved, the other properties of the underlying surface, such as its electrical or thermal conductivity, are hardly affected.
Adam T. Paxson, Jose L. Yagüe, Karen K. Gleason, Kripa K. Varanasi (2013). Stable Dropwise Condensation for Enhancing Heat Transfer via the Initiated Chemical Vapor Deposition (iCVD) of Grafted Polymer Films Advanced Materials DOI: 10.1002/adma.201303065