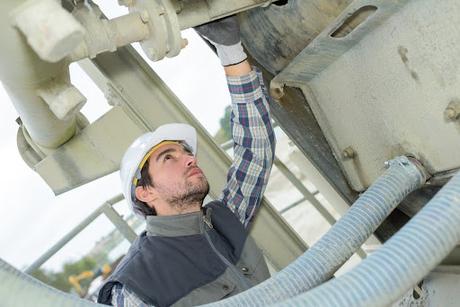
Successful construction companies understand the importance of keeping their expensive machinery clean and in top-notch condition. Equipment efficiency and longevity are critical in producing quality results in any building project. Mud, dirt, grease, and grime can significantly affect heavy machinery performance, resulting in production delays and unscheduled downtime.
While cleaning construction equipment is often an underappreciated chore, smart equipment owners recognize the benefits that come along with it. This article discusses the importance of periodically cleaning construction equipment and how to do it efficiently.
BENEFITS OF REGULAR CLEANING
1. Frequent cleaning serves as preventive maintenance for heavy machines since there is less strain on fixed and moving parts. Dirt and grime act as abrasives and friction agents. Hence, grimy equipment wears much faster and is not as efficient as the regularly cleaned ones.
2. Clean equipment is less likely to overheat compared to those covered with mud and grease. Although most machines are heat regulated, excessive dirt and oil may cause the engine to work harder, resulting in an overheated mess.
3. Construction delays and downtimes do not happen when the equipment is clean and fully operational. Broken machines due to unsanitary conditions may result in unnecessary expenditures and prolonged project execution.
4. Cleaning equipment is an excellent opportunity to check for any potential issues and damages. Metal cracks and rusting become a hindrance when overlooked. Regular maintenance and cleaning allow mechanics to resolve the problem before it escalates.
5. Frequently washed machinery enhances safety for construction workers. One example is when contaminant build-up around the machine’s hydraulic and electrical system may result in a dangerous low-out of high pressure and voltage. Poorly-maintained devices not only potentially endanger the operator but anyone on its line of fire as well.
6. Workers and mechanics work more efficiently with adequately cleaned equipment. Cleaning dislodges heavy build-ups and debris that may cause on-site injuries. Ensuring workers’ safety and using the right tools is critical in any building projects, like installing coastal zone access panels for any building near coastal areas.
7. Clean equipment makes a great impression on potential clients and future investors. It gives the impression that you value the safety of your workers and everyone, which makes for a loud and positive statement for your reputation in the construction industry.
PRODUCTS NEEDED TO CLEAN HEAVY MACHINERY EFFECTIVELY
Washing heavy pieces of machinery is a significant and tedious task. It requires technical knowledge to remove dirt, mud, and grease build-up successfully. There are systematic ways and specialized products to thoroughly clean each piece of equipment to ensure that the cleaning process is meticulous yet swift.
While some of these items are complicated to use, you can ensure that they get the job done. Here are the main products that machine cleaners need to clean heavy machinery effectively:
Personal Protection Equipment
Safety is paramount at any construction project to clean heavy machinery effectively. These are the first products to consider when starting a machinery cleaning task. Personal safety must be taken seriously at all times to avoid accidents on site. Machine cleaners should have these tools to keep them protected:
- The cleaners’ first line of defense is full-length overalls that protect their torso, arms, and legs. Nowadays, all construction workers use hi-visibility outerwear with disposable or reusable coveralls. There are also specialized rainwear and insulated protection when using hot water washing.
- As with all cleaning jobs, washing areas can be slippery, so protective anti-slippery footwear is essential. The best footwear is commercial rubber boots with anti-skid soles and toe protection.
- Face and eye protection are mandatory since splashes from dirt and grease under pressurized water can be hazardous. Eye contamination and chemical burns are existent during the cleaning process. Some examples are wrap-around headwear or full-face shields.
- Washing heavy machinery is a hands-on task, so it makes sense that wearing safety gloves is also mandatory. Some workers use leather gloves, but the most common ones have rubber and latex material.
Pressure Washing Equipment
There is no better way of removing stubborn dirt and grime than cleaning it with high-pressure water. The force of concentrated water quickly reaches tight places like hinges and seams that are impossible to hand brush alone. With the proper specifications, one can clean large construction machines such as excavators, dozers, scrapers, dump trucks, and tractor-trailers under pressurized water.
High-pressure cleaning involves two kinds of equipment which are pressure washers and water cannons. Both are reliable and efficient in washing heavy machinery, but they still have their uses. Water cannons expel larger volumes than pressure washers. You may find them on commercial equipment washing stations with closed-loop racks.
On the other hand, pressure washers are for small-scale devices and fine detailing as they only have a limited amount of water flow. Washing heavy machinery is a complex task that requires proper planning and scheduling while using the right high-pressure washer system.
Heavy Equipment Wash Racks
When it comes to equipment cleaning, there is no better substitute than using professionally designed wash racks. Many states regulate wash locations by prohibiting contaminated wash water from heavy machinery flowing on concave surfaces or groundwater reservoirs. Non-compliance may result in severe penalties, including jail time, not to mention being environmentally irresponsible.
Correctly assembled wash racks have water containment and recycling systems. The frame must be self-contained and enclosed to prevent polluted water from overflowing into the external water system. Excess water should then be captured and recycled in a closed-loop system before filtering and continually reusing.
Efficient waste management is critical in washing areas as contaminated water needs proper containing and removal if needed. Many wash racks contain a system where solid waste is removed, collected, and dried before transferring to a safe disposal site. The wash racks are often designed with above-ground solid management systems (SMS), while some depend on underground sumps and mud-drying pads.
Cleaning Detergents, Surfactants, and Water Temperature
Water is not enough to remove dirt, mud, and grease. Every cleaning wash system utilizes a cleaning solution that depends significantly on the type of equipment and the operation site.
The most common impurities compose of organic and inorganic compounds. Organics include hydrocarbons like lubrication grease and fuel residue, while inorganics refer to mineral compounds like sand, gravel, and dust. Another category involves both, whereas the most common mixture is polluted soil made of decomposing organics and static inorganic compounds.
Heavy equipment cleaning agents are often dissolved in water or other solvents to break the bond between dirt and the machine effectively. On the other hand, Chelating agents work on a molecular level where they attack the minerals on the water to soften it and prevent hard water from blocking surfactant efficiency.
It would be best if you considered the wash water temperature to avoid any error. Hot water effectively softens and warms large debris, while cold water washing is ideal with a suitable surfactant.
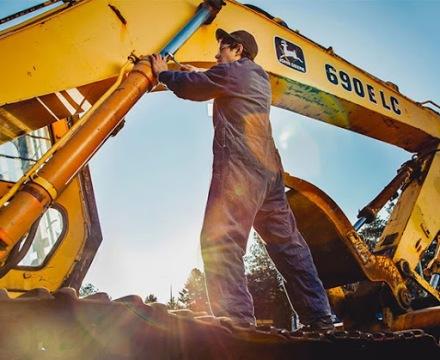
PROPER WASHING PROCEDURE
There is a distinct process of inefficiently cleaning heavy construction equipment promptly. Every equipment has its parts and attributes, but generally, this is how to conduct the cleaning process properly:
- Assemble all washing products and machinery in a contained wash rack with a secured loop system. Construction personnel must wear necessary PPE at all times during the process.
- With a steel bar and spade, large dry chunks of dirt and mud are manually pried loose from the undercarriage and chassis. All debris must be removed and collected before using pressurized water to prevent tripping hazards and liquefying the dirt, making it more challenging to handle.
- Blast the entire machine with a water cannon to remove larger debris. Hot water without detergent is also adequate at this stage.
- Grease accumulation is hand-removed since they will have softened by now due to the water pressure.
- Detergent is then scarcely applied to areas with visible contamination, including engine compartments and especially radiators.
- Soak the machine with cleaning agents for 15 minutes to ½ hours. It gives time for surfactant molecular action to dislodge all bonding chemically.
- Once time is up, use the water cannon again and blast the equipment starting from the top, allowing gravity to pull contaminants and wastewater to the wash pad floor naturally.
- Use small pressure washers and hand scrubbing for detailing tight places, seams, and joints.
- Hose rubber tires while glass surfaces are cleaned and polished.
- After cleaning the equipment, you may air dry or compress air to speed up the process.
- The construction machine is then removed from the wash rack, checked for maintenance, repaired, or placed in storage.
- Inspect the wash rack area for any solid waste and gray water that needs disposal. Finally, a perimeter check ensures that no contaminants escape.
Ensuring the cleanliness of heavy machines is essential for preventing any unnecessary accidents, expenses, and delays on site. High-performance equipment guarantees quality results from workers, which is the key to completing any successful construction project.