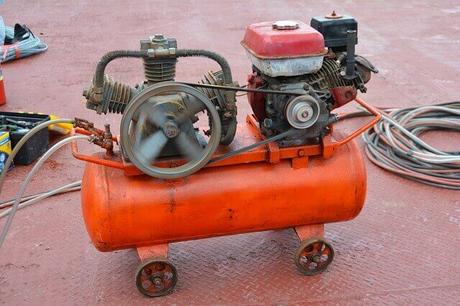
Air compressors have become an essential tool in almost every industry today, from manufacturing and construction to automotive repair and DIY projects. But have you ever wondered how an air compressor actually works? It may seem like a complex piece of machinery, but understanding the basics of its inner workings can help you make the most of this powerful tool.
Essentially, an air compressor works by converting power into potential energy stored in pressurized air. This compressed air can then be used to power a range of tools and equipment, from pneumatic drills and nail guns to sandblasters and spray guns. In this comprehensive guide, we’ll take a closer look at the different types of air compressors, how they work, and the key components that make them tick. So, whether you’re a seasoned professional or just starting out, read on to discover the fascinating world of air compressors and take your DIY game to the next level.
Basic principles of air compression
The basic principle of an air compressor is to convert power into potential energy stored in pressurized air. This compressed air can then be used to power a range of tools and equipment, from pneumatic drills and nail guns to sandblasters and spray guns. Air compressors work on the principle of Boyle’s law, which states that the pressure and volume of a gas are inversely proportional to each other. In other words, as the volume of a gas decreases, its pressure increases. This is what happens inside an air compressor. The compressor sucks in air from the atmosphere and compresses it into a smaller volume, thereby increasing its pressure.
Air compressors use different methods to compress air, such as positive displacement and dynamic displacement. Positive displacement compressors work by trapping a volume of air and then reducing its volume, while dynamic displacement compressors work by imparting kinetic energy to the air, which is then converted into potential energy through compression.
Types of air compressors
There are several types of air compressors, each with its own unique features and advantages. The most common types of air compressors are:
1. Reciprocating air compressors – These compressors use a piston and cylinder arrangement to compress air. They are best suited for intermittent use and are commonly used in small workshops and DIY applications.
2. Rotary screw air compressors – These compressors use two interlocking screws to compress air. They are ideal for continuous use and are commonly used in large workshops and industrial applications.
3. Centrifugal air compressors – These compressors use a high-speed impeller to impart kinetic energy to the air, which is then converted into potential energy through compression. They are best suited for large-scale industrial applications.
Components of an air compressor
An air compressor consists of several key components, each with its own unique function. The most important components of an air compressor are:
1. Compressor pump – This is the heart of the air compressor and is responsible for compressing air. It can be either a reciprocating or rotary screw type.
2. Motor – The motor powers the compressor pump and is usually electric or gas-powered.
3. Tank – The tank stores the compressed air and allows it to be used when needed. There are some common types such as 80-gallon, 60-gallon, 30-gallon, 20-gallon, etc. Read this article for more info.
4. Pressure switch – The pressure switch controls the on/off cycle of the compressor.
5. Regulator – The regulator controls the pressure of the compressed air as it is released from the tank.
How an air compressor works – step by step
Now that we’ve covered the basics of air compressors, let’s take a closer look at how they work. The following is a step-by-step guide to the operation of a typical reciprocating air compressor:
1. The motor powers the compressor pump, which draws in air from the atmosphere through an intake valve.
2. The compressor pump compresses the air and delivers it to the tank through a discharge valve.
3. As the tank fills with compressed air, the pressure inside the tank increases.
4. Once the pressure inside the tank reaches a pre-set limit, the pressure switch turns off the motor, and the compressor stops running.
5. When the pressure inside the tank drops below a pre-set level, the pressure switch turns on the motor, and the compressor starts running again.
6. The regulator controls the pressure of the compressed air as it is released from the tank, allowing it to be used to power pneumatic tools and equipment.
Uses of air compressors
Air compressors have a wide range of uses, from powering pneumatic tools and equipment to inflating tires and cleaning surfaces. Some common uses of air compressors include:
1. Pneumatic tools and equipment – Air compressors are commonly used to power pneumatic tools such as drills, saws, and nail guns.
2. Inflating tires – Air compressors can be used to inflate tires quickly and efficiently.
3. Sandblasting – Air compressors can be used to power sandblasters, which are used to clean surfaces and remove rust.
4. Painting – Air compressors can be used to power spray guns, which are used for painting and finishing surfaces.
Common problems with air compressors and troubleshooting tips
Like any piece of machinery, air compressors can experience problems from time to time. Some common problems with air compressors include:
1. Overheating – Overheating can be caused by a variety of factors, including a dirty air filter, low oil levels, or a malfunctioning pressure switch.
2. Leaks – Air leaks can be caused by a variety of factors, including worn-out seals, damaged hoses, or loose fittings.
3. Low pressure – Low pressure can be caused by a variety of factors, including a malfunctioning regulator, a clogged air filter, or a leak in the system.
4. Noisy operation – Noisy operation can be caused by a variety of factors, including worn-out bearings, loose components, or a malfunctioning motor.
To troubleshoot these problems, it is important to refer to the manufacturer’s manual and follow the recommended maintenance procedures.
Maintenance of air compressors
Proper maintenance is essential to ensure the longevity and efficiency of an air compressor. Some important maintenance tasks include:
1. Checking and replacing the air filter regularly.
2. Checking and changing the oil regularly.
3. Inspecting and tightening all fittings and connections.
4. Draining the tank regularly to remove moisture.
5. Checking and replacing worn-out parts as needed.
Safety precautions when using air compressors
Air compressors can be dangerous if not used properly. Some important safety precautions to follow include:
1. Always wear eye and ear protection when using an air compressor.
2. Never exceed the maximum pressure rating of the tank or any components.
3. Always turn off the compressor and bleed the tank before performing any maintenance.
4. Keep the compressor and all components clean and free of debris.
5. Always follow the manufacturer’s instructions and recommended safety precautions.
Conclusion
In conclusion, understanding how an air compressor works is essential for anyone who uses this powerful tool. By knowing the basic principles of air compression, the different types of air compressors, and the key components that make them tick, you can make the most of this versatile tool and take your DIY game to the next level. Remember to follow the recommended maintenance procedures and safety precautions to ensure the longevity and efficiency of your air compressor.