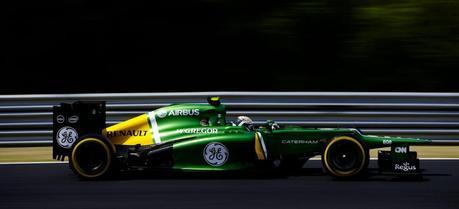
Starting with the 2014 season, F1 will enter a new, super-efficient era. The engines will still generate up to 700 horsepower, but they will be capped at 1.6 liters of displacement and use around a third less fuel than today. GE engineers will help Caterham F1 Team’s cars get around the course more quickly by focusing on four areas: big data analytics, fiber-optic sensing, composites manufacturing, and heat management.
Scientists working at GE Global Research (GRC) are using advances in big data analytics and materials science to help Caterham F1 Team’s Formula 1 race cars perform better. “It’s a win-win partnership for both of us,” says Matt Nielsen, GRC’s principal scientist for controls, electronics, and signal processing. “They are on a very short technology development cycle, often only two weeks between races. We learn how to apply our technology in that time-scale.”
Each Caterham car has some 500 sensors buried inside its wheels, engine, gearbox, chassis and elsewhere. Together they generate up to 1,000 data points per second. “These cars are roving sensor platforms traveling at 200 mph,” says Nielsen, who grew up as an open-wheel racing fan.
The gigabytes of data travel to Caterham’s UK headquarters for analysis, where team engineers combine it with information generated during the development cycle, wind tunnel tests and even from a driver simulation system. “We were shocked by how much data they had,” Nielsen says. “We are helping them look at how they store, assemble and make connections between pieces of data, and pull out those nuggets that help them fine-tune their cars. The analytics developed by GE have the potential to cut Caterham’s data processing by half.
Some of the data may soon come from advanced fiber-optic sensors. The GE team built them to accurately measure the downforce on the front wing below the car’s nose. They believe that the embedded instruments can improve the wing’s design and help the vehicle go faster around turns.
Most today’s cars are built mainly from carbon composites. The few exceptions include the engine, the drivetrain, and pipes. GE materials scientists are helping the racing team replace aluminum cooling tubes with composites and reduce weight. “Every ounce adds up,” Nielsen says. “We’ve made good progress and are working to transfer the manufacturing process to them.”
Starting with the 2014 season, F1 will raise its engine efficiency requirements. In order to comply, engines will come equipped with advanced turbochargers and energy recovery systems, which will boost performance. GE engineers are helping Caterham design sophisticated intercoolers that reduce the temperature of the air the turbocharger pumps into the engine. “You don’t want a lot of pressure drop, but you want the air as cool as possible,” Nielsen says. “We know a lot about heat transfer and are using that to help build analysis tools for Caterham.”
Nielsen says that the Caterham team is solving problems very similar to what GE engineers do every day. For that reason, there are a number of places where collaboration could lead to insights beyond just F1 racing cars. “It’s all very analogous to what we do in the field with gas turbines, aircraft engines and the Industrial Internet,” he says.
Meanwhile, we at the Daily Fusion hope that this will help Caterham F1 Team to move forward from the last place in the F1 team standings.