
Researchers at the MESA+ research institute at the University of Twente, Netherlands, have developed a new type of hybrid membrane that allows to separate gases from each other in an energy-saving way, even under extreme conditions.
The chemical industry is responsible for one third of the energy consumption in the Netherlands. Approximately 40% of the energy is used for separation processes in which the products of chemical reactions are separated from each other.
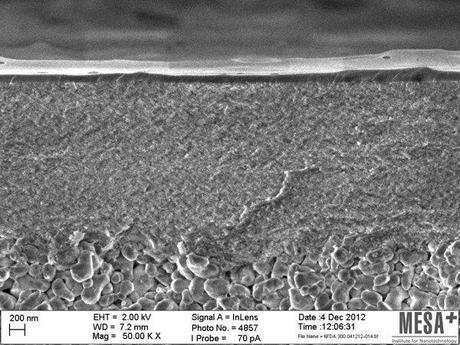
A high-resolution microscopic image of a new type of hybrid gas separation membrane. (Credit: See citation at the end of this article)
Currently, gases are separated via processes such as of cryogenic distillation, during which gases are liquefied by intensive cooling, or through absorption processes. The disadvantage of these methods is that they often require a large amount of energy.
Using membranes that selectively allow one gas through but retain another allows energy-efficient separation. However, up until now there were no suitable organic membranes available that also performed at high temperatures and high pressures. Conventional, organic membranes are made of polymers and are not stable enough at high temperatures.
The gas separation membrane developed by researchers at the University of Twente, which comprises of both organic and inorganic components, remains effective at high temperatures (of up to 300 degrees Celsius) and high pressures. This offers advantages for gas separation in the chemical industry, as many processes involve high temperature and high pressure conditions. The researchers published their research in the Journal of the American Chemical Society (see footnote).
The membrane is approximately 100 nanometers thick and consist of ceramic nanoparticles that are bound to each other at multiple points by long-chain organic molecules. These then form a sort of three dimensional web (with the nanoparticles as the junctions) and this web allows certain gases to pass through and retains others. As it is possible to choose the length of the organic molecules used (and therefore how fine the web is), it is easy to design suitable membranes for all kinds of applications. An added advantage is that the hybrid membranes are relatively easy to produce on a large scale, as the techniques used are compatible with those for producing the conventional membranes often used in water purification.
Michiel J. T. Raaijmakers, Mark A. Hempenius, Peter M. Schön, G. Julius Vancso, Arian Nijmeijer, Matthias Wessling, and Nieck E. Benes (2014). Sieving of Hot Gases by Hyper-Cross-Linked Nanoscale-Hybrid Membranes Journal of the American Chemical Society, 136 (1), 330-335 DOI: 10.1021/ja410047u