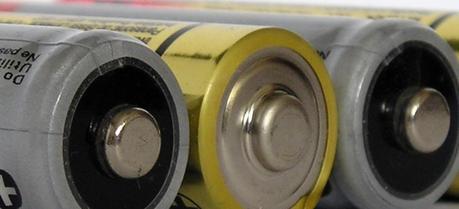
Kui Yao and co-workers from the A*STAR Institute of Materials Research and Engineering in Singapore have discovered a way to give lightweight polymer vibration harvesters a hundredfold boost in energy output—a finding that may help to eliminate manual battery recharging in microsensors and mobile devices.
Many vibration harvesters contain piezoelectric substances that create an electric voltage when mechanically bent. By fabricating piezoelectric materials into cantilevers that resemble a diving board, these devices can oscillate from ambient vibrations and generate electricity. Researchers often use piezoelectric ceramics because they impart large amounts of electrical charges; however, the brittleness of ceramics makes them unsuitable for prolonged and large vibrational movements.
Yao and co-workers investigated a plastic-based piezoelectric material, polyvinylidene fluoride (PVDF), which is low cost and readily undergoes mechanical strain. To make efficient vibration harvesters from PVDF, researchers must stack the polymer in multiple layers, improving the output current and reducing the electrical impedance that is inherent to piezoelectric materials. But when too many thin piezoelectric layers are stacked, the cantilever can become too stiff for bending-mode vibrational harvesting.
To optimize piezoelectric harvesting with plastic films, the team deployed an analytical approach. Developing a mathematical model of a multilayered polymer cantilever coated with metal electrodes, the researchers systematically calculated how different material parameters affected the energy output.
Their simulations revealed some often-ignored factors “such as the thinness of electrode coatings and the material’s electrical parameters,” says Yao. “These can have a dramatic effect on the electricity generated by bending multilayer polymers.”
One key parameter identified was the need to match the electrical impedance with an optimum load resistance. The researchers’ analysis showed that the energy output of a 22-layered piezoelectric structure could be from 5 to 400 times higher than a single-layer piezoelectric polymer of similar dimensions.
The team then tested the feasibility of their analytical results by fabricating a PVDF-based vibrational harvester on a flexible aluminum substrate. They used scalable dip-coating procedures to build up polymer multilayers and ensured thin metal electrode coatings with physical vapor deposition techniques.
“Our experimental results are promising and show that, for many practical applications, piezoelectric polymer multilayers may enable harvested energy to replace batteries,” notes Yao.
The A*STAR-affiliated researchers contributing to this research are from the Institute of Materials Research and Engineering.
Lei Zhang, ., Oh, S., Ting Chong Wong, ., Chin Yaw Tan, ., & Kui Yao, . (2013). Piezoelectric polymer multilayer on flexible substrate for energy harvesting IEEE Transactions on Ultrasonics, Ferroelectrics and Frequency Control, 60 (9), 2013-2020 DOI: 10.1109/TUFFC.2013.2786