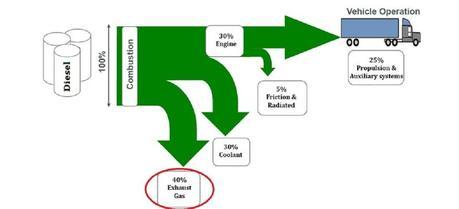
A new European research project, “TEG for Energy Efficiency in Heavy Vehicles”, will develop and demonstrate an efficient and inexpensive thermoelectric generator to harvest waste heat in trucks and heavy vehicles based on thermoelectric materials.
Transportation of goods is consuming an increasing part of our transport fuel, and heavy automotive applications are foreseen to rely on internal combustion engines still for many years to come, fueled by fossil diesel today, biofuels in the future.
Accordingly, technologies improving overall fuel efficiency will have a clear benefit in terms of reduction of CO2 emissions and better use of limited energy resources. Thermoelectric generators (TEGs) are seen as one of the technologies with a potential to improve the efficiency by harvesting electricity from excess heat otherwise lost with the exhaust.
DTU Energy Conversion at the Technical University of Denmark is part of a new research project, “TEG for Energy Efficiency in Heavy Vehicles”, together with Volvo, Behr Group, TEGnology, Aarhus University and Panco. This project-group covers not only the key scientific competences needed to develop the technology but also the entire value chain and channel to market.
The project has started, and fleet owners of heavy vehicles and trucks have been invited to provide input to the project. This will be followed by research on both thermoelectric materials and modules to improve their long-term reliability when subjected to high temperatures. The project aims to develop and demonstrate an efficient and inexpensive thermoelectric generator (TEGs) to harvest waste heat in trucks and heavy vehicles based on thermoelectric materials.
The TEGs will supplement and eventually replace the on board generator in the vehicle, while at the same time generate the necessary power without the use of additional fuel. The initial performance target of the project is to improve the system efficiency by 1%, i.e. save 1% of the fuel. Even this will constitute a significant competitive advantage in the market for heavy trucks.
The role of DTU Energy Conversion is to use its extensive knowhow in thermoelectric materials, advanced test rigs and computer models to characterize and test the TEG modules made by the other partners.
“You can compare it to building with Lego bricks. TEGnology and Aarhus University develop the materials, Panco makes the bricks, i.e. the TEGs, we make sure that they fit together and work properly using state-of-the-art test and characterization equipment, while Volvo and Behr build the actual demonstration model”, explains work package leader and senior researcher at DTU Energy Conversion, Kaspar Kirstein Nielsen.
A full scale test in an operating truck with data monitoring is very costly and therefore Volvo has designed test bench setups to bring down the expenses and also allow systematic repetitions of the test design.
The project will be finished in 2016.
Earlier we reported that a EU-funded project, “Nano-carbons for versatile power supply modules” (NanoCaTe), aims to develop thermoelectric harvesters which are able to operate in the temperature range from room and body temperature to 100°C.