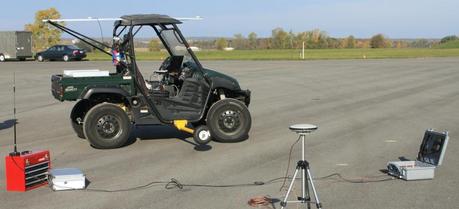
Junmin Wang, assistant professor of mechanical engineering at Ohio State University, and his team are designing an unconventional four-wheel independently-actuated electric car. This vehicle has no no transmission and no differential; and each of its four wheels has its own built-in electric battery-powered motor, meaning the car has the ability to make sharp turns and change direction very quickly.
Without an exceptional traction and motion control system, however, this car would be quite difficult to drive, providing a driving experience vastly different from anything else on the road, and almost certainly more dangerous. To counter that, the vehicle’s onboard computer will calculate and ensure motion control to keep the car stable and operating smoothly. The system, which receives and analyzes input data 100 times per second from the steering wheel, the gas pedal and brake, works out how each wheel should respond.
“Without it, the car is quite difficult to drive because the wheels are not coordinated,” says the National Science Foundation (NSF)-funded researcher, who also directs the university’s vehicle systems and control laboratory. “You feel like you are driving something uncontrollable. You could flip over, or travel along an undesired path, or cause a crash. But when the ‘controller’ is active, based on feedback loops, the vehicle motion can be controlled, just as the driver expects.”
With a safe and reliable control system, this new electric vehicle ultimately should make the perfect in-city car. It’s efficient and maneuverable—and has no emissions. Because it is all electric, “you can use wind power or solar power, and contribute toward reducing our dependency on fossil oils,” Wang says.
The computer calculates exactly how much torque the car needs for each of its four wheels. Moreover, because each wheel is independent, “one wheel can be doing the braking, while another is doing the driving,” Wang says. “The computer gets signals from the driver from the steering wheel and pedal positions, then calculates the desired speed, or vehicle motion, based on a mathematical model.”
The experimental four-wheel independently-actuated car weighs only about 800 kg (1,764 lbs), which makes it energy efficient. The researchers retrofitted a commercially available utility terrain vehicle chassis and removed the engine, transmission and differential, then added a 7.5 kW electric motor to each wheel and a 15 kW lithium-ion battery pack. A single electrical cable connects the motors to a central computer.
The researchers tested the car and its controller on normal road conditions at the Transportation Research Center in East Liberty, Ohio, an independent automotive site for vehicle crash, emissions and durability testing. On roads with good conditions, the car followed a driver’s “desired” path within four inches.
To see how it performs on slippery roads, they brought the car to an empty west campus parking lot on a snowy day. The car maneuvered with an accuracy of up to eight inches, and the vehicle traction and motion control system prevented “fishtailing” through independent control of the left and right sides of the car.
Rongrong Wang, Junmin Wang (2013). Tire–road friction coefficient and tire cornering stiffness estimation based on longitudinal tire force difference generation Control Engineering Practice, 21 (1), 65-75 DOI: 10.1016/j.conengprac.2012.09.009