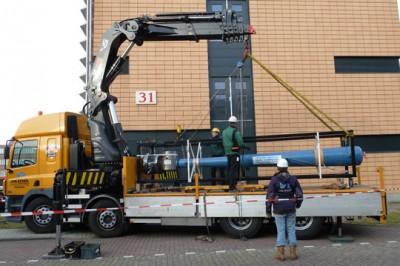
Energy Research Centre of the Netherlands (ECN) and Bronswerk Heat Transfer (BHT) have developed and built a heat pump that uses a very special technology for heat transfer: sound waves.
The new thermoacoustic heat pump is currently being tested by ECN. In a few years Dutch industry should be able to make significant energy savings using this type of heat pump. Dutch industry, which accounts for one fifth of energy consumption in the Netherlands, sends hundreds of petajoules worth of residual heat up the chimney each year in the form of water vapor, says Anton Wemmers, expert in energy savings in industry at ECN. So putting this heat to good use in the factory or elsewhere could make a huge difference.
SEE ALSO: Novel Battery Tech Harvests Waste Heat
However, conventional heat exchangers—which have for years been the mainstay of BHT—are by no means always suitable for this. Existing heat pump technology whereby a refrigerant is evaporated and condensed, for example in a refrigerator or air-conditioning unit, is unsuitable for the high temperatures involved in industry.
A thermoacoustic device basically consists of heat exchangers, a resonator, and a stack (on standing wave devices) or regenerator (on traveling wave devices). Depending on the type of engine a driver or loudspeaker might be used as well to generate sound waves.
Consider a tube closed at both ends. Interference can occur between two waves traveling in opposite directions at certain frequencies. The interference causes resonance creating a standing wave. Resonance only occurs at certain frequencies called resonance frequencies, and these are mainly determined by the length of the resonator.
The stack is a part consisting of small parallel channels. When the stack is placed at a certain location in the resonator, while having a standing wave in the resonator, a temperature difference can be measured across the stack. By placing heat exchangers at each side of the stack, heat can be moved. The opposite is possible as well, by creating a temperature difference across the stack, a sound wave can be induced. The first example is a simple heat pump, while the second is a prime mover.
A process is quite similar to a Stirling cycle. Unlike Stirling engine, though, no moving parts are used. In a thermoacoustic engine, the sound wave controls the compression, displacement and expansion of the working medium helium. The working medium thereby undergoes a cycle that amplifies the sound wave.
In a thermoacoustic heat pump developed at ECN, industrial waste heat is used to power the engine. The ECN technology can operate across a wide temperature range: from -50 to +250 °C. According to the developers of the heat pump, the 10 kW prototype that is currently undergoing testing will be scaled up to at least 1 MW for use in industry.