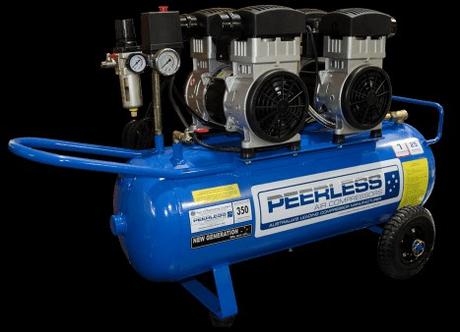
Air compressors are essential tools used in various industries and applications, providing compressed air for powering pneumatic tools, machinery, and processes. When selecting an air compressor, one important decision is whether to choose an oil-lubricated or oil-free model. This article aims to provide a comprehensive comparison of these two types, exploring their characteristics, differences, and factors to consider when making a choice.
Oil-Lubricated Air Compressors
Oil-lubricated air compressors rely on oil to lubricate the internal components, ensuring smooth operation, reducing friction, and extending the compressor’s lifespan. Here are key points to consider:
- Lubrication: The use of oil lubrication in these compressors significantly reduces wear and heat generation, contributing to improved performance and durability.
- Performance: Oil-lubricated compressors are known for their higher capacity and efficiency. They excel in heavy-duty applications where a continuous high volume of compressed air is required.
- Noise Level: Due to the lubrication of moving parts, oil-lubricated compressors tend to operate more quietly compared to their oil-free counterparts.
- Air Quality: While oil-lubricated compressors can deliver clean and dry air, there is a slight risk of oil carryover into the compressed air stream. This may not be suitable for applications that require completely oil-free air, such as certain medical or food processing applications. However, this risk can be minimized through proper filtration and regular maintenance.
- Maintenance: Oil-lubricated compressors require regular oil changes, filter replacements, and general maintenance tasks to ensure optimal performance. However, these maintenance intervals are typically longer compared to oil-free compressors.
Oil-Free (Oilless) Air Compressors
Oil-free air compressors utilize specialized coatings, materials, or non-contact designs to eliminate the need for oil lubrication. Here are important considerations regarding oil-free compressors:
- Lubrication: Oil-free compressors eliminate the use of oil by employing alternative mechanisms such as self-lubricating coatings or non-contact designs. This reduces the risk of oil carryover and eliminates the need for oil changes.
- Performance: Oil-free compressors are suitable for light to moderate-duty applications that do not require continuous high-volume air delivery. While they may have slightly lower capacity and efficiency compared to oil-lubricated compressors, they fulfill the needs of many industries and applications effectively.
- Noise Level: Oil-free compressors often generate more noise due to higher operating speeds and the absence of oil lubrication. However, advancements in technology have led to quieter oil-free compressor models.
- Air Quality: Oil-free compressors excel in providing oil-free, contaminant-free, and dry compressed air. They are commonly employed in industries such as pharmaceuticals, electronics, and food processing, where strict air quality standards must be met.
- Maintenance: Compared to oil-lubricated compressors, oil-free compressors generally require less maintenance since there are no oil changes or filter replacements. However, other components may require regular maintenance and monitoring.
Which Is Better Oil or Oilless Air Compressor?
Choosing between an oil-lubricated or oil-free air compressor depends on various factors, including the application requirements, desired air quality, maintenance considerations, and personal preferences. Oil-lubricated compressors are suitable for heavy-duty applications that require high capacity and efficiency, with some tolerance for oil carryover. On the other hand, oil-free compressors are preferred in industries that demand oil-free, contaminant-free, and dry compressed air.
It is crucial to carefully evaluate the specific requirements of your application, such as air quality standards, noise levels, maintenance needs, and operational demands, to make the most appropriate choice. Consider factors such as the required air volume, desired pressure levels, the presence of sensitive equipment or processes, and any specific industry regulations or standards that need to be met.
Furthermore, it is essential to consult with reputable compressor manufacturers or suppliers who can provide expert guidance based on your specific application needs. They can offer valuable insights into the advantages and limitations of each type of compressor, helping you make an informed decision.
Remember that regular maintenance and proper filtration systems play a vital role in ensuring the long-term performance and reliability of any air compressor, regardless of whether it is oil-lubricated or oil-free. Neglecting maintenance tasks can lead to decreased efficiency, increased energy consumption, and potential issues with air quality.
Conclusion
In conclusion, the choice between an oil-lubricated or oil-free air compressor depends on a careful evaluation of various factors, including performance requirements, air quality standards, maintenance considerations, and industry-specific needs. Both types have their advantages and are suited to different applications. By understanding the characteristics and differences between oil-lubricated and oil-free compressors, you can make an informed decision that best suits your unique requirements, ensuring optimal performance, longevity, and air quality in your compressed air system.