Quality assurance and quality services are the keys to the business's success. This is why many businesses implement the Six Sigma process into the workforce to tackle the problem of wastage and improve the efficiency of working.
The product services are considered best when performed with durability, reliability, and eliminating wastage. Hence, it is crucial to carry out the entire management process because this will enable you to deliver the best quality products to the customer to satisfy their needs. In return, you achieve success.
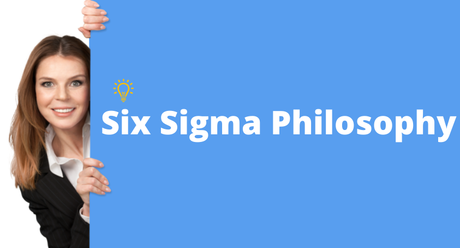
However, several parameters decide the product quality, performance, functionality, reliability, suitability, relevance, timeliness, and consistency in delivering quality work. Therefore, use the Six Sigma methodology and practices to help your business organization create and design the products according to the customer's requirement.
Another key benefit of using the Six Sigma tools in the workplace is maintaining the quality and productivity to increase the revenues and achieve targets faster.
What is Six Sigma?
Six Sigma is the process and methodology used in the businesses for quality management, which further helps the business organizations to improve the services and products by eliminating the defects.
Implementing Six Sigma into the workplace aims to streamline the entire process and quality control management. Therefore, the concept was reframed to help the companies to maintain the quality.
Quality control management refers to the process carried out in the organization from the beginning to the end of the projects. This is to ensure that all the activities are well-planned, designed, and implemented into the project field to obtain top-quality products and improve the performance of the businesses.
The Six Sigma Certification program, which confirms a candidate's expertise in implementing Six Sigma approaches, was created by Motorola & GE.
A Six Sigma Certification verifies a professional's ability to detect risks, mistakes, or faults in a company process and determine how to eliminate them. Six Sigma offers several certificates with accrediting organizations.
What is Lean Six Sigma?
Lean Six Sigma is a data-driven, fact-based improvement methodology that prioritizes defect avoidance above fault discovery. It improves customer satisfaction and underside results by lowering variance, waste, and order cycle while encouraging work uniformity and flow, resulting in a competitive advantage. It applies whenever there is a variety of waste, and every employee should be a part of it.
By implementing the Six Sigma concept and quality management, you can achieve the business goals faster and ineffective. So, let's read about the Six Sigma methodology briefly and how to take the Lead Six Sigma Green Belt certification course online.
Lean Six Sigma Methodologies
Two different Lean Six Sigma methodologies are applied into the workplace, which is as follows.
Six Sigma DMADV
is the core concept that involves the following steps: defining, measurement analysis, design, and verification. The steps are as follows.
Define: During the step, the business will evaluate the realistic goals to determine a pathway to achieve success and meet consumer goals.
Measure: In this step, the business individuals and teammates will measure the clients' requirements. This will be the critical step because it will determine the pathway to achieving goals and following the project's layout.
Analyze: The next step is an analysis of the products and measurement goals. Moreover, this will also help estimate the entire life cycle you follow in the project.
Design: Next step in the process is to design the method and prototype, which is used to find out the wastage, errors, and other things. This way, teammates can modify them and further move towards the verification step.
Verify: This would be the final step in the process. It is to verify the iteration of the process and products that the clients and customers validate in internal and external methods.
Lean Six Sigma DMAIC
This process and methodology refer to the Design for Six Sigma. The methodology will include five different phases, and the steps are defined, measured, analyzed, improved & control. The whole process is as follows:
Define: This is the first step in the process that helps define the key pain areas and the requirements of the projects. The ultimate goal is to measure the customer's needs so that you can define the process accordingly to meet their requirement.
Measure: This is the second step required to evaluate the performance of the current business process, which is done with a data collection plan. The process can determine the wastage and defects present in the projects and collect the above metrics.
Analyze: In this step, the businesses need to analyze the entire process to target the root cause from where the defect arises or presents. Moreover, it is also helpful to identify the issues related to the current strategies that may disturb the entire process to achieve business goals faster.
Improve: The process includes eliminating defects and wastage and understanding the root cause by finding out creative and advanced level solutions.
Control: The last step in the process is control. In this, the whole process is run in a controlled manner so that the previous errors will be eliminated and everything runs smoothly.
What is The Key Difference Between the DMADV and DMAIC?
Both approaches appear to have the least variations at first appearance, yet they are used in distinct contexts. When current processes or products are discovered to be unable to satisfy the customer's expectations or are not functioning to the expected standards, DMAIC is used .
DMADV is intended for situations in which a company has to build or construct a new product or process or when an old product, despite being optimized, fails to function as planned.
Conclusion
Six Sigma certificates can help you advance in your profession by certifying you as an expert in identifying and eliminating faults. As a result, your management levels in a company will rise.
These certificates would undoubtedly be included in your CV. If you want to obtain certification, look for authorized training providers. It should allow you to study at your speed and alternatives for delivery modes such as classroom, blended learning, and instructor-led.