I really enjoyed building the timber frame (pictures below), with occasional assistance from volunteers Robert and Steve. My previous experience of working with wood has essentially involved mostly chopping it up and burning it to fire kilns, or walloping bits of it together with nails to form basic kiln sheds. It's very satisfying to work a bit more sensitively with it, cutting mortice and tenon joints and half-lap joints and fixing it together with wooden dowel and glue rather than screws or nails. The joints are - unsurprisingly - not the neatest and don't bear up to too much close scrutiny but they're pretty much in the right place. The whole structure is more or less square and true, is where it's meant to be and is now holding up the new roof across the back of the bungalow. I find this last bit in particular both very pleasing and very unnerving.
The roof will hopefully start to get it's waterproof EPDM rubber waterproof coating next week, the windows and doors have all been measured up and are now being manufactured, so things are moving along. There's ridiculous amount still to do, not least trying to get some render on the straw before it's too late (ie: before it gets frosty out there). As throughout the build, the trick with not freaking out is to keep dealing with one thing at a time. If I look at everything that needs doing I'm prone to larger than normal amounts of gibbering. If I focus on the task in hand (whichever task it is) then I can get it done and mostly enjoy it (with the exception of priming/undercoating both sides of 40 metres of fascia board - today's task and a particularly dull one).
Building doorsteps up to correct height so that when the frame is fitted the top of the frame is level with finished floor level, producing level mobility thresholds. Timbers of the same size as the one above also fitted to the sides of the door and window openings, to form the box that the doors/windows will be fitted into.
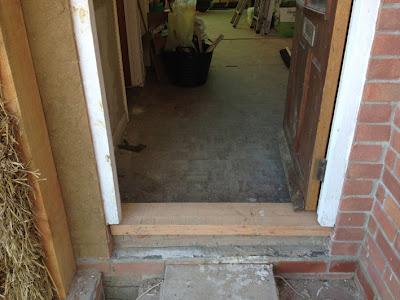
Front doorstep doctored for same reasons as above. Bottom hacked off door so it can remain in place until last possible moment. We're having different types of door in different places, all with different thicknesses of frame, making calculating what height to set the doorstep a right old headache!
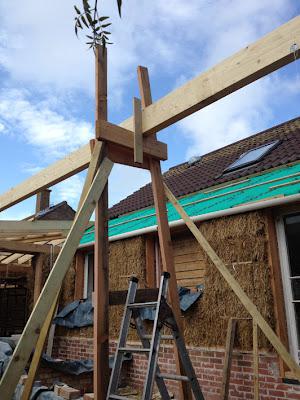
Stage one of conservatory structure - eaves beam on (very) temporary support.
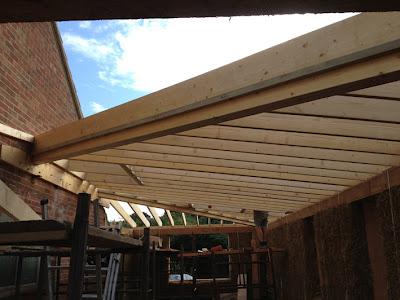
Extension roof structure taking shape. It's a shame none of this will be visible, it's beautiful!
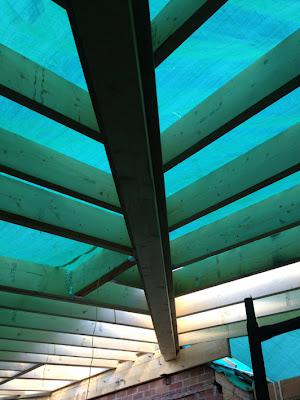
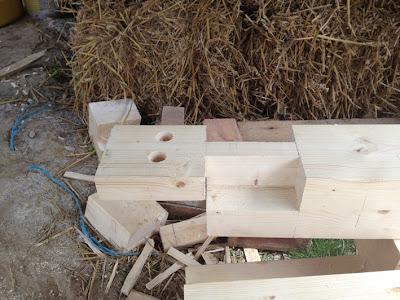
The most complicated carpentry I've undertaken. Notching top of glulam timber post to support eaves beam and cross-timbers.

The post in place, with douglas fir cross-timbers and glulam base-plate added. It's all pegged and glued, no screws.
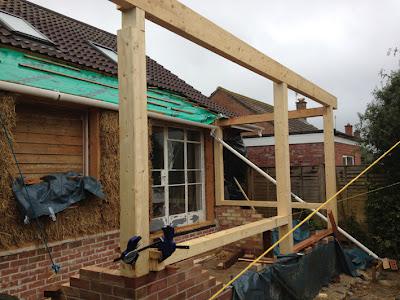
Self-supporting now.
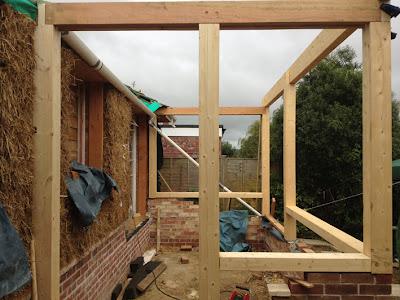
My first foray into timber-framing, nearly complete.
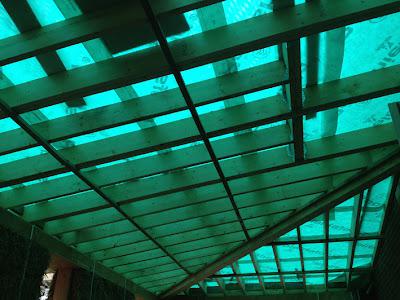
Breather membrane on extension roof.
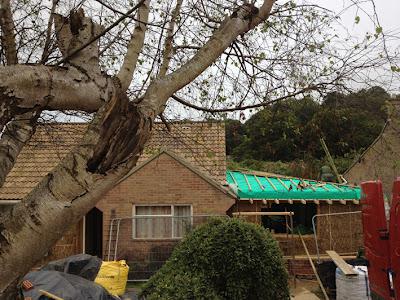
50mm battens on top of membrane to provide ventilation above it (to remove any condensation).
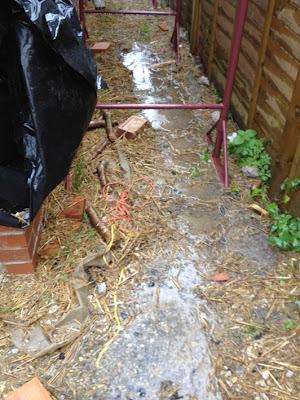
Raining again.

Mike finds out whether my timber frame is at the right height and can support the rafters.
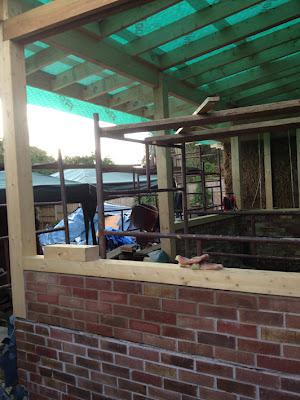
Timbers and membrane across conservatory, brickwork built up to frame. Very very satisfying.
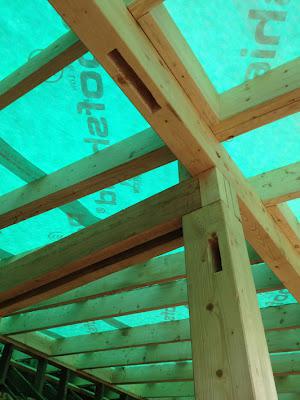
Last details of the timber-framing, notches cut to receive tongues of a diagonal timber. Working this out took a disproportionately long time. There was a lot of standing up a ladder with a tape measure, a square and a bewildered expression.
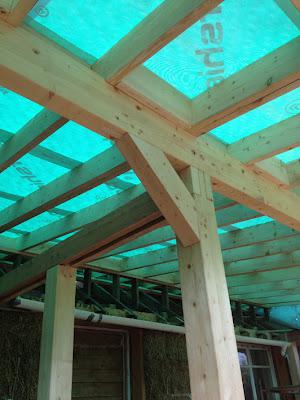
Ta-da! It fitted - phew!
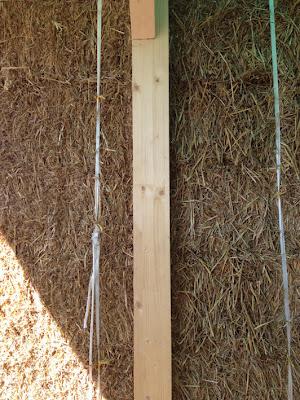
Straw to the left: strimmed, ready for render. Straw to the right: not yet strimmed, straggly, not ready for render.
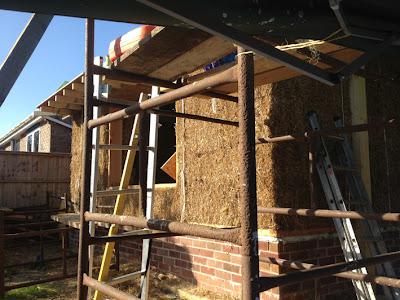
Trimmed end.
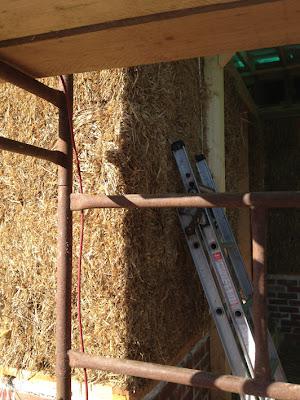
Trimmed corner.
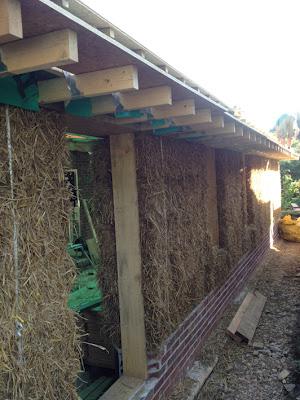
Soffit overhangs taking shape. These will keep the worst of the direct rain off the walls.
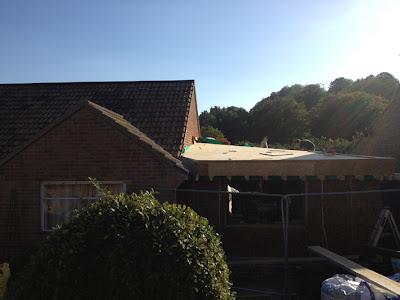
Boarding the roof with Smartply, highly sustainable OSB/Oriented Strand Board: formaldehyde free (unlike most OSB) and made from forestry trimmings/waste.
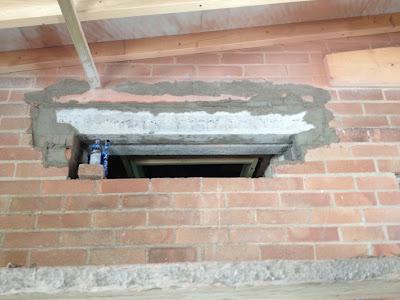
Fitting lintels ready to cut new opening for corridor into extension. Had a long drawn-out and very boring saga with these, trying to find a way to get them above ceiling height so we could have continuous ceiling level through the opening, whilst still supporting a critical structural beam of the exiting roof. Turned out that all the lintels capable of supporting that beam and its load were too big (apart from one that was specified but appears not to actually exist), so now there'll be a slight step in the ceiling.
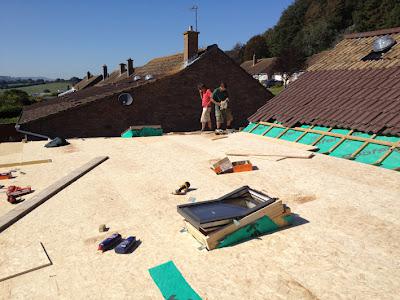
Roof windows fitted, nearly all boarded. The roof is huge when viewed from above - partly because it comes up over the existing roof by quite a lot.
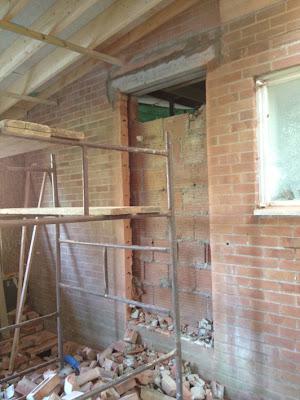
Outer brick skin removed, no collapse yet, good.
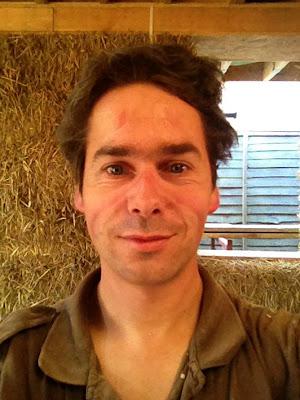
Brick Man (after using the dust-monster disc cutter to cut the opening above, wearing goggles and mask).
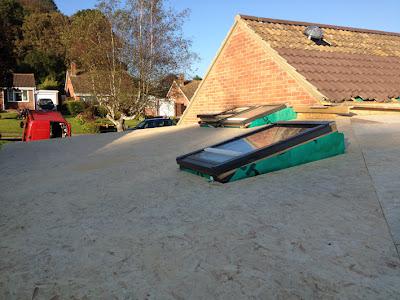
Up on the rooooof....
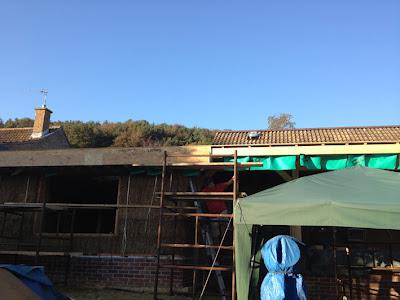
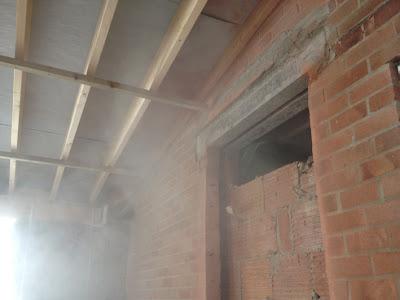
Dust. This is just the dust that spilled outside when cutting through remaining bricks from the inside. On the inside, with a tarpaulin hung to contain the worst of the dust I was in my own private dust cloud.
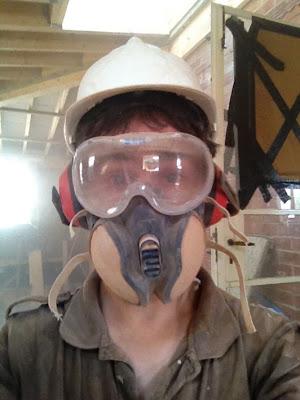
PPE Man (PPE: Personal Protective Equipment). Suitable attire for cutting holes in walls in a personal dust cloud, when mistrustful of bricks/lintels and not wishing them to fall on my head.
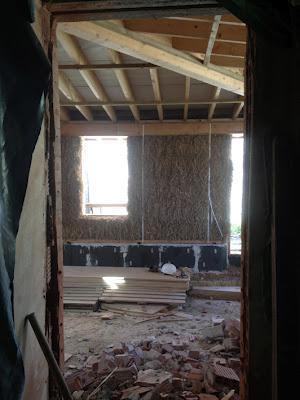
New opening! Felt momentous. Now boarded over to maintain security.
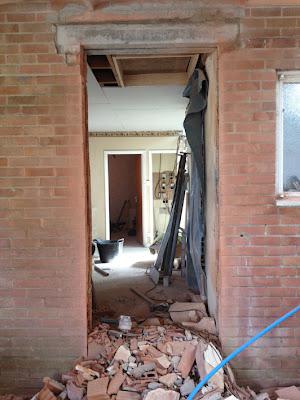
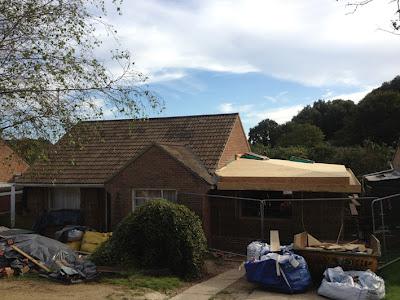
Roof and internal gutter now fully boarded and ready to be covered with EPDM rubber waterproof membrane (the least toxic/polluting and lowest embodied energy option for sealing the roof beneath the green-roof build up. Also extremely durable and reliable.
COMMENTS ( 1 )
posted on 03 September at 05:21
rat Long Sleeve Floor-leng