Efficient Production with zero downtime is the dream of every production supervisor, while this could be regarded as a utopian thought, the possibilities of reducing downtime can be achieved with the help of efficient productive maintenance.
The role of maintenance is to ensure that the unit runs with minimum defects and zero accidents, to achieve these various measures have been tried and tested in the commercial world and have shown amazing results.
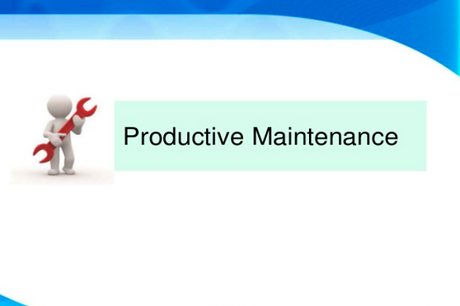
Amongst the few popular ways to reduce maintenance cost, are the TPM maintenance process and the adaptation of planned maintenance software. In most cases, these two methods work hand in hand to ensure the smooth functioning of a production unit. Let's understand each of them in detail.
TPM or Total Productive maintenance is a strategy that aims to achieve an ideal production scenario. The primary aim of this strategy is to ensure that the unit runs without any pauses, i.e. without downtime, without breakdowns and accidents.
How can we achieve TPM?
The good news is that a perfect production scenario can be created with the help of planned maintenance software. It might take time to reach the perfect level, yet as soon as we switch from the outdated method to the modern-day software, we will notice the results.
With the help of technology , companies are directed to move from a reactive maintenance policy to the proactive or preventive maintenance method. This shift helps in managing the production unit more effectively, as the lifespan of equipment is maximised, and the downtimes are cut down to almost zero.
Let's look at some of the benefits that the TPM process offers with the usage of maintenance software.
Empowering the Man Power
The TPM process creates a culture of ownership, where the employees working on a machine is given the responsibility of maintaining the asset, here the machine operators are encouraged to perform the cleaning, lubricating, painting and another maintenance service on their equipment from time to time.
Additionally, since they are working on the machine, spotting errors is easier for them, thus to report any major issue, these operators are provided training on the CMMS mobile software , where they can log issues and escalate in real-time.
Companies like MRC Bearings had reported that they could reduce almost 98 per cent of downtime with the help of the TPM process.
Safety First
The TPM is a well-planned event that lists down all the activities required for maintenance. It primarily focusses on all the major principles of maintenance, which helps achieve the following.
- Well-kept machines ensure the production is clean and of high quality, ensuring that the machines.
- Healthy machines lead to fewer issues, thus reducing downtime.
- With sole ownership of equipment's, the risk of accidents is reduced as operators understand their machines better.
- The unit looks cleaner and clutter-free.
- Work orders are completed on time and with zero errors.
Increase in OEE
OEE stands for Overall Equipment Effectiveness . The TPM method ensures that every asset irrespective of its size or importance is maintained properly.
A typical TPM process involves the cleaning of machines, inspecting the equipment, lubricating it for better functioning, conducting corrective repairs if needed and finally painting the machine. With such maintenance, the equipment lifetime and efficiency are boosted, thus giving better results in terms of productivity .
The Final Word
TPM might sound utopian, but when implemented diligently, it can bring miraculous results. A lot of organizations have adopted this policy and have seen exponential results.