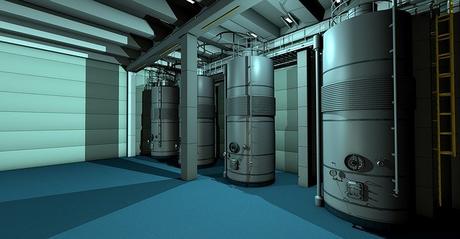
For the optimal functioning of boilers, it’s vital to supply them with treated boiler water. A thorough water treatment program should be in place to ensure that the quality of water entering the boiler is best suited for its operation. To achieve a well-planned water treatment program, the feedwater setup must be taken into account.
What is a feedwater tank?
Essentially, a feedwater setup can be classified as deaerators and feedwater tanks. In the case of the former system, the feedwater is stored in a highly pressurized container that has a dedicated deaerating apparatus.
Feedwater tanks, on the other hand, are storage facilities where the water is heated and has no specific deaerating section. Moreover, it also operated at atmospheric pressure, unlike its highly specialized counterpart. These tanks also serve a whole host of other functions, acting as a receiver for condensation water as well as the entry point for injecting various chemicals in the system.
Due to its importance, feedwater tank design and operation is an extremely vital engineering problem, for it can significantly reduce the efficiency of the boiler and other affiliated systems. In fact, many facilities face a whole host of problems with their feedwater tanks that can be ultimately chalked up to poor design and operation. Here, 4 such common issues and their solutions will be discussed in detail.
Common Problems in Feedwater Tank Design and Operation.
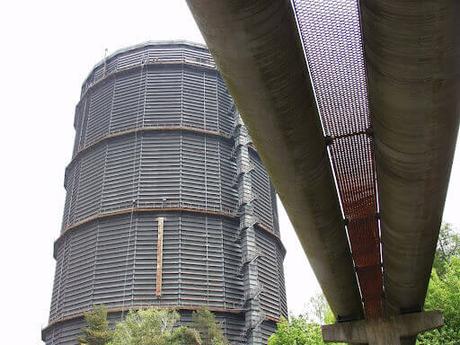
Inadequate Feedwater Heating
Due to a lack of pressure, it is crucial for water in feedwater tanks to be heated before they enter the boiler, for inadequate heating of the feed water can create a massive thermal shock. For the uninitiated, thermal shock is a phenomenon caused by rapid temperature fluctuations that can create undue mechanical stress on the system, even to the point of damaging physical components. Hence, this is a problem that needs to be avoided at all costs.
Fortunately, most well-designed feed tanks have proper heating systems like a steam sparger, a direct-contact heating device where the residual steam from the boiler heats the tank. Moreover, an increase in water temperature will also automatically reduce the oxygen concentration, thereby accomplishing deaeration as well. Ideally, the tank should be maintained in the temperature range of 185°F to 195° F to accomplish this.
After making sure that a solid heating process and control valve is in place, regular inspections are enough to keep the equipment running smoothly. One simple way to inspect is to check the vent discharge and compare the steam generation with the temperature mentioned in the gauge. For example, if the temperature reads 190°F and there is the right amount of steam escaping from the vent discharge, then you know that the system is operating perfectly.
Incorrect Feedwater Pump Location
Another common issue is the incorrect positioning of the feedwater pump in the tank, which adversely affects the quality of water that enters the boiler. The location of the pump is also dependent on the location of the make up.
Make up is basically cold water between the temperature range of 50°F to 80°F that is also being pumped into the feed tank. Hence, having the make up and feedwater pump too close to one another can create uneven heating and aeration.
To solve this problem, simply locate the feedwater pump far away from the inlet of the make up. Ideally, the two should be located on the opposite sides of the tank, so that the cold water has maximum time to get heated and lose its oxygen content before it reaches the pump. Giving this extra time is crucial as water in the tank is rarely ever heated or chemically treated at a uniform rate.
Another great solution is to use a continuous feedwater pump that is equipped with piping and recirculation lines that can send excess discharge back to the tank. Without this recirculation line, a phenomenon known as deadheading can occur, where the flow is hindered or blocked. Lastly, ensure that the recirculation line is attached below the water level to prevent aeration.
Scale Buildup
This is a common issue for not only feed water tanks but any large boiler systems in general. Due to the presence of several contaminants in the water such as silica, iron, magnesium, calcium, aluminum and other particles, these deposits settle down and create hard surfaces once the water has evaporated. Once scaling has begun in a piping system, it’s extremely difficult to remove it and it will slowly deteriorate the entire plumbing.
The amount of scaling is directly proportional to the pressure capacity of a boiler. For example, if you are using a high-pressure boiler, then the feed water needs to be almost entirely free of contaminants to prevent scaling. To achieve this, facilities go for advanced water treatment solutions such as reverse osmosis, deionization, or electro-deionization. Conversely, a boiler operating in a low-pressure setting can simply use sodium-based water softeners to improve water quality and reduce or eliminate scale buildup.
But to remove any guesswork from the equation, it’s best to get details about water purity directly from the boiler manufacturer, and closely stick to their guidelines. If it’s not possible to contact or get this information from your manufacturer, you can alternatively seek guidance from an affiliated engineering organization that would have a set contamination limit for different operating pressures.
Foaming And Priming
Foaming and priming are two problems that often occur in tandem due to one root cause, which is surface-level impurities in the feed water. Basically, when the feed water containing these dissolved solids is heated, the contaminants bubble up along with the steam. This is known as foaming. Once sufficient steam has been generated, these particles also evaporate along with the water, and this phenomenon is known as priming. In systems where boilers are attached to turbines or superheaters, foaming and priming pose a major threat as these evaporated impurities end up latching onto the turbines and reducing their efficiency over time.
Moreover, the problem just doesn’t end with salt deposits on turbines and superheaters, for these impurities can also latch onto piping and other crucial parts of the system, consequently damaging the entire machinery. This problem can be avoided or reduced in two ways, by reducing the level of dissolved solids in the feed water and by ensuring that the solution remains alkaline throughout the operation.
To achieve the first goal, a plethora of processes such as membrane filtration, ion exchange, and various water softening techniques can be employed. To ensure that the water remains alkaline, engineers have to constantly monitor the pH level of the water, which should drop below 8.5, but also should not exceed 9.5.
In Conclusion
Hopefully, addressing these 4 problems and offering solutions will improve the efficiency of the boiler and the entire system of your facility. If you follow these tips diligently, then you can significantly drive down maintenance costs in the long run, for that is the primary goal of addressing these issues.
Author’s Bio:
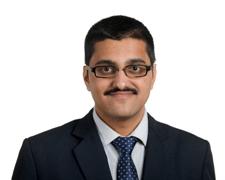
Dhruv Mehta is a Digital Marketing Professional who works as a brand consultant and provides solutions in the digital era. In his free time, he loves to write about marketing, finance & tech. Reach out to him on Digital Dhruv or connect with him on LinkedIn.