The need for contract packaging is growing in the Consumer Packaged Goods (CPG) industry. Manufacturers are more narrowly segmenting the consumer marketplace while retailers seek differentiation through the products they stock. These factors drive a seemingly unending need for additional products and SKU’s. These more complex product lines call for added packaging capability and capacity, often through growth of contract packaging.
One might think that as contract packaging becomes more widespread in supply chains, its costs would become more consequential, which would lead to more precise decisions about selecting a contract packer. After all, the same factors that influence where a manufacturing plant is located would seem to be relevant in selecting a packaging location; i.e., packaging cost, proximity to sources of supply, proximity to markets, breadth of capability, and inventory and distribution costs would all seem to be pertinent. Pertinent . . . yes, but unfortunately, not often considered . . . at least in any meaningful manner.
Where should packaging be done?
The default answer to this question is typically – near the manufacturing plant supplying the component materials. If that’s not practical, then the choices devolve to locations where the right type of packaging capability exists, with available capacity, and with the required quality standards. At some level, this logic is perfectly clear and makes sense. However, in situations where more than one location can do the work, this logic is insufficient and can lead to decisions that actually cause inefficiencies.
Here is a case to consider:
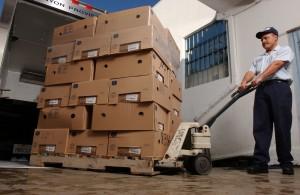
Other locations, specifically Atlanta and Dallas, were not considered, even for regional supply. The decision was based solely on packaging criteria. It was blind to supply chain considerations. The missing factor in this, all too frequent, scenario is the concept of “landed cost.” To some, perhaps many, the concept of “landed cost” is nothing new; but it’s often not considered in the packaging location decision. The concept is either ignored by making decisions based solely on packaging criteria or the concept is neutered by using non-specific “plug values” for important cost drivers, such as transportation. Any practice that dismisses a “landed cost” approach risks a bad decision.
Consider again, the food manufacturer in Kentucky. A landed cost analysis shows that transporting product to Chicago for packaging, only to ship the finished product back to the Southeast is expensive. An Atlanta location provides considerable savings.
“Landed cost,” a factor in many supply chain decisions, has a role in the packaging location decision. No doubt, there are barriers to its use, not the least of which is organizational structures and siloed responsibilities. But with its acceptance and use come better decisions and much more efficient supply chains to handle more complex product lines.
So when choosing a packaging location, consider these questions to help you make a better decision:
- Can the packaging be done in more than one qualified location?
- Are full supply chain costs considered in the decision making – inbound transportation, packaging, warehousing, outbound transportation?
- Are the cost estimates “plug” numbers or an estimate of the market?
If either of the last two questions is answered with a “no,” then the packaging location decision may not be optimal. While determining true landed cost requires more diligence, taking the time to work through this analysis can lead to better decisions and have a positive impact over the entire supply chain.
Click here to learn more about packaging.
Written by Paul Lomas, Group Director, Consumer Packaged Goods, Ryder Supply Chain Solutions
Paul Lomas brings 30+ years of supply chain experience. In his current role, Mr. Lomas leads the Business Development function for the Consumer Packaged Goods Group within Ryder’s Supply Chain Solutions division. Prior to this role, he was responsible for Supply Chain Excellence for the Consumer Packaged Goods group. He joined Ryder as part of the TLC acquisition, where he held roles of increasing responsibility in the areas of business development, engineering, IT, and operations. Previously to joining TLC, he did some consulting work with Accenture and Cleveland Consulting Associations and also held positions responsible for Materials Management at General Motors.