Back in January, I took a lapidary class with Michael Boyd, who is a lapidarist and jewelry designer based out of Colorado. It was an intense 5-day workshop (complete with candy breaks!), and I learned so much. For anyone not familiar with the term, lapidary work centers on the cutting and polishing of stones.
Michael brought a whole slew of stones with him, and taught us what to look for with regards to color and inclusions. It’s pretty amazing to see what the rough forms of stones look like – some were pretty ugly!
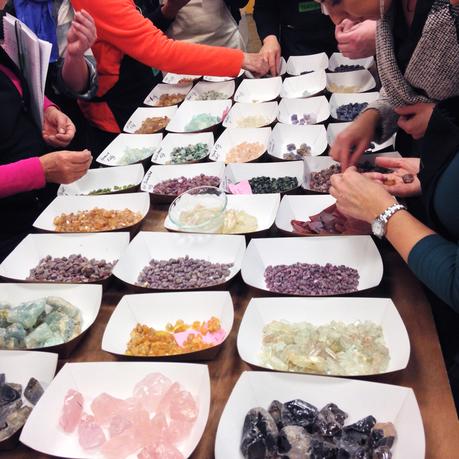
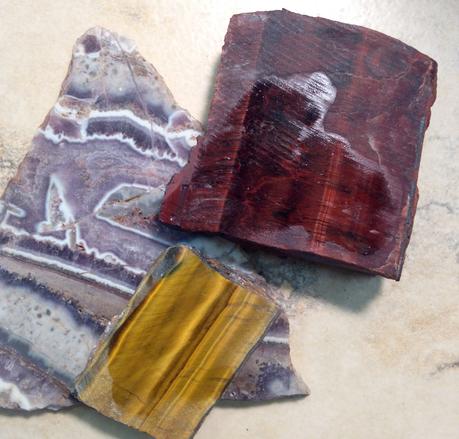
At the start of class, we all got a basic kit like this (well the safety glasses were my own).
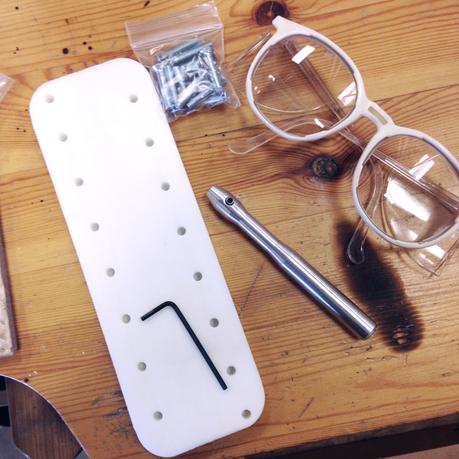
Here are a couple before/after shots of stones that I worked on during the workshop.
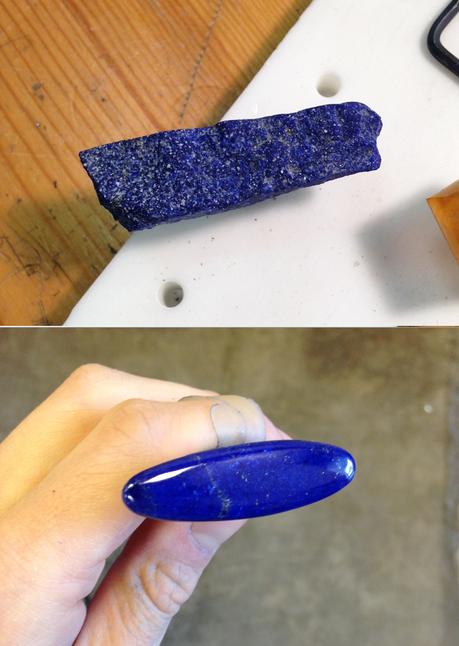
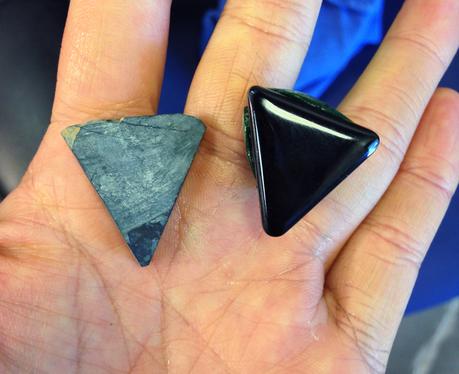
So…why would you cut your own stones? Well, it’s way cheaper than buying them cut from someone. And you can customize the stone to fit your design. Michael’s view is that if you’re going to spend a lot of time making a-one-of-a-kind piece of jewelry, why use a generic/store bought stone? In his work, he finds ways to make the stone unique. This may mean custom shapes, or it might mean he drills a hole through a big stone and sets a smaller one to fit on top. Or maybe he polishes a stone, carves a divet in it, and then hammers gold wire to create something like these stones (which he then uses for necklaces, rings, etc).
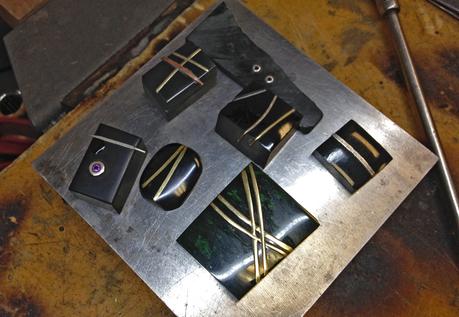
I love how innovative he is with his work, and how he encouraged us to experiment with our own projects. He told us to not be afraid of trying new things or of messing something up. After all, the goof ups sometimes lead us to discover something even better!