Just as density exists in every element in the periodic table of elements, logistics density is also everywhere in the world of supply chain management. Logistics density can be discovered in the route design of inbound manufacturing logistics, in service parts logistics within the distribution center and in finished vehicle logistics in the load factor used per railcar or over the road carrier. But what is logistics density? How do you find it in your supply chain and how can it impact your overall costs? Let’s review how you can apply logistics density in the automotive industry.
What is Density?
Density is defined as a quantity per a unit of space. Some of the more common measurements of density are pounds per cubic volume or population per square mile. So how can we extend this definition to logistics?
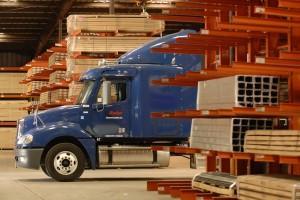
When applying the term density to logistics, we are really talking about the distribution of a unit of something, but instead of using mass and population, think instead of suppliers, dealers, and vehicles. Think of stops as the numerator. And for your denominator, replace volume and square miles with routes, ports, railheads and shipments. Let’s look at two common examples of “logistics density” – LTL freight classification and transportation modes themselves.
Logistics Density
Less-than-truckload (LTL) freight classification is the breaking down of a shipment based on its density. The way density is classified is by weight per volume – the heavier a shipment per volume the higher the density which results in a lower freight classification. Lighter shipments will be less dense but have a higher freight classification. For example, when you think of heavy materials such as metals or batteries, these may have a lower classification at 60, but they are actually denser.
When a transportation mode is designated for a shipment, this is often a reflection of that shipment’s density. Say you are transporting oil, the densest way, or best way, to transport this would be through a pipeline. Now, if you transport this over ocean, the shipment becomes less dense, because you are limited to space and structure, making it a more difficult and expensive shipment. So as you move across different modes of transportation density changes: pipeline being the densest and air being the least dense. Think of it this way, the more product you can move at a time, the higher the density.
When it comes to the automotive industry, there is a wealth of examples that support the need to identify and measure logistics density. In this industry, logistics density is used to determine the transportation need, whether it be truckload (TL), a milkrun, or an LTL route. If one shipment has enough material, or density, to fill a truck, then truckload is chosen. Milkruns are chosen when there are enough suppliers within a geographic region to support a route. If the density of suppliers and freight are lacking, then LTL is chosen.
In the world of service parts, the geographic placement of the distribution center is determined using density. As the number of distribution centers increases, so can the number of dealers located within a certain distance and transit time of that location. Here, density is measured as the amount of dealer’s located within a specific radius or the amount of dealer’s over transit hours.
In the finished vehicle logistics arena, the most familiar form of logistics density measurement is load factor – the number of vehicles per railcar, ocean vessel or trucking carrier. Every improvement made to the load factor of the equipment is an attempt to increase the logistics density in that network.
Your overall goal should be to increase logistics density, meaning you are increasing your utilization of space in any given transportation mode. This will result in reduced costs, because you can reduce the total amount of shipments as well as pay reduced rates.
Finding Logistics Density in the Supply Chain
So know that we think we have defined logistics density, how do we find it? The first step is to gather necessary data, such as information about the product being moved, existing routes, dealer information as well as information about the current contract in place. Then you will need to analyze this data to find the logistics density in your network. Utilizing visual data management tools and network optimization tools will streamline the process of determining the current state and then finding alternatives by creating different scenario analyses. This final step is probably the most difficult, as it requires all stakeholders to come to agreement on an alternative and then moving forward with an implementation.
Tools That Help Measure Logistics Density
There are many tools available to help you measure the logistics density in your network. Using a visual data management tool, such as Tableau, you can visually map out and see the density in your network. For example, you can illustrate port activity based on the types of vessels and the type of cargo handled on each. This will help identify which ports are more Roll-On Roll-Off (RORO) friendly. You can also use this data to create distribution maps by state and dealer to identify where there are existing opportunities to increase your network’s logistics density.
You can also use network optimization tools which will allow you to take all the necessary data, such as plant locations, rail networks, ports and auto carrier networks and create models for mode changes from truck to rail or vice versa. You can also use these tools to determine railhead and port assignments.
So by visualizing and optimizing logistic densities in the finished vehicle logistics realm we can reduce overall supply chain costs, increase equipment and resource utilization and optimize the transportation logistics plan at a plant, regional or network level.
Now that you know what logistics density is and the impact it can have on your supply chain, how will you go about measuring it in your own network?
Written by Tom Kroswek, Senior Director SCE Automotive, Ryder
Mr. Kroswek is a logistics and engineering professional with 28 years of experience in supply chain engineering, transportation analysis, and inbound manufacturing support. Throughout his career, Mr. Kroswek has worked in design, supply chain analysis, sales, project management and operations management.
Mr. Kroswek has a unique blend of experience from both the operational and corporate support environments. In his role as Senior Director of Supply Chain Excellence for Ryder System, Inc., Tom leads the engineering, quality management and program management activities for the Automotive, Aerospace and Industrial team of Supply Chain Services. Mr. Kroswek was the lead inventor for Ryder’s patented Logistics Release, a proprietary process and technology to control material flow to line-side..