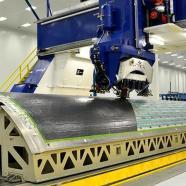
What You Need to Know About Composite Manufacturing
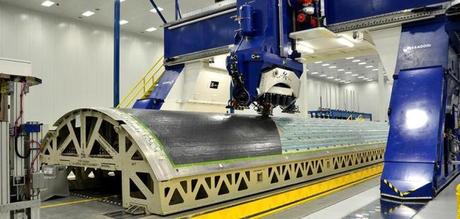
The need for lightweight, economical, durable and, at the same time, flexible solutions for many branches of the economy make composite materials a logical and easy choice for countless sectors of the manufacturing industry. They are an ever-rising trend when it comes to creating the building blocks of automotive components and aircraft structures, for example, uniting the best qualities you can find in different traditional materials. Let's take a look at their characteristics and benefits, which can help us understand why they are so widespread and preferred.
First, A Definition
In their essence, composites are a mixture, obtained by combining two or more elements of either natural or artificial origin. These elements need to have different physical and chemical properties that would complement and enhance each other, contributing to the unique qualities of the output compound.
The characteristics of the raw material are not changed or lost, they are enhanced by the combination. Putting different elements with varied individual traits is done on purpose with a practical end in mind - the final product will be stronger, more efficient or durable than the sum of its parts.
What Composites Are Made Of
Composites are made of a polymer matrix that is fortified and reinforced by an either artificial or natural reinforcing fiber element. It's the matrix that serves as environmental damage protection and load distribution. Fibers, on the other hand, provide additional strength to the matrix, diminishing the likelihood of cracks and breaks.
The manufacturing process is rather long and complex but if you are interested in finding out more about the various processes involved, this is a great guide and contains plenty of information. Suffice it to say that the main components are usually two. There could, of course, be any kind of additional filler or appearance enhancer based on the industry it is going to serve, but a mixture of fiber and resin make up the basis of most composite products.
Advantages of Composite Materials
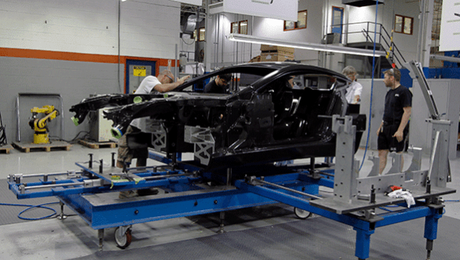
Inarguably the greatest benefit of composite materials is their high stiffness and strength as compared to the weight. They are around two-thirds lighter than an aluminum component of the same size, while offering the same sturdiness and stability. Adding to this the ease with which the material can be bent and molded, and we have a great resource for engineering purposes.
The flexibility with which a matrix is used to form complex shapes without the help of special tools can be attributed to the fact that the geometry of the object is created as it goes solid. It is also very durable, and can be safely exposed to dampness, heat, radiation and various other outside influences without suffering damage or losing its properties.
A Word on The Disadvantages
Since they are so difficult to break, these materials make it very difficult to tell whether an interior structure has suffered any damage. This is probably the greatest shortcoming engineers are facing when using composite outer layers for their structures. An aluminum one will dent really easily, leaving enough clues about the state of the whole. This is probably the single greatest problem when using such mixtures. Repair jobs for composite surfaces are in turn pretty difficult, which also means they generally tend to be more costly.
The resin used in composite manufacturing tends to be affected by much lower temperatures than other traditional materials. It starts to weaken at around 150 degrees, so a fire could have utterly devastating effects on a composite part. Apart from the fact that burning results in the danger of inhaling toxic substances emitted by the resin, higher temperatures mean the structure can sustain irreparable damage.
Challenges in Composite Manufacturing
Despite the fact that composites bring numerous advantages to the various industries that employ them, there are also some challenges that are hard to ignore, experts from http://sparteccomposites.com share. The drawbacks put a brake on the sector's otherwise rapid rate of development, as some of them are still quite tricky to tackle in the immediate future.
The fact that traditional materials, such as plastic and aluminum are much cheaper than composites is huge. Added to that is the obstacle of the difficulty of automating all manufacturing processes, so it turns out we have an expensive product that often needs to be created manually. There is also the issue of standards, created for the use of traditional materials in some industries, such as ship building, for example. These standards are so strict and specific that composites fall short for trivial reasons. The good news is that there are some newer programs that have now started implementing automation in composite parts production successfully. This increase hopes of kick-starting mass production in every branch of the industry.
Uses
Both commercial and residential building companies make use of composites to replace the good old wooden frame we are all familiar with. A coat of plastic in the mixture ensures the frame will not be susceptible to damp, rot and termites, thus extending the structure's life expectancy considerably. Any outdoor elements that are exposed to harsh weather conditions benefit from a composite make. Just imagine not having to fix your roof for decades to come or maintain it in any other way, either.
The aircraft and automotive industries make the most of composites' lightweight quality, which ensures considerable fuel economy that does not involve a compromise in terms of stability in the sky or on the road, where durability is a must, as human life and safety are involved. Water vessels today are very rarely made of rotting wood or heavy metal that's bound to rust. Thermoplastics and fiberglass ensure that the boat stays afloat and doesn't suffer cracks or other forms of damage or corrosion, despite the frequent contact with salt water and air.
Last but not least, composites are amazing when it comes to making bulletproof jackets and other ballistic protection items and devices. Certain pieces of body armor offer protection from flames and certain explosives as well, thus saving thousands of lives and preventing grave injury.