When you are searching for answers on how to improve your supply chain, you will find an array of sources that speak to different strategies and tactics that can be implemented to help. But there is one common theme you will always come across: visibility. But what does “visibility” mean? And why is it so important?
What is Supply Chain Visibility?
Supply chain visibility is the ability to identify, capture and share events and transactions as they develop and to store that information for historical record and reporting. It is crucial for all stakeholders to know where things are coming from, where they are at specific times and where they are going.
But visibility for visibility’s sake is not effective, unless you can dive down to very specific detail needed to make decisions, such as reference points at the item level. Item level detail allows the end user of the data collected to reference the exact element that they need to track, trace and follow through the business processes supporting the supply chain – and enact quick responses when exceptions to the plan occur. Having this kind of visibility can act as a competitive advantage because it arms companies to be able to react quickly to unexpected situations and emergencies, sometimes enabling companies to outperform competitors.
Using Reference Levels
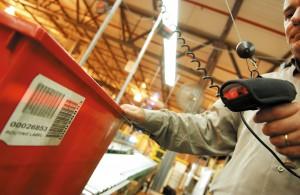
In the retail and consumer packaged goods markets visibility needs to be at the SKU level to be useful. The amount of product in the supply chain, on store shelves, in the warehouse, in transit or being returned can be more effectively tracked at the SKU level. By using this reference, the value of visibility is increased and decisions can be made in a much timelier way. Reduced inventory levels, increased stock and shipping accuracy, and lower total landed costs are all results of a SKU level reference increasing the visibility in these segments.
Benefits of Increased Supply Chain Visibility
The value of supply chain visibility is in the ability to capture information at an item level and improve the overall business processes supporting the supply chain because of it. The ability to track, trace and manage inventory, support returns and confirm the authenticity and quality of the product is enhanced when supply chain visibility is referenced at an item level detail. Having supply chain visibility also makes your company more reliable and responsive, which in turn will increase your customer satisfaction.
How is your company currently achieving supply chain visibility? What reference levels are you using?
Written by Tom Kroswek, Senior Director SCE Automotive, Ryder
Mr. Kroswek is a logistics and engineering professional with 28 years of experience in supply chain engineering, transportation analysis, and inbound manufacturing support. Throughout his career, Mr. Kroswek has worked in design, supply chain analysis, sales, project management and operations management.
Mr. Kroswek has a unique blend of experience from both the operational and corporate support environments. In his role as Senior Director of Supply Chain Excellence for Ryder System, Inc., Tom leads the engineering, quality management and program management activities for the Automotive, Aerospace and Industrial team of Supply Chain Services. Mr. Kroswek was the lead inventor for Ryder’s patented Logistics Release, a proprietary process and technology to control material flow to line-side.
Tom joined Ryder in 1992 as a logistics analyst and has assumed positions of greater responsibility within the Automotive Supply Chain Services team. Prior to joining Ryder Integrated Logistics, Mr. Kroswek started his career and worked 6 years in the logistics industry in various roles with Frito- Lay, Inc.