The supply chain offers tremendous opportunity to improve productivity through the principles of Lean Labor Management. Warehouse managers usually agree on the two main challenges faced in their facilities:
- Workforce turnover
- Variation and fluctuation in activity levels
Fortunately, the implementation of Lean Labor Management strategies can greatly reduce inefficiencies resulting from these challenges.
A Lean Warehouse Retains Employees
Employee turnover can be a costly and on-going problem in many facilities. A constantly changing staff makes it difficult to reach productivity goals. The process to recruit, hire, and train new employees is lengthy and expensive and requires precious time from managers who should be on the floor. Often, months are needed for new hires to work at optimal levels with low error rates.
Lean warehouse environments benefit from lower turnover rates.
Because Lean Labor Management begins with empowering employees to identify and root out waste, this attitude creates an environment where all employees—management and hourly staff—are working toward a common goal. When employees feel they are part of the overall solution, they come to work with a sense of pride. Lean facilities are well organized and clean, creating positive and safer work environments. Typically, employees in this type of facility are less likely to look for other places to work.
Lean Tools to Address Warehouse Flux
All facilities experience fluctuations in inventory and activity throughout the annual cycle, which cause staffing challenges. Too many workers in an area create waste, and too few can lead to delayed fulfillment or costly overtime.
How does lean alleviate fluctuation challenges?
When lean principles are implemented, management and hourly employees are working together to lower costs, improve quality, and reduce lead times. Lean visual tools, such as boards or TV screens showing work in progress, can help accomplish this goal by making problems in the system more evident. These lean tools create a “visual factory” to root out waste and identify successes. Additionally, these boards can create clearly defined expectations for specific tasks—an essential component of Lean Labor Management. For example, specific metrics can be identified for action items such as load times and pick times. All of this combined data will ultimately help managers understand the staffing requirements of various warehouse activities, to schedule and assign workers to achieve optimal efficiencies.
Following is a list of useful Lean visual tools:
- Lean Signage
- Lean Storyboards
- Quality Walls
- Workplace Organization Diagrams
- Dashboards
- Status-At-A-Glance Boards
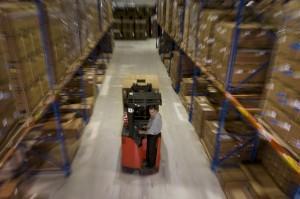
To learn more about Lean Labor Management in warehouses, watch SupplyChainBrain’s Video Interview of Bob Arndt, Vice President of Lean Supply Chain Solutions for Ryder here.
Written by Robert Arndt, Vice President of Lean Supply Chain Solutions