Why wage inflation in Asia is fueling a “Made in the USA” comeback.
15 to 20 years ago, moving manufacturing operations to China was the thing to do. And for good reason. Wages were significantly lower, the pool of skilled workers plentiful and land cheap. Sourcing in China also made sense because of the country’s robust logistics infrastructure, political stability and sound raw materials supply chain.
However, continuing demand for that ultra-low-cost labor steadily pushed wages ever-higher. Many companies, looking to keep production costs low, moved operations from one low-wage destination to the next. As development in one Asian offshoring location reached maturity, manufacturers would move on to the next underdeveloped country. This “traveling circus” model worked as long as the difference in wages was large enough to make offshoring make sense. [1]
Today, the cost-benefit calculus of manufacturing in China has changed dramatically. Wages are rising at a brisk clip, at about 15 to 20 percent every year, according to The Boston Consulting Group (BCG). The cumulative total? HSBC research confirms that real wages in China have risen some 350 percent over the last decade.
According to the Bureau of Labor Statistics, wages are rising faster in China than they are in the U.S. The rise can be attributed to more than a shrinking labor pool. To control income inequality, China is expected to raise its minimum wage to 40 percent of the average salary by 2015.[2]
Rising wages, a shrinking workforce and high global oil prices
Meanwhile, that infinite pool of affordable skilled labor isn’t what it once was. The workforce has become less loyal as younger workers show diminishing interest in factory jobs. Meanwhile, wages for technical and supervisory jobs are reaching parity with their American counterparts. All as high global oil prices drive up shipping costs and erase any remaining labor savings.
For some companies, the short-term solution is to move to China’s interior, where wages are less than half those of booming coastal regions. However, there are tradeoffs. The deeper you travel into China’s rural provinces, the more primitive the infrastructure, the higher the transportation costs and the less skilled the workers. All three factors can negatively impact delivery times.
Other companies are shifting operations to Vietnam and the Philippines or adding sites in other low-wage destinations. As they do, they wrestle with many of the same deficiencies as inland China: less skilled workers, language barriers and issues with infrastructure and technology.
What does it mean? It means on-shoring is looking like a viable solution.
Suddenly, the economics of manufacturing in China, Taiwan and Malaysia aren’t quite as compelling as they once were. As wages rise in China and companies win concessions from labor unions in the U.S., manufacturers are doing something that would have been unthinkable a decade ago. They’re bringing manufacturing back to the United States. A recent cover story in Time Magazine reported that American manufacturing growth is currently outpacing that of other advanced nations with some 500,000 jobs created in the last three years.
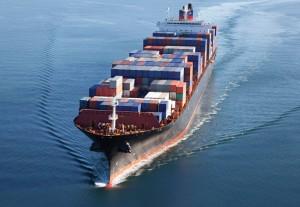
In fact, the Boston Consulting Group predicts that within a decade, China will have 20 cities the size of New York, exacerbating pressures on its labor force. At home, energy costs will continue to fall, workers will hone their skills and production will expand across America. The result? The end of the boomtown in offshore manufacturing in China and an exciting decade for on-shoring: to the tune of $100 billion worth of manufacturing returning to the United States.
Written by Lee Williams, Ryder Supply Chain Solutions
Lee Williams is a Director of Business Development for the Retail Division of Ryder Supply Chain Solutions. Lee’s background and experience includes international logistics, international freight consolidation and Asia origin services.
[1] Presentation by Edwin Keh, Wharton School of Business, “The New Global Supply Chain for the Next Century”/H K Rita, The Hong Kong Research Institute of Textiles and Apparel
[2] CNN Money, February 2013