Use these three simple strategies to improve efficiency and get bottom-line results.
If you’re responsible for workforce planning, one of the biggest challenges you face is balancing the need for more manpower with continuing pressure to control costs. This is especially true in the retail arena, where demand can fluctuate wildly, making managing costs, labor and productivity a tricky proposition.
Meeting consumer demand and getting products to market on time means being able to ramp up when demand spikes and dial back during off-peak periods or downturns. So how do you get the most value for your workforce investment and save on labor costs? In two words: work smarter. Here are three proven ways to lower the asset costs associated with labor and turn up your productivity and profitability.
1. Save money with a flexible labor pool
Whether you’re in the retail, consumer packaged goods, high-tech/electronics or food and beverage business, you could probably benefit from having a flexible workforce. Sure, it’s important to have a core group of employees who know your company, processes and expectations. But, increasingly, it’s equally important to complement that permanent staff with a contingent labor pool. Nurturing a flexible labor pool is also preferable to laying workers off when business slows and rehiring when it picks up.
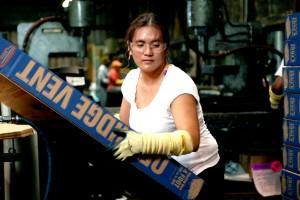
2. Work smart by implementing Lean labor management
Another way to shave costs is to apply a Lean labor approach to warehousing functions. With origins in manufacturing, Lean principles improve efficiency by standardizing tasks, processes and the use of technology/materials handling systems. A Lean culture also helps you improve time utilization and set performance goals and then reward employees for exceeding them. Whether your operation is manual or automated, these factors can drive tremendous throughput increases and/or labor cost reductions.
3. Do more with your resources by cross training your staff
Here’s another way to reduce costs (hint, it happens to be an integral part of Lean labor management): set up cross training or job sharing programs. Your workforce is much more flexible when you cross-train employees and then move them to wherever you have the greatest need. This might mean sharing a staff member with another department or simply making sure many of your workers are trained to do different jobs. When demand slows in one area, you can allocate them to another.
With these three strategies, you’re well on your way to reducing labor costs, while ensuring that you have the resources you need to ramp up or down quickly based on shifting consumer demand or changing market conditions. Could these labor management practices help you make the most of your labor resources, while reducing costs? Would you like to find out more?
To learn more about how you can lower assets costs associated with labor, and the importance of the involvement of the people in your operation, read Part 1 of our Lean Guiding Principles White Paper Series on People Involvement.
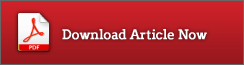