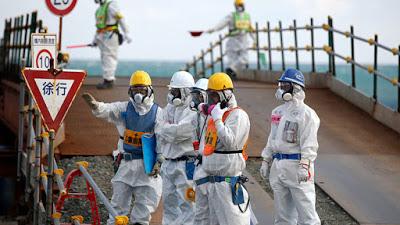
How can industries involving processes that create large risks of harm for individuals or populations be modified so they are more capable of detecting and eliminating the precursors of harmful accidents? How can nuclear accidents, aviation crashes, chemical plant explosions, and medical errors be reduced, given that each of these activities involves large bureaucratic organizations conducting complex operations and with substantial inter-system linkages? How can organizations be reformed to enhance safety and to minimize the likelihood of harmful accidents?
One of the lessons learned from the Challenger space shuttle disaster is the importance of a strongly empowered safety officer in organizations that deal in high-risk activities. This means the creation of a position dedicated to ensuring safe operations that falls outside the normal chain of command. The idea is that the normal decision-making hierarchy of a large organization has a built-in tendency to maintain production schedules and avoid costly delays. In other words, there is a built-in incentive to treat safety issues with lower priority than most people would expect.
If there had been an empowered safety officer in the launch hierarchy for the Challenger launch in 1986, there is a good chance this officer would have listened more carefully to the Morton-Thiokol engineering team's concerns about low temperature damage to O-rings and would have ordered a halt to the launch sequence until temperatures in Florida raised to the critical value. The Rogers Commission faulted the decision-making process leading to the launch decision in its final report on the accident (The Report of the Presidential Commission on the Space Shuttle Challenger Accident - The Tragedy of Mission 51-L in 1986 - Volume One, Volume Two, Volume Three).
This approach is productive because empowering a safety officer creates a different set of interests in the management of a risky process. The safety officer's interest is in safety, whereas other decision makers are concerned about revenues and costs, public relations, reputation, and other instrumental goods. So a dedicated safety officer is empowered to raise safety concerns that other officers might be hesitant to raise. Ordinary bureaucratic incentives may lead to underestimating risks or concealing faults; so lowering the accident rate requires giving some individuals the incentive and power to act effectively to reduce risks.
Similar findings have emerged in the study of medical and hospital errors. It has been recognized that high-risk activities are made less risky by empowering all members of the team to call a halt in an activity when they perceive a safety issue. When all members of the surgical team are empowered to halt a procedure when they note an apparent error, serious operating-room errors are reduced. (Here is a report from the American College of Obstetricians and Gynecologists on surgical patient safety; link. And here is a 1999 National Academy report on medical error; link.)
The effectiveness of a team-based approach to safety depends on one central fact. There is a high level of expertise embodied in the staff operating a surgical suite, an engineering laboratory, or a drug manufacturing facility. By empowering these individuals to stop a procedure when they judge there is an unrecognized error in play, this greatly extend the amount of embodied knowledge involved in a process. The surgeon, the commanding officer, or the lab director is no longer the sole expert whose judgments count.
But it also seems clear that these innovations don't work equally well in all circumstances. Take nuclear power plant operations. In Atomic Accidents: A History of Nuclear Meltdowns and Disasters: From the Ozark Mountains to Fukushima James Mahaffey documents multiple examples of nuclear accidents that resulted from the efforts of mid-level workers to address an emerging problem in an improvised way. In the case of nuclear power plant safety, it appears that the best prescription for safety is to insist on rigid adherence to pre-established protocols. In this case the function of a safety officer is to monitor operations to ensure protocol conformance -- not to exercise independent judgment about the best way to respond to an unfavorable reactor event.
It is in fact an interesting exercise to try to identify the kinds of operations in which these innovations are likely to be effective.
Here is a fascinating interview in Slate with Jim Bagian, a former astronaut, one-time director of the Veteran Administration's National Center for Patient Safety, and distinguished safety expert; link. Bagian emphasizes the importance of taking a system-based approach to safety. Rather than focusing on finding blame for specific individuals whose actions led to an accident, Bagian emphasizes the importance of tracing back to the institutional, organizational, or logistic background of the accident. What can be changed in the process -- of delivering medications to patients, of fueling a rocket, or of moving nuclear solutions around in a laboratory -- that make the likelihood of an accident substantially lower? (Here is a co-authored piece by Bagian and others on the topic of team-based patient safety in the operating room; link.)
The safety principles involved here seem fairly simple: cultivate a culture in which errors and near-misses are reported and investigated without blame; empower individuals within risky processes to halt the process if their expertise and experience indicates the possibility of a significant risky error; create individuals within organizations whose interests are defined in terms of the identification and resolution of unsafe practices or conditions; and share information about safety within the industry and with the public.